www.industrie-afrique-du-nord.com
03
'18
Written on Modified on
L'analyse globale de la détérioration des outils ne se limite pas à l'usinage
Les outils coupants sont des éléments primordiaux du processus d'usinage des métaux. Selon la manière dont les outils sont fabriqués et utilisés, ils permettent de maximiser la productivité de l'usinage ou deviennent au contraire des obstacles à la production. Cela dépend beaucoup de la façon dont l'utilisation de l'outil est gérée par rapport à l'ensemble du processus de production.
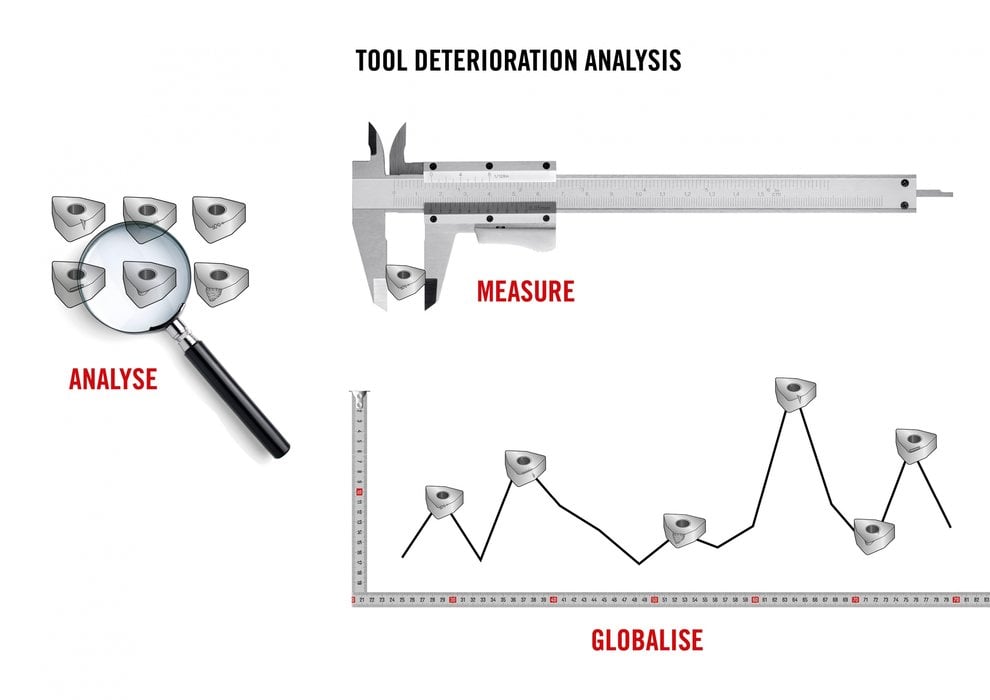
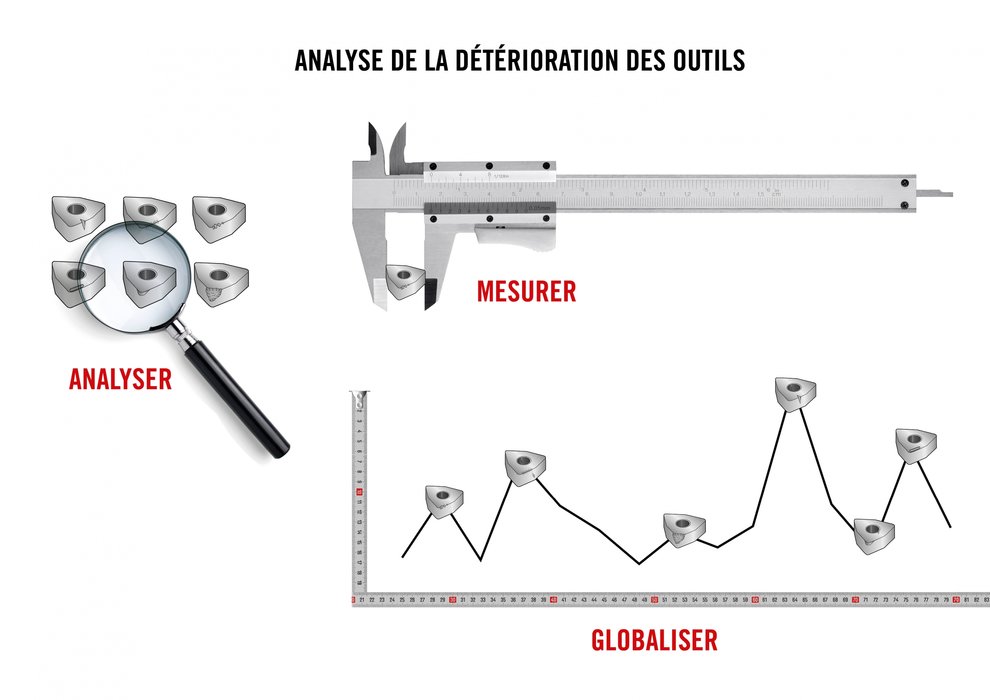
Figure 1
Les outils coupants sont de par leur nature des consommables ; ils s'usent jusqu'à ne plus être efficaces. Une approche traditionnelle de la gestion des outils se concentre uniquement sur l'analyse de l'usure, qui porte essentiellement sur la matière, la géométrie et les paramètres de coupe pour améliorer une partie de la production et aussi la durée de vie de l'outil dans le cadre d'une opération spécifique. Pour maximiser l'efficacité de l'ensemble du processus de fabrication d'un site, il faut toutefois tenir compte de plusieurs autres facteurs que l'usure de l'outil. Il est ainsi essentiel d'examiner de façon plus générale, l’usure des outils, à la lumière du contexte général ou global du processus de production.
