www.industrie-afrique-du-nord.com
18
'11
Written on Modified on
Production de récipients en verre à usage pharmaceutique contrôlée par système de vision
La société SPAMI, qui fait partie du Groupe Stevanato, a mis au point un système d'inspection pour améliorer la qualité de sa production. Elle opère un contrôle des tubes de verre à l'arrivée à l'usine ainsi que sur le produit final. Le système comprend un système d'inspection visuelle (NoVIS), un système de mesure continue de la température, ainsi qu'un système de traitement d'images numériques, appelé CLEANER, qui est capable de détecter et éliminer les défauts dans le produit final en verre aussi petits que quelques microns. Le processus, entièrement intégré, fournit la mesure du diamètre du tube de verre et l’épaisseur de la paroi, ainsi que la température à l'aide pyromètres infrarouges afin de garantir un contrôle total de la qualité, alors que les brûleurs motorisés fournissent remontent une information précise de leur positionnement. Ce système offre à Stevanato un avantage en termes de qualité, par rapport aux autres fabricants de flacon. Pour ce système de pointe, S.P.A.M.I. utilise les convertisseurs Anybus HMS pour la connexion entre les appareils d'inspection visuelle et les automates de contrôle des lignes de production.
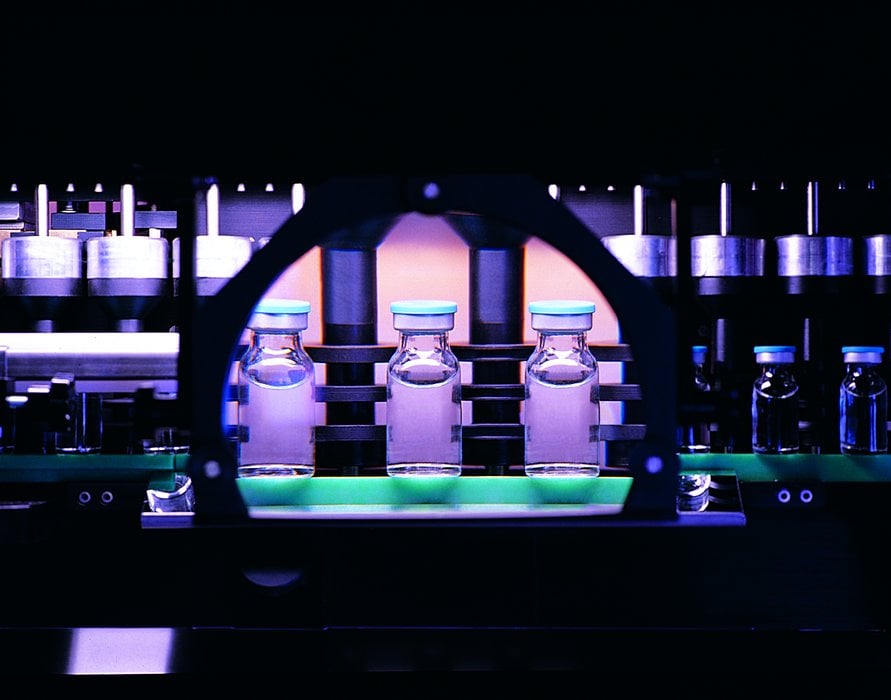
Fondée en 1949 dans une région à forte tradition dans l'art de la verrerie, le groupe Stevanato est passé d’un fonctionnement artisanal à une entreprise de production industrielle de haute technologie.
Le groupe comprend deux divisions. La Division de verre est plus particulièrement spécialisée dans la production contenants en verre à usage pharmaceutique. Elle propose une large gamme tels que les ampoules et flacons, ainsi que des produits en pleine croissance tels que les cartouches pour les auto-injecteurs et les stylos d’insuline, notamment les seringues stériles prêt-à-remplir.
