Protolabs ouvre de nouvelles perspectives avec l’adoption de la technologie DLS de Carbon 3D
Protolabs, leader mondial de la fabrication numérique, augmente sa capacité de production et renforce son expertise en fabrication additive avec l’introduction de la technologie Digital Light Synthesis de Carbon 3D et du matériau rigide EPX 82 dans la région EMEA.
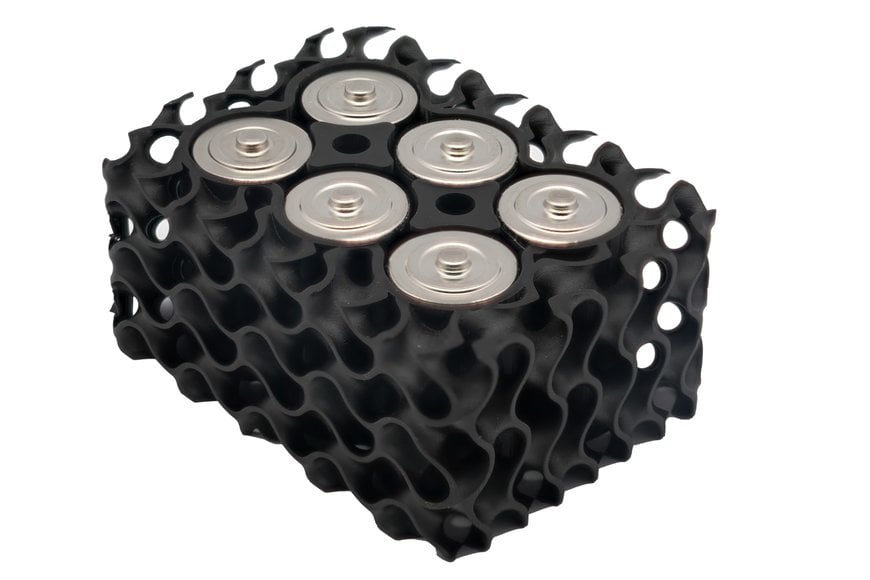
Cette technologie de pointe offre une solution innovante pour la production en série de composants plastiques fonctionnels. En alliant la précision de la technologie DLS™ de Carbon 3D à des matériaux certifiés, Protolabs ouvre de nouvelles perspectives aux industries nécessitant des pièces rigides et durables. Afin de permettre à ses clients d’exploiter pleinement cette technologie révolutionnaire et d’optimiser la conception de leurs projets, l'entreprise a mis en place un service consultatif complet, conçu comme un véritable département R&D externe.
Vers une production en série aux possibilités infinies
L'intégration de la technologie DLS™ de Carbon 3D et du matériau EPX 82 représente un tournant majeur pour Protolabs en France. Désormais, l’entreprise est en mesure de produire des pièces en plastique directement utilisables en production de masse, sans avoir recours aux moules d’injection traditionnels, ce qui simplifie considérablement le processus de fabrication. “Cette innovation ouvre des opportunités inédites pour nos clients, notamment dans les secteurs de l’industrie et de l’automobile en leur offrant une flexibilité et une réactivité sans précédent”, explique Romuald Chasseur, directeur France de Protolabs. Grâce à cette avancée, Protolabs accompagne les entreprises françaises dans l'adoption de solutions de fabrication additive à grande échelle, renforçant ainsi sa position de leader tout en répondant aux besoins spécifiques de chaque secteur industriel.
Performance, durabilité et vitesse : les avantages du procédé DLS
La technologie DLS permet une vitesse d'impression nettement plus rapide que le balayage laser séquentiel utilisé en stéréolithographie conventionnelle (SLA) ; dans le procédé DLS™ de Carbon 3D, une résine polymère liquide est durcie en continu grâce à une projection de lumière ultraviolette à travers une fenêtre perméable à l'oxygène, située dans un réservoir de résine UV. À chaque nouvelle couche, la plateforme de construction s'élève pendant qu'une nouvelle image UV est projetée.
Les composants imprimés en 3D à partir du matériau EPX 82 se distinguent par leur robustesse, leur durabilité à long terme et leur grande qualité de surface Leurs propriétés mécaniques sont comparables à celles de matériaux comme le polybutylène téréphtalate chargé à 20 % de fibres de verre (PBT-GF20) ou le polyamide 6 chargé à 15 % de fibres de verre (PA6-GF15). Grâce à sa haute résistance chimique et thermique, jusqu'à 130°C, l’EPX 82 est adapté à une large gamme d’applications. Ses faibles émissions de gaz et sa longévité, même sous des variations importantes de température et d'humidité, sont des avantages supplémentaires. En plus de l’EPX 82, Protolabs propose également d'autres matériaux de sa gamme Carbon, comme l’EPX 86FR, le polyuréthane rigide FPU 50 et le RPU 70.
Optimiser la production grâce à un accompagnement personnalisé
L’un des facteurs clés de réussite pour la mise en œuvre de cette nouvelle technologie est l’accompagnement complet offert par les experts techniques de Protolabs à travers un programme de conseil personnalisé. Dès les premières phases de consultation, la faisabilité de la production avec la technologie DLS™ de Carbon 3D est soigneusement évaluée, permettant ainsi de créer des modèles parfaitement adaptés au processus d'impression.
“Étant donné que cette technologie est encore méconnue pour de nombreux clients, nous anticipons les questions liées à son utilisation pour la production en série”, explique le Dr Philipp Amend, directeur de l’ingénierie des procédés 3D Protolabs, en Allemagne. Si le matériau EPX 82 satisfait aux exigences des composants, Protolabs collabore alors étroitement avec le client pour développer un procédé de fabrication sur mesure. Ce procédé, validé par des tests d’impression et optimisé si nécessaire, permet une production immédiate, réalisée en un temps nettement inférieur à celui des méthodes traditionnelles.
Des opportunités pionnières pour l'industrie
“Ce n'est pas la première fois que Protolabs réussit à rendre des technologies accessibles d'une manière que même les fabricants pensaient impossible”, se félicite le groupe. Outre la flexibilité de conception propre à l'impression 3D, les clients de Protolabs bénéficient avec cette technologie des nombreux avantages de la fabrication additive, comme une rapidité de production accrue et la possibilité d'imprimer plusieurs variantes sans nécessiter d'outillage. Tout cela en atteignant des volumes communs à la production en série, généralement réservée aux méthodes de fabrication traditionnelles !
Cette évolution n'a pas seulement un impact majeur pour un grand nombre d'industries, elle redéfinit également les limites de la fabrication additive. Avec cette avancée, Protolabs fait une fois de plus de la fabrication additive une norme industrielle pour la production de masse, tout en rendant les avantages de l'impression 3D accessibles à un public plus large.
www.protolabs.com