L'analyse globale de la détérioration des outils (GTDA) ne se limite pas uniquement au contrôle de base de l'usure des outils. En effet, elle prend en considération des facteurs tels que le temps consacré à la manipulation des outils, les problèmes non liés à l'usure, l'économie de production, l'organisation de l'atelier, les comportements et les croyances des équipes, la gestion des chaînes de valeur et les coûts totaux de production. L'analyse GTDA est basée sur l'évaluation régulière d'un grand nombre d'outils coupants utilisés dans les ateliers. Ils sont choisis au hasard pour dresser un panorama complet de leur contribution déployée sur l'ensemble du site de production.
Processus de production global
L'examen de l'usure des outils est généralement limité à un seul outil dans le cadre d'un usinage spécifique. Cependant, pour en tirer le maximum de rentabilité, il est essentiel d'examiner l'usure ou la détérioration des outils en prenant en compte tous les outils utilisés dans les procédés de fabrication d'une usine. Le processus de fabrication (Figure 2) commence par l'acquisition des matières brutes et la planification avec l'utilisation des compétences humaines, des ressources technologiques et des investissements. Le processus avance à travers la création de valeur ajoutée mais peut être freiné par des événements générateurs de déchets qui entraînent une perte d'argent, de temps et de ressources intellectuelles et réduisent ainsi la qualité et le rendement. Le rendement est mesuré en fonction de la qualité de la pièce, de la quantité requise, du temps de production souhaité et du coût.
