Laserline
Un partenariat de poids
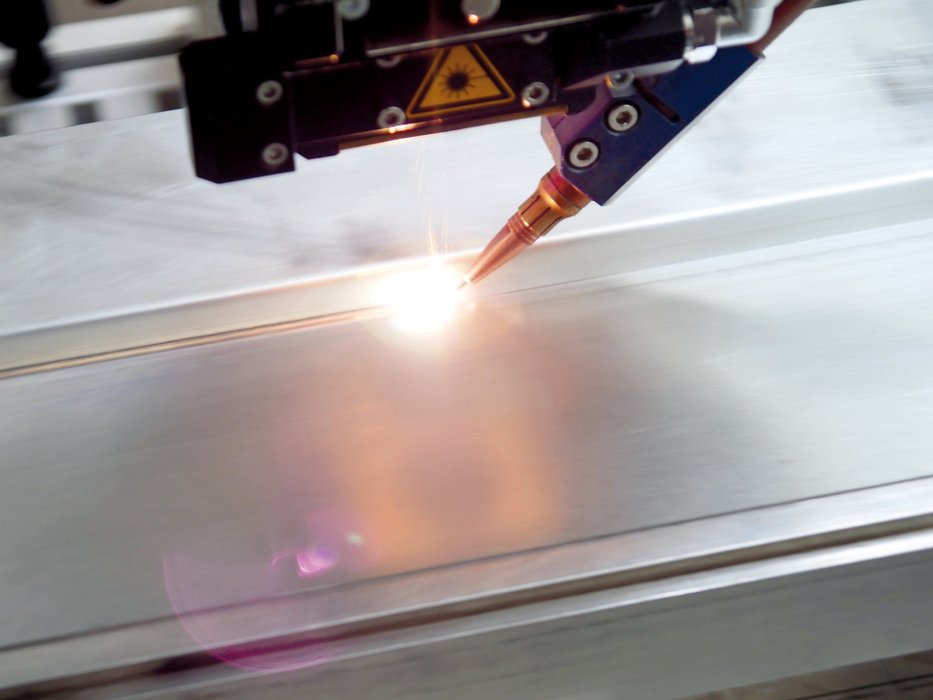
Les faisceaux laser peuvent faire fondre voire vaporiser les métaux de manière très efficace et très précise. C'est pourquoi ils sont de plus en plus utilisés comme outils d'assemblage de composants, notamment pour le soudage et le brasage dans l'industrie automobile, par exemple. Normalement, les appareils laser, tout comme que les chalumeaux traditionnels, n'ont qu'un seul point focal ou « spot ». Laserline propose désormais des optiques multi-spots pour le brasage et le soudage au laser qui permettent également de traiter des matériaux particulièrement difficiles. Les moteurs de FAULHABER contribuent à une répartition correcte de l'énergie ponctuelle.
Le zinc protège l'acier de la rouille. C'est pourquoi les constructeurs automobiles utilisent principalement des tôles zinguées pour la carrosserie de leurs véhicules. Auparavant, le revêtement métallique de protection était appliqué par galvanoplastie. Toutefois, la galvanisation à chaud s'impose peu à peu. Ce procédé offre une meilleure protection contre la corrosion. Un problème inattendu s'est posé au tout début de l'utilisation de tôles galvanisées à chaud.
Brasage ou soudage ?
Par rapport au soudage, le brasage offre une multitude d'avantages à la production en série dans l'industrie automobile. Dans le cas du soudage, les tôles sont chauffées à la température de fusion le long de la soudure elle-même, puis les deux tôles sont directement liées entre elles. Cette opération exige une précision millimétrée et il est impossible d'obtenir une qualité de soudure visible. Les soudures sont rugueuses et la vaporisation de zinc les rend poreuses. Dans le cas du brasage en revanche, une jointure faite d'un matériau différent est insérée comme matériau de remplissage entre les tôles. Cette soudure cuivre-silicium, qui se liquéfie pendant le brasage avant de se solidifier à nouveau, permet non seulement d'assembler les pièces, mais aussi de combler l'espace entre elles. Par conséquent, le brasage permet une tolérance dimensionnelle supérieure et nécessite moins d'efforts pour l'assemblage des pièces. Le brasage permet surtout de réaliser des joints sans jeu de qualité visible. Les composants soudés peuvent ensuite être peints sans avoir à subir d'autres traitements préalables.