La Division de l'ingénierie, composée des sociétés SPAMI et Optrel, se concentre sur la conception et la production de machines et équipements pour la transformation, l'inspection visuelle et le contrôle des tube en verre. La synergie entre les deux divisions fait en sorte que le Groupe Stevanato a le plein contrôle de ses processus de production, de l'achat des matières premières jusqu'au service après-vente.
"La Production de SPAMI est destinée tant aux entreprises du groupe et qu’à des sociétés extérieures." Les solutions mécaniques et électriques installées sur les machines de formage ont été conçues pour fournir la plus grande précision et les meilleurs résultats dans la production de contenants en verre.
Tous les éléments utilisés pour former le verre en fusion sont installés et soigneusement vérifiés afin de garantir les tolérances dimensionnelles des flacons, des seringues, des cartouches et des ampoules. De même, ceux utilisés dans les machines de formage, ainsi que les bandes transporteuses, sont conçus pour éviter de contaminer les contenants. Le processus est entièrement automatique, depuis le chargement du tube jusqu’à l’emballage du produit fini.
Le cycle de production commence avec des tubes de verre d’une longueur d’environ 1,5 m et de diamètre adapté à la taille du produit fini. Ceux-ci sont achetés en dehors de la société. Les tubes de verre sont introduits dans des machines rotatives de formage avec plusieurs têtes de traitement et chauffées par des brûleurs. Les flacons, les ampoules, seringue, etc. sont formés de cette manière.
En aval de la machines de formage, les produits sont placés sur une bande transporteuse où des contrôles dimensionnels et de formes sont effectués au moyen de caméras. "Ce sont essentiellement des mesures dimensionnelles ", explique M. Gobita. "Puisque le produit est soumis à des contraintes mécaniques pendant le traitement, il y a aussi un four de recuit qui fournit un cycle de chaleur supplémentaire pour éliminer les tensions dans le verre." Puis l'étape finale consiste en des contrôles de qualité du produit fini, eux-mêmes suivis par un emballage automatisé. Il convient de noter que cette dernière partie du cycle est réalisée de manière à respecter les niveaux de qualité et de stérilité requis par l’industrie pharmaceutique.
Il y a un certain nombre de concurrents sur le marché qui opèrent au niveau international. «Nos principaux concurrents sont allemands et américains, alors que les autres entreprises en Italie sont beaucoup plus petites ", explique M. Gobita.
La valeur ajoutée offerte par S.P.A.M.I. se trouve principalement dans la qualité de ses produits, qui lui a permis d'exceller dans ce secteur. "Comme ils sont utilisés dans des applications pharmaceutiques, nos produits répondent à des normes de qualité très élevées afin de se conformer aux très strictes limites réglementaires. Cela nécessite une grande quantité de personnel très qualifié pour les processus de contrôle, poursuit M. Gobita. "La différence entre nous et nos concurrents nationaux se situe sans doute là. Notre capacité de recherche et développement est également un point fort : lorsque les compagnies pharmaceutiques nous demandent des produits très spécifiques, nous pouvons offrir une solution, car nous avons la capacité de modifier nos systèmes. Cette capacité de personnalisation est une valeur ajoutée importante. Certes, il y a un certain nombre de produits standards dans le secteur pharmaceutique, tels que les ampoules ou les fioles que nous connaissons tous, mais il y a aussi de plus en plus de produits spéciaux. Ils sont développés pour la plupart ad hoc. Dans ces cas, une machine spécifique est nécessaire, qui le plus souvent, est une adaptation d’une machine existante».
Une collaboration positive avec HMS
L'association avec HMS a vu le jour afin de résoudre un problème de communication spécifique, lorsque SPAMI a souhaité introduire des contrôles de qualité des produits à base de système de vision. Plus précisément, les caméras intelligentes Cognex ont dû être connectées aux automates Siemens. "Nous avions la nécessité de permettre à des caméras pourvues d’interface Ethernet de communiquer avec des automates munis du protocole Profibus", explique M. Gobita. "Après quelques recherches approfondies, c’est avec EFA Automation, distributeur exclusif en Italie des passerelles HMS, que nous avons adopté la gamme Anybus."