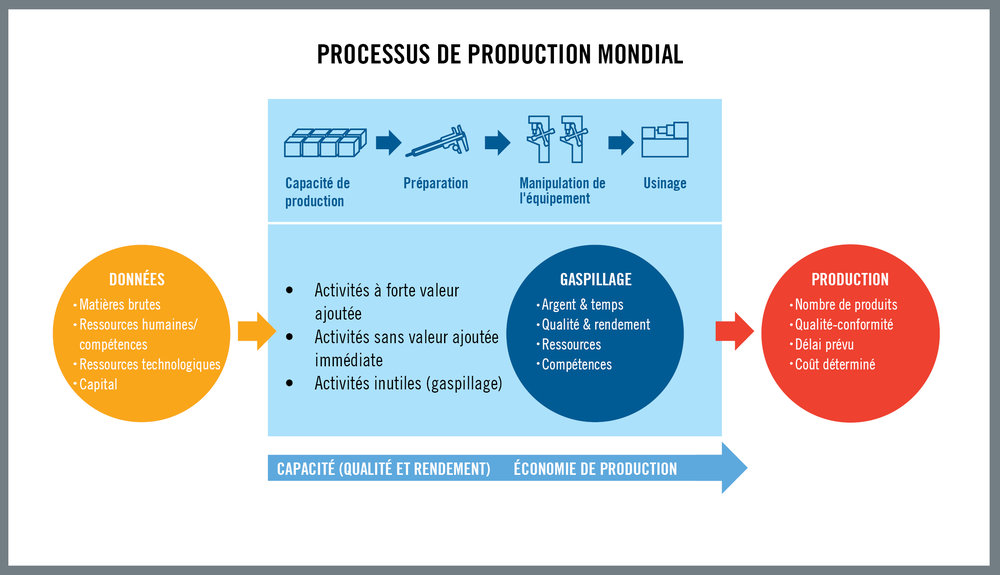
HQ_ILL_Processus_Global_de Production.jpg
Figure 2
Évolution du processus de production
Les méthodes utilisées pour analyser et prévoir la durée de vie de l'outil dépendent de la façon dont les outils sont utilisés. Au fil des siècles, les méthodes de fabrication sont passées de la production artisanale de pièces "uniques" à la production de masse de pièces standardisées. L'amélioration des méthodes de fabrication a ensuite débouché sur une deuxième génération de production de masse permettant de produire des volumes de plus en plus importants de pièces similaires (modèle de production de masse à faible variabilité (HVLM)). Plus récemment, la technologie numérique appliquée à la programmation, aux commandes des machines-outils et aux systèmes de manipulation des pièces a facilité la pratique d'une troisième génération de production qui permet une production de masse (HMLV) à forte variabilité et faible volume rentable.
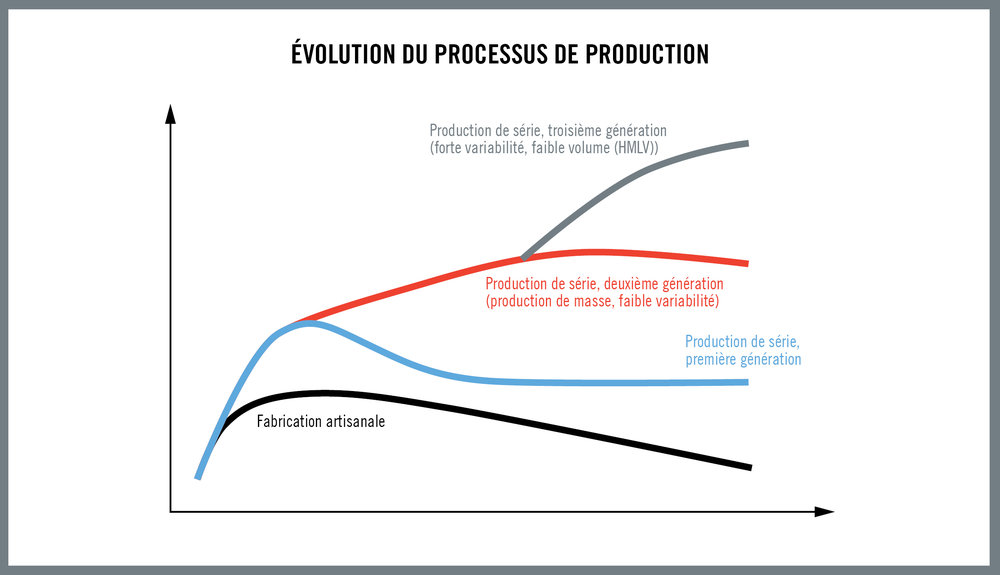
HQ_ILL_Evolution_du Processus_de production.jpg
Figure 3
Bien que les principales problématiques en matière de rendement demeurent inchangées (à savoir la réalisation d'économies de temps, d'argent et un certain niveau de rendement), les techniques de production de masse de deuxième et troisième générations nécessitent des approches différentes en matière d'analyse de la durée de vie de l'outil. Dans un contexte de production de masse à faible variabilité (HVLM) de deuxième génération, des pièces identiques sont usinées à partir de la même matière à usiner dans des cycles de production qui peuvent durer des jours, des mois ou des années avec le même équipement et le même type d'outils coupants. Dans ce cas, la gestion de la durée de vie de l'outil est relativement simple. Le personnel de l'atelier fait appel au processus de prototypage et réalise des essais pour déterminer la meilleure moyenne de durée de vie de l'outil (exprimée en nombre de pièces/arête par exemple), puis divise le volume de pièces souhaité par la durée de vie prévue des outils sélectionnés lors des essais.
