Heidenhain se forge un succès
La société App Tech produit 60 000 jantes haut de gamme par an dans son atelier de Mestrino, une commune de Vénétie située entre Vicence et Padoue, dans le nord de l'Italie. La commande numérique TNC 640 est pour beaucoup dans le succès de l’entreprise. Tout en contribuant largement au respect précis de la trajectoire de l'outil, elle montre clairement l'influence qu'elle a sur un bon processus de fabrication.
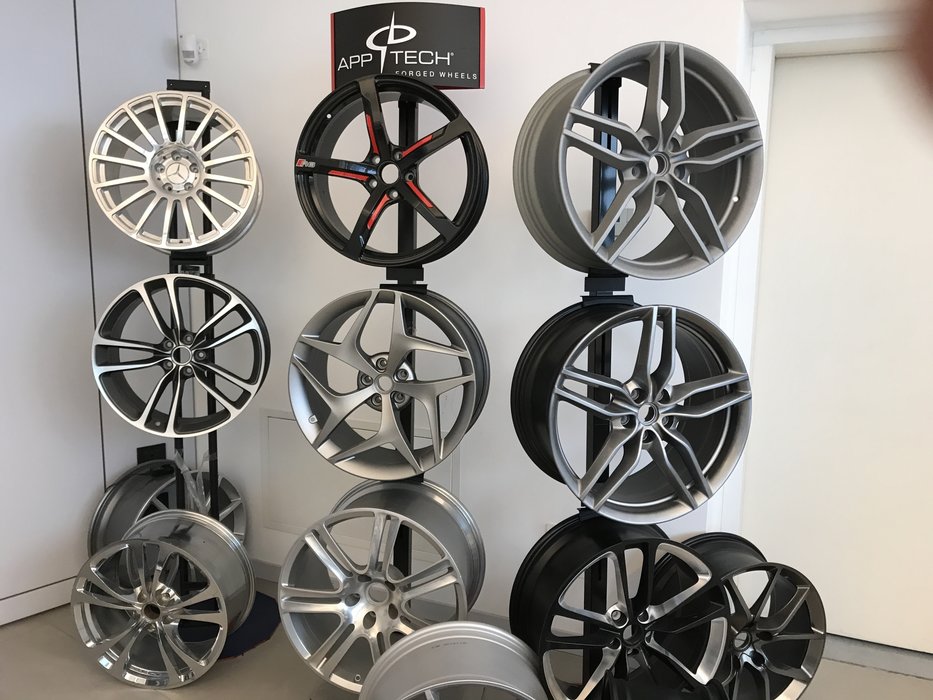
Photo : Pour un état de surface parfait l'usinage de finition de ces jantes haut de gamme est réalisé sur de puissants centres 5 axes équipés de commande de contournage TNC 640 capable de garantir un asservissement hautement précis des trajectoires.
En améliorant à la fois la dynamique et les caractéristiques de conduite d’une automobile, de bonnes jantes en aluminium contribuent à améliorer les performances. En plus leur design doit être étudié pour donner une impression de vitesse ou de puissance même sur un véhicule à l’arrêt. Par contre, toutes les jantes ne se valent pas, même si elles peuvent parfois se ressembler. Le nec plus ultra, ce sont les jantes forgées en aluminium et en magnésium, comme celles que la société App Tech fabrique pour de grandes marques de voitures, pour le tuning ou la course automobile. C’est une technique d’excellence coûteuse mais haut de gamme. Le dynamisme est alors garanti par le faible poids et une bien meilleure rigidité structurelle du matériau forgé par rapport au plus conventionnel matériau moulé. Cet avantage provient notamment de l'absence de porosité, de la bonne étanchéité de la matière, mais aussi de la répartition granulométrique homogène dans la matrice de la pièce forgée, ce qui permet de fabriquer des jantes plus légères aux propriétés de stabilité et de conduite exceptionnelles. Pour l'aspect visuel en revanche, c'est l'usinage qui joue un rôle déterminant. Chez App Tech, c’est la TNC 640 d’Heidenhain qui a été retenue pour garantir un usinage des plus efficients.
Un état de surface parfait obtenu plus rapidement
Le processus de forgeage crée les conditions favorables au très bon état de surface qui sera obtenu à l'issue de l'usinage. C’est toutefois possible seulement avec une machine puissante et une commande capable de garantir un asservissement hautement précis des trajectoires. Pour l'usinage de finition, App Tech utilise des centres d'usinage 5 axes équipés d'une commande de contournage TNC 640 Heidenhain. Francesco Doro, responsable du département mécanique et automatisation d’App Tech, nous donne un aperçu du processus de fabrication. Les blocs d'aluminium et de magnésium traités à chaud sont d'abord préparés sur des tours à 3 axes, avant de subir un usinage de finition sur des machines à 5 axes. “L'usinage en 5 axes continus est effectué avec le flanc de l'outil conique. Cette technique nous permet d'obtenir un meilleur état de surface en moins de temps qu'il n'en faudrait avec la pointe d'un outil sphérique. La TNC 640 de Heidenhain joue alors un rôle important dans le respect de la trajectoire de l'outil. La moindre erreur de positionnement de l'outil serait en effet susceptible d'endommager la surface.” C'est d'ailleurs pour cette raison que les usinages sont principalement effectués avec le cycle 32 Tolerance. Ce dernier optimise l'asservissement du mouvement et l'adapte à l'usinage pour atteindre le niveau de précision recherché, sans que cela se fasse au détriment de la dynamique. Ce n'est toutefois pas le seul atout de la TNC 640. Pour les opérations d'usinage à 3, puis à 5 axes, il est en effet essentiel que le point d'origine soit défini avec une extrême précision pour la finition de la pièce à usiner: “Pour éviter les erreurs de positions sur la pièce, il faut que le système de coordonnées 3D soit orienté par rapport à la surface de la jante, et non par rapport à la surface de la machine. Nous y parvenons avec un palpeur de pièces Heidenhain associé au cycle Tch Probe 431 de la TNC 640,” détaille Francesco Doro.
La TNC640 aide à la quête de perfection
Pour une jante usinée et intégralement polie, avec le même système de FAO, le même programme et les mêmes paramètres d'usinage, la TNC 640 a permis de réduire le taux de rebut dû à un manque esthétique de 30 à 2 %.Dans le même temps, la machine travaille 10 % plus vite. App Tech réorganise sa production pour optimiser le flux de projets. La TNC 640 joue un rôle très important dans cette initiative. Compte tenu des bons résultats atteints avec les commandes Heidenhain en termes de performances de production, le spécialiste prévoit d'acquérir sept nouvelles commandes TNC. Pour de potentielles améliorations, l’entreprise s'est aussi lancée dans la production numérique. Dans le cadre d'un projet pilote en partenariat avec Heidenhain, le fabricant teste le nouveau logiciel StateMonitor, qui fait partie de la solution « Connected Machining ». En se basant sur l'acquisition et l'analyse des états des machines au sein d'une production connectée en réseau, elle va pouvoir s’appuyer sur des données solides qui l’aideront à réaliser encore des améliorations.