A l'époque, d'autres fournisseurs potentiels ont été considérés, mais HMS a été la seule entreprise qui pourrait offrir une vaste gamme de convertisseurs de protocole. "Cette caractéristique a été la raison principale de notre choix, parce que nos applications sont souvent très différentes les unes des autres. Initialement, par exemple,
nous en avions besoin pour gérer le protocole Profibus associés aux automates Siemens. Nous avons utilisé l’Anybus X-gateway, qui convertit de Profibus pour Modbus sur Ethernet. Mais notre entreprise utilise normalement aussi des automates d'autres fournisseurs.
Sur une ligne de production, plusieurs convertisseurs Anybus sont en principe installés. «Les caméras intelligentes sont utilisées à plusieurs endroits de la ligne de fabrication. Nous avons déjà utilisé d’autres références de convertisseurs en fonction des applications que nous installions. Ils sont devenus la norme pour nous. Nous sommes très satisfaits de notre choix. Ils sont très robustes, fonctionnels et simples à utiliser par rapport à d'autres solutions similaires que nous avons essayées. Nous savons tous que même s’il est très facile de trouver des choses complexes, il n'est pas si facile de trouver des choses simples. Dans le futur, nous envisageons d'utiliser les convertisseurs HMS Anybus également sur d'autres lignes, où ils seront bien-sûr étroitement liés à nos systèmes de vision. Puisque les normes exigent des tolérances de plus en plus sévères, il est inévitable que l’utilisation de systèmes de vision va augmenter ", conclut M. Gobita.
Le groupe comprend deux divisions. La Division de verre est plus particulièrement spécialisée dans la production contenants en verre à usage pharmaceutique. Elle propose une large gamme tels que les ampoules et flacons, ainsi que des produits en pleine croissance tels que les cartouches pour les auto-injecteurs et les stylos d’insuline, notamment les seringues stériles prêt-à-remplir.
La Division de l'ingénierie, composée des sociétés SPAMI et Optrel, se concentre sur la conception et la production de machines et équipements pour la transformation, l'inspection visuelle et le contrôle des tube en verre. La synergie entre les deux divisions fait en sorte que le Groupe Stevanato a le plein contrôle de ses processus de production, de l'achat des matières premières jusqu'au service après-vente.
"La Production de SPAMI est destinée tant aux entreprises du groupe et qu’à des sociétés extérieures." Les solutions mécaniques et électriques installées sur les machines de formage ont été conçues pour fournir la plus grande précision et les meilleurs résultats dans la production de contenants en verre.
Tous les éléments utilisés pour former le verre en fusion sont installés et soigneusement vérifiés afin de garantir les tolérances dimensionnelles des flacons, des seringues, des cartouches et des ampoules. De même, ceux utilisés dans les machines de formage, ainsi que les bandes transporteuses, sont conçus pour éviter de contaminer les contenants. Le processus est entièrement automatique, depuis le chargement du tube jusqu’à l’emballage du produit fini.
Le cycle de production commence avec des tubes de verre d’une longueur d’environ 1,5 m et de diamètre adapté à la taille du produit fini. Ceux-ci sont achetés en dehors de la société. Les tubes de verre sont introduits dans des machines rotatives de formage avec plusieurs têtes de traitement et chauffées par des brûleurs. Les flacons, les ampoules, seringue, etc. sont formés de cette manière.