Des données cohérentes sur la durée de vie de l'outil permettent à un atelier de planifier le remplacement des outils pour optimiser leur utilisation et soutenir une production continue. Cependant, les méthodes de production de masse à faible variabilité sont en déclin. Afin d'équilibrer les stocks de pièces avec la demande et de s'adapter aux changements technologiques en cours, les fabricants usinent de moins en moins de pièces dans le cadre de séries de production longues et identiques.
Dans le même temps, les stratégies de production de masse (forte variabilité, faible volume, HMLV) de troisième génération se répandent de plus en plus. Les processus HMLV rapidement ajustables correspondent bien aux objectifs actuels en matière de stock et d'ingénierie, mais le processus de planification est beaucoup plus complexe. Une série de dix pièces peut être suivie de lots de deux ou cinq pièces, voire d’un seul composant. Les matières à usiner peuvent varier de l’acier à l’aluminium en passant par le titane, et la géométrie des pièces peut être simple ou complexe. Le temps est compté et souvent insuffisant pour déterminer la durée de vie de l’outil en réalisant des essais.
Dans de tels cas, un atelier fait généralement une estimation prudente de la durée de vie prévue d'un outil et, pour être sûr, utilise un nouvel outil pour chaque série, puis le met au rebut bien avant qu'il n'atteigne la fin de son cycle de productivité réel. Une approche plus globale de l'analyse de l'usure de l'outil et des prévisions s'y afférent peut contribuer à réduire les rejets de déchets ainsi générés.
Possibilités de rendement binaire
L'évolution rapide des méthodes de fabrication HMLV (production de masse à forte variabilité et faible volume) augmente la difficulté d'atteindre un pourcentage élevé de rendement des opérations d'usinage. Dans le cas d'une production HVLM à long terme, des essais et des réglages peuvent permettre d'atteindre plus de 90 % de rendement. De plus, le rendement peut être binaire dans le cadre d'une production HMLV. Une seule pièce réussie représente un rendement de 100 %, mais lorsque la pièce n'est pas utilisable ou qu'une pièce à usiner est détruite, le rendement est nul.
Les exigences en matière de qualité, de coût et d'efficacité demeurent inchangées. Cependant, le premier rendement est devenu une exigence primordiale. Dans ce cas, éviter la rupture de l'outil est peut-être la préoccupation qui relève de la plus grande importance. L'un des avantages est que l'usure de l'outil ne représente pas un problème majeur dans le cadre de petites séries de production. L'atelier peut notamment appliquer, dans la limite du raisonnable, des paramètres de coupe plus élevés et productifs.
Artisanat et contribution humaine
Les séries de production HVLM longues et identiques tendent à minimiser l'importance des contributions humaines au processus de production. Après le lancement d'une longue série, les opérations peuvent être essentiellement automatisées. Même dans les cas où un opérateur participe à chaque changement de pièce, le caractère répétitif de ces situations marginalise l'apport des opérateurs et des programmeurs. Aucune flexibilité n'est requise, elle est même parfois déconseillée.
Au contraire, l'évolution rapide des méthodes HMLV redonne de l'importance au rôle de l'homme dans le processus, au point que les opérations nécessitent une forme d'artisanat traditionnel impliquant de la créativité et de la flexibilité afin de s'adapter à l'évolution des pièces et aux conditions de coupe spécifiques à l'usinage HMLV.
Mettre l'accent sur le processus plutôt que sur les résultats
De nombreuses analyses du processus de production sont axées sur l'examen des résultats obtenus par rapport à la durée de vie de l'outil et à une partie de la production et ne permettent pas d'étudier le processus lui-même de manière approfondie. Les problèmes liés aux outils coupants, mais pas directement à la durée de vie de l'outil, peuvent passer à la trappe et représenter une entrave à la production. Par exemple, les bavures ne sont généralement pas liées à la durée de vie de l'outil, mais leur présence interrompt le processus de production. Dans ce cas, il convient de développer et d'appliquer une opération différente afin d'éliminer les bavures.