Toutefois, dans le cas des tôles galvanisées à chaud, la soudure présente des caractéristiques différentes. « Les éclaboussures de soudure liquide étaient plus nombreuses sur les surfaces jouxtant la soudure. Les micro-éclaboussures en particulier sont difficiles à voir au début, mais deviennent ensuite clairement visibles une fois la peinture appliquée, rapporte Axel Luft, Directeur des ventes pour le secteur automobile chez Laserline. Nous avons également constaté une dégradation de la qualité de la soudure en elle-même. Elle était plus rugueuse et formait souvent ce qu'on appelle des vaguelettes, c'est-à-dire des points auxquels la soudure franchit la limite de soudure prévue. »
Solution de brasage pour les tôles galvanisées à chaud
Il était évident que ces problèmes étaient liés à la couche de zinc sur la tôle d'acier. La galvanisation à chaud rendait cette couche plus épaisse et moins régulière. De plus, elle présentait un comportement de réflexion différent, affectant également le processus de brasage. Thorge Hammer, ingénieur au service de planification et de développement technologique chez Volkswagen à Wolfsburg, est responsable de ce processus de brasage et a eu une idée pour résoudre ce problème : retirer le zinc des bords de la soudure avant le brasage. Toutefois, cela nécessiterait que le spot laser circulaire habituel soit rectangulaire et qu'il existe également une ouverture à travers laquelle alimenter la soudure. Les coins « avant » du spot seraient alors chargés d'enlever le zinc, tandis que la plus grande partie du rectangle procèderait à la soudure proprement dite.
« Cette solution était impossible d'un point de vue technique, mais nous étions sur la bonne voie, se souvient Markus Baumann, ingénieur en chef du développement chez Laserline. Au lieu de former un spot de forme complexe – et donc très difficile à obtenir d'un point de vue optique, nous avons finalement ajouté deux spots plus petits au spot principal. Lors du soudage, ces spots secondaires sont toujours dirigés vers les bords de la soudure devant le spot principal, qui mesure quelques millimètres carrés. » Leur énergie est suffisante pour vaporiser la couche de zinc dans cette zone, commencer à faire fondre l'acier et générer une légère oxydation. Cette opération produit une couche dite « passive » qui empêche le bouillonnement de la brasure liquéfiée par le spot principal.
Il n'est donc pas nécessaire d'enlever les éclaboussures de soudure au niveau des pièces soudées avant la peinture. Autre raison justifiant l'utilité d'un spot principal rectangulaire : il répartit la chaleur sur la soudure de façon plus uniforme qu'un spot circulaire, créant ainsi un bain de soudure sans fioritures. « Grâce à cette technologie, nous avons enfin pu résoudre tous les problèmes rencontrés avec les tôles galvanisées à chaud, se réjouit M. Luft. Elle est désormais utilisée dans la production en série chez VW et nous permet d'atteindre une vitesse de brasage allant jusqu'à 4,5 mètres par minute. D'autres fabricants suivront bientôt le mouvement. »
Séparation de faisceau avec module optique
Un module optique est chargé d'assurer l'alignement précis des spots. Il contient divers éléments optiques qui modifient le faisceau laser de façon sélective. La lentille de collimation aligne les faisceaux laser divergents qui sortent du câble à fibres optiques, de façon à ce que les parcours de tous les faisceaux soient parallèles les uns aux autres. Une matrice d'homogénéisation génère un spot principal de forme carrée, tandis que d'autres éléments optiques divisent le faisceau pour générer d'autres spots. Dans le cas du brasage, deux spots de tête sont générés à l'avant et sur le côté du spot principal. Afin de garantir une soudure propre à la fin du processus, la répartition de la puissance entre le spot principal et les spots de tête ainsi qu'entre les spots de tête entre eux doit être réglée avec précision. La répartition de la puissance du laser sur ces spots dépend de la position des éléments optiques. Le déplacement de ces éléments sur les axes X et Y permet d'obtenir une répartition précise de la puissance laser comme requis pour la tâche concernée.