En aval de la machines de formage, les produits sont placés sur une bande transporteuse où des contrôles dimensionnels et de formes sont effectués au moyen de caméras. "Ce sont essentiellement des mesures dimensionnelles ", explique M. Gobita. "Puisque le produit est soumis à des contraintes mécaniques pendant le traitement, il y a aussi un four de recuit qui fournit un cycle de chaleur supplémentaire pour éliminer les tensions dans le verre." Puis l'étape finale consiste en des contrôles de qualité du produit fini, eux-mêmes suivis par un emballage automatisé. Il convient de noter que cette dernière partie du cycle est réalisée de manière à respecter les niveaux de qualité et de stérilité requis par l’industrie pharmaceutique.
Il y a un certain nombre de concurrents sur le marché qui opèrent au niveau international. «Nos principaux concurrents sont allemands et américains, alors que les autres entreprises en Italie sont beaucoup plus petites ", explique M. Gobita.
La valeur ajoutée offerte par S.P.A.M.I. se trouve principalement dans la qualité de ses produits, qui lui a permis d'exceller dans ce secteur. "Comme ils sont utilisés dans des applications pharmaceutiques, nos produits répondent à des normes de qualité très élevées afin de se conformer aux très strictes limites réglementaires. Cela nécessite une grande quantité de personnel très qualifié pour les processus de contrôle, poursuit M. Gobita. "La différence entre nous et nos concurrents nationaux se situe sans doute là. Notre capacité de recherche et développement est également un point fort : lorsque les compagnies pharmaceutiques nous demandent des produits très spécifiques, nous pouvons offrir une solution, car nous avons la capacité de modifier nos systèmes. Cette capacité de personnalisation est une valeur ajoutée importante. Certes, il y a un certain nombre de produits standards dans le secteur pharmaceutique, tels que les ampoules ou les fioles que nous connaissons tous, mais il y a aussi de plus en plus de produits spéciaux. Ils sont développés pour la plupart ad hoc. Dans ces cas, une machine spécifique est nécessaire, qui le plus souvent, est une adaptation d’une machine existante».
Une collaboration positive avec HMS
L'association avec HMS a vu le jour afin de résoudre un problème de communication spécifique, lorsque SPAMI a souhaité introduire des contrôles de qualité des produits à base de système de vision. Plus précisément, les caméras intelligentes Cognex ont dû être connectées aux automates Siemens. "Nous avions la nécessité de permettre à des caméras pourvues d’interface Ethernet de communiquer avec des automates munis du protocole Profibus", explique M. Gobita. "Après quelques recherches approfondies, c’est avec EFA Automation, distributeur exclusif en Italie des passerelles HMS, que nous avons adopté la gamme Anybus."
A l'époque, d'autres fournisseurs potentiels ont été considérés, mais HMS a été la seule entreprise qui pourrait offrir une vaste gamme de convertisseurs de protocole. "Cette caractéristique a été la raison principale de notre choix, parce que nos applications sont souvent très différentes les unes des autres. Initialement, par exemple,
nous en avions besoin pour gérer le protocole Profibus associés aux automates Siemens. Nous avons utilisé l’Anybus X-gateway, qui convertit de Profibus pour Modbus sur Ethernet. Mais notre entreprise utilise normalement aussi des automates d'autres fournisseurs.
Sur une ligne de production, plusieurs convertisseurs Anybus sont en principe installés. «Les caméras intelligentes sont utilisées à plusieurs endroits de la ligne de fabrication. Nous avons déjà utilisé d’autres références de convertisseurs en fonction des applications que nous installions. Ils sont devenus la norme pour nous. Nous sommes très satisfaits de notre choix. Ils sont très robustes, fonctionnels et simples à utiliser par rapport à d'autres solutions similaires que nous avons essayées. Nous savons tous que même s’il est très facile de trouver des choses complexes, il n'est pas si facile de trouver des choses simples. Dans le futur, nous envisageons d'utiliser les convertisseurs HMS Anybus également sur d'autres lignes, où ils seront bien-sûr étroitement liés à nos systèmes de vision. Puisque les normes exigent des tolérances de plus en plus sévères, il est inévitable que l’utilisation de systèmes de vision va augmenter ", conclut M. Gobita.