L'apparition de bavures est toutefois liée à la géométrie de l'outil et aux paramètres de coupe et doit donc être prise en compte dans l'analyse de la détérioration des outils. La rupture de l'outil, autre problème qui n'est généralement pas lié à l'usure de l'outil, concerne le matériau, la géométrie, les paramètres ainsi que les facteurs propres à la machine-outil.
Éléments permettant d'atteindre une excellence opérationnelle
Les principaux composants permettant l'efficacité sont l'élimination des déchets, l'inflexibilité et la variabilité. L'analyse complète de la détérioration des outils prend en compte cinq éléments permettant une excellence opérationnelle.
Tout d'abord, il est essentiel de bien comprendre l'ensemble du processus d'usinage et de la relation entre l'opération d'usinage et la matière à usiner. Deuxièmement, il faut faire particulièrement attention à réduire les déchets, grâce à des stratégies sans gaspillage et à d'autres initiatives. Troisièmement, les notions d'économie de production doivent être appliquées pour assurer la rentabilité. Quatrièmement, le taux de rendement visé doit être examiné en tenant compte du volume de production et des différentes pièces. Le fait de maximiser la flexibilité doit être vu comme un moyen de réduire les obstacles à la production. Ce paramètre doit être contrôlé afin d'assurer des tolérances de pièces cohérentes. Enfin, il est nécessaire d'insister sur la valeur du personnel de fabrication pour tirer le meilleur parti de la ressource unique et irremplaçable que celui-ci représente.
Considérations allant au-delà de l'usure de l'outil
L'analyse globale des outils complète la mesure initiale de l'usure des arêtes de coupe avec l'analyse du rôle des outils dans le coût total des marchandises vendues (CMV), l'analyse SMED (changement rapide d'outil), les résultats de la gestion de la chaîne de valeur (VSM) et les pourcentages des taux de rendement global (TRG).
La considération économique la plus fondamentale liée à l'outillage est claire : les outils coûtent de l'argent. La figure 4 présente le coût des différents éléments du processus d'usinage et les comptabilise dans le coût total des marchandises vendues (CMV). Ces données permettent à un atelier de comparer et de mettre en contraste les différents paramètres des coûts de production, dans le but de trouver des solutions pour réduire les coûts et accroître la rentabilité opérationnelle.
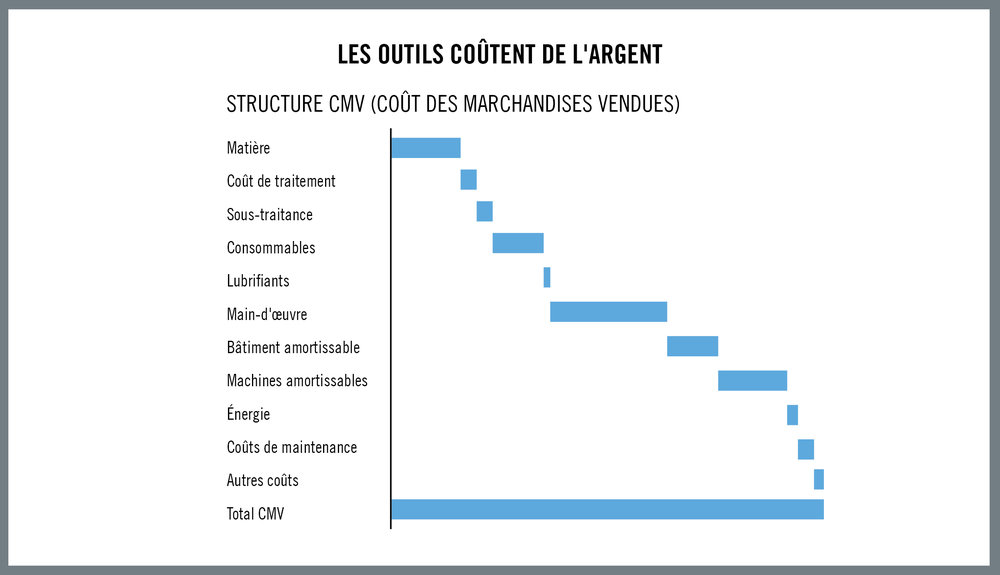
HQ_ILL_Coût_Financier_des Outils.jpg
Figure 4
Un autre facteur économique lié aux outils est que ceux-ci engendrent des frais (temps nécessaire pour manipuler les outils en dehors des opérations d'usinage proprement dites). Le temps consacré au changement et à l'installation des outils est analysé au moyen de techniques analytiques SMED (Single Minute Exchange of Die ou changement rapide d'outil) qui permettent également d'obtenir une vue d'ensemble des coûts au-delà de ceux générés par l'usure et le remplacement des outils. Une partie des dépenses est engagée pour acquérir et organiser les outils, le montage et le chargement de programmes dans la machine-outil.