Pour de l'aluminium soudé en profondeur, par exemple, un petit spot intense peut être positionné à l'intérieur du spot principal, plus léger. Pour souder ensemble des tôles d'épaisseurs différentes, deux spots peuvent être adaptés à chaque matériau. Cette opération peut être effectuée pendant le processus car les éléments du module optique Laserline sont déplacés par des moteurs.
Le bord de ce module de forme carrée mesure 12 centimètres de longueur et 5 centimètres de profondeur. Ce petit espace renferme les éléments optiques et un système mécanique complexe, laissant peu de place aux moteurs. Les systèmes d'entraînement doivent donc être aussi compacts que possible.
« Nous avons opté pour des servomoteurs C.C. sans balais de la série 1226 B FAULHABER, ils mesurent 12 millimètres de diamètre, sont dotés de vis-mère directement fixées à l'arbre du moteur et sont sans accouplement d'arbre, explique M. Baumann. Nous disposons ainsi d'un entraînement très compact qui fournit néanmoins de manière fiable la puissance et la vitesse requises. La simplicité d'intégration du contrôleur de mouvement dans le système était un autre point important à prendre en compte. » Le contrôleur de mouvement de FAULHABER est logé à l'extérieur du module est communique grâce à une interface série RS232. Si le client de Laserline le souhaite, la combinaison moteur/contrôleur peut également être actionnée via un système de bus CAN, sans devoir apporter de changements à la mécanique ou au boîtier. Il est possible de remplacer facilement le contrôleur RS 232 par une version à interface CANopen.
Moteur avec garantie de position
Le système optique laser est monté sur un bras de robot pendant le brasage et le soudage. Ce bras positionne le système comme souhaité. Le système optique doit supporter des charges dynamiques considérables qui agissent sur les moteurs et peuvent générer des changements de position involontaires. « Le moteur FAULHABER n'a pas ce problème. En effet, il détecte sa position actuelle à l'aide du capteur à effet Hall intégré et s'ajuste le cas échéant, au plus tard lorsque le laser est positionné sur la soudure, souligne M. Luft. Nous sommes ainsi assurés que tout positionnement incorrect est exclu. La qualité élevée des entraînements nous permet d'obtenir des résultats constamment reproductibles, un critère fondamental puisque nos clients comptent sur un fonctionnement sans problème pendant au moins sept ans ! »
M. Baumann ne doutait pas de trouver le moteur approprié chez FAULHABER. Cela avait déjà été le cas huit ans auparavant, alors qu'il recherchait un moteur adapté à un nouveau système de zoom optique. À l'époque, les moteurs pas à pas constituaient la norme pour ce type d'appareil. Toutefois, comme le rapporte l'ingénieur de développement, ces moteurs pas à pas éprouvaient des difficultés à gérer l'accélération des masses dans le bras du robot : « Du fait de la charge dynamique, certains pas individuels peuvent échapper à un moteur pas à pas. Pour éviter cela, un codeur peut être utilisé afin de déterminer et de réajuster la position. Cette combinaison est aussi complexe que coûteuse. Quand j'étais jeune, j'ai eu besoin d'un moteur compact pour une maquette de bateau et je l'ai trouvé chez FAULHABER. Je m'en suis souvenu lors du développement du système de zoom optique. J'ai donc contacté FAULHABER et, une fois de plus, j'ai trouvé le moteur idéal. Cela nous a permis de créer une solution extrêmement rentable qui s'est avérée très efficace. » Le nouveau module multi-spot fait également preuve d'une exécution sans faille dans la production en série. De plus, ce système optique est déjà largement reconnu par les experts : la solution technique et l'efficacité économique obtenue en peu de temps dans les applications industrielles ont convaincu le jury international chargé de décerner le prix « Innovation Award Laser Technology ». Cette année, l'équipe de développement a remporté le premier prix.