Le TRG (taux de rendement global) détermine la quantité de temps de fabrication disponible utilisé de manière efficace. L'analyse du TRG montre les pertes, les progrès accomplis et permet d'améliorer la productivité tout en éliminant les déchets. Le temps total disponible pour la production est identifié, puis les temps d'arrêt planifiés ainsi que le temps perdu par les pannes imprévues, les changements, les arrêts courts, les pertes de vitesse ainsi que les mises au rebut et les ré-usinages sont déduits du total pour obtenir la durée d'usinage efficace exprimée en pourcentage du temps total disponible. Un TRG de 100 %, qui est un objectif noble mais pratiquement irréalisable, signifie qu'une pièce a été produite selon les critères de qualité spécifiés, le plus rapidement possible et sans perte de temps.
L'analyse de la gestion de la chaîne de valeur (VSM) illustre la nécessité d'équilibrer l'amélioration des performances entre tous les éléments du processus de fabrication. La figure 5 est une représentation graphique des effets de l'amélioration de la performance d'un seul élément d'un système. Imaginez plusieurs personnes dans un aviron. Si l'un des rameurs était beaucoup plus performant que les autres, cela nuirait à la performance globale de l'équipe.
Des améliorations doivent être apportées à certaines étapes du processus en raison de leur rapport au volume et à la variété de la production, aux caractéristiques de la matière à usiner, à la géométrie des pièces, aux exigences de la machine-outil et aux réglages requis, ainsi qu'à d'autres considérations, afin de réaliser et de maintenir une fabrication équilibrée dans l'ensemble.
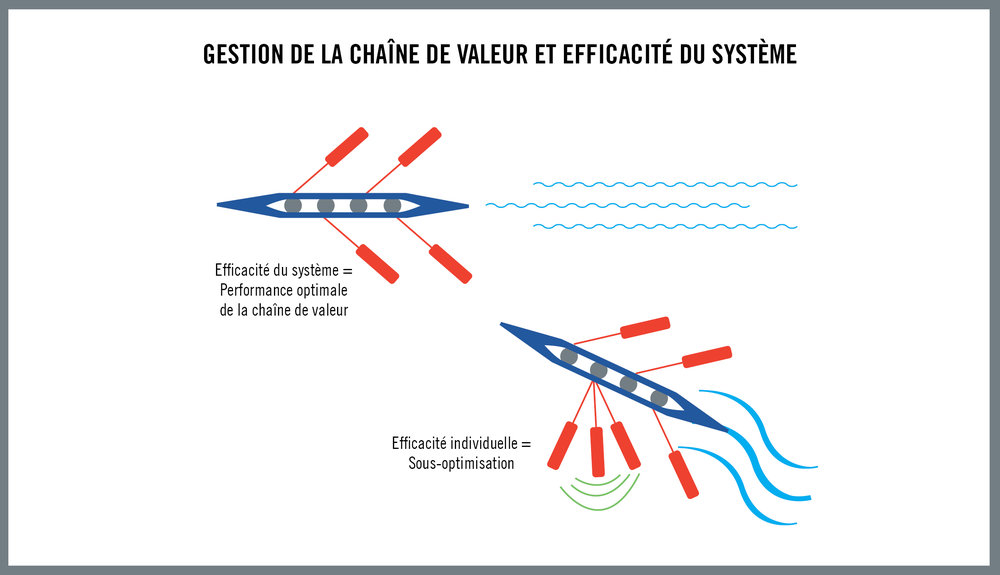
HQ_ILL_VSM_et_Système_d'efficience.jpg
Figure 5
Analyse globale de la détérioration des outils
L'analyse GTDA est fondamentalement un processus simple. Les arêtes de coupe d'un grand nombre d'outils choisis au hasard dans un atelier sont examinées une par une afin de déterminer celles qui sont usées. L'usure est classée selon son type et son importance. L'analyse traditionnelle de l'usure des outils est axée sur un outil dans le cadre d'une seule opération. L'analyse GTDA recueille des informations sur l'usure des outils et d'autres aspects liés à l'outil dans tout l'atelier, puis s'appuie sur les méthodes CMV, SMED, VSM, TRG et d'autres outils analytiques pour réunir des données supplémentaires qui permettront de guider la planification et de mettre en œuvre des programmes d'amélioration.
Pour qu'un atelier réussisse, celui-ci doit être assez discipliné pour initier un programme ayant recours à une analyse GTDA. Il est tout aussi important que celui-ci poursuive l'examen des outils et l'analyse des données de manière régulière. L'honnêteté est également un critère de discipline dont on ne peut se passer. Un atelier doit accepter de manière honnête et objective les résultats de l'analyse et être prêt à agir sur les résultats sans tenir compte des habitudes et de la politique de l'atelier ou des avis non fondés concernant les paramètres de coupe de l'outil.
Conclusion
L'usure de l'outil est inévitable et sa gestion est essentielle pour assurer le succès des opérations d'usinage. Cependant, l'usure de l'outil n'est qu'un exemple des nombreux rôles des outils coupants sur l'efficacité du processus de production d'une usine dans son ensemble. L'analyse GTDA va au-delà de l'analyse de l'usure d'outils individuellement pour inclure tous les outils d'un atelier ainsi que tous les facteurs influant liés à l'outil en dehors du processus de coupe.
Encadré :
Analyse GTDA : pourquoi et comment
À l'apogée de l'ère de la production de masse à volume élevé de pièces individuelles, l'usure de l'outil était simplement mesurée, manipulée et équilibrée pour maximiser la durée de vie de l'outil et une partie de la production. Comme ces stratégies ont évolué vers une production plus en juste-à-temps de pièces presque sur mesure, l'importance de l'usure des outils est devenue un élément de moindre importance dans le cadre du processus de production.
Seco Consulting Services analyse en permanence l'évolution continue de la production et a développé son modèle de production « NEXT STEP » pour faire face aux changements continus de l'industrie (Figure 6). Le modèle NEXT STEP est basé sur les quatre critères clés de l'usinage, à savoir la rentabilité, l'efficacité dans le temps, la qualité et le rendement. Next Step permet aux industriels d'établir et de respecter des normes d'usinage qu'ils appliqueront eux-mêmes à travers l'analyse de la production de déchets, de la technologie des procédés d'usinage, de l'outillage et de la science de la matière à usiner, de l'économie et du rendement de la production, ainsi que du rôle crucial des personnes et du leadership dans le cadre de leurs opérations.
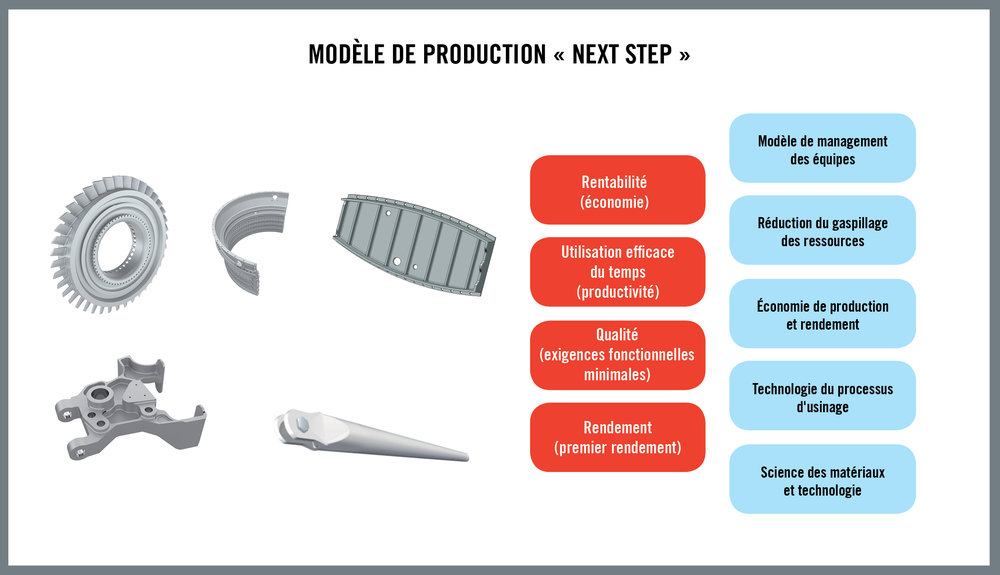
HQ_ILL_Modèle_de Production_Next_Step.jpg
Figure 6
L'analyse globale de la détérioration des outils (Figure 7) est un élément clé de l'évaluation et de l'amélioration du processus de production dans son ensemble. En examinant une sélection aléatoire d'outils couvrant toutes les opérations d'usinage d'une usine, puis en appliquant plusieurs mesures dans l'atelier, un industriel acquiert une compréhension approfondie du rôle que l'outillage joue dans l'ensemble du processus d'usinage. L'analyse GTDA permet aux ateliers de découvrir à quel niveau les performances des outils peuvent être améliorées pour augmenter la productivité, et de découvrir les situations où les problèmes liés à l'outillage peuvent représenter un obstacle au flux de production.
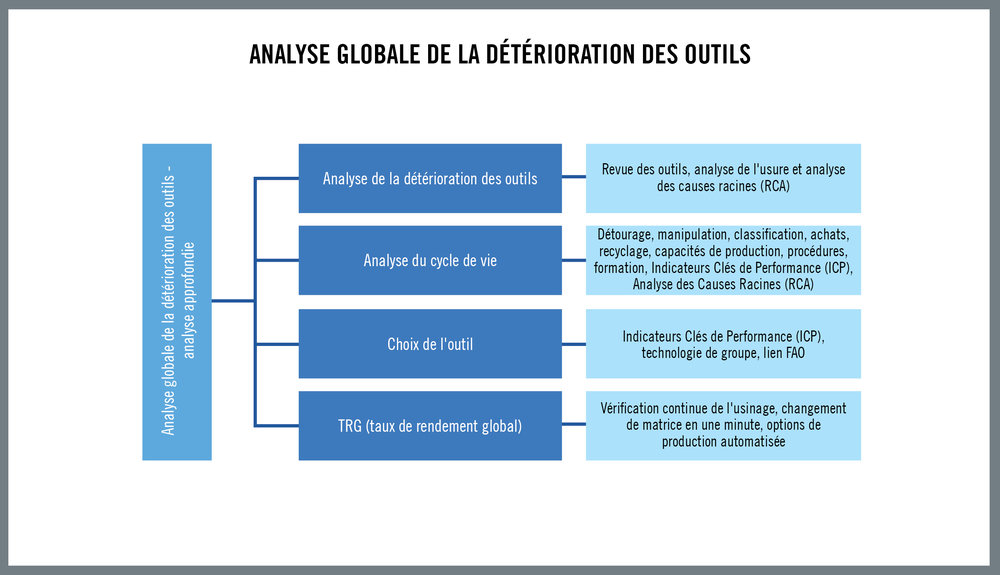
HQ_ILL_Analyse_Globale_de la détérioration_des Outils_.jpg
Figure 7
Seco Consulting Services a produit un manuel intitulé « Tool Deterioration: Best Practices » (soit en français: Les meilleures pratiques en détérioration des outils) (Figure 8) sur le thème spécifique de l'analyse GTDA. Le livre présente la détérioration des outils comme un point d'équilibre pour les modèles d'usinabilité, mettant en avant le fait que la plupart des problèmes dans les processus d'usinage peuvent être classés comme des événements liés à la détérioration des outils. Le guide porte sur les différentes applications d'usinage des métaux et vise à fournir un aperçu des phénomènes qui sont à l'origine de la détérioration des outils, tout en offrant une vue d'ensemble des « meilleures pratiques » en matière d'identification, de manipulation et de contrôle des processus de détérioration des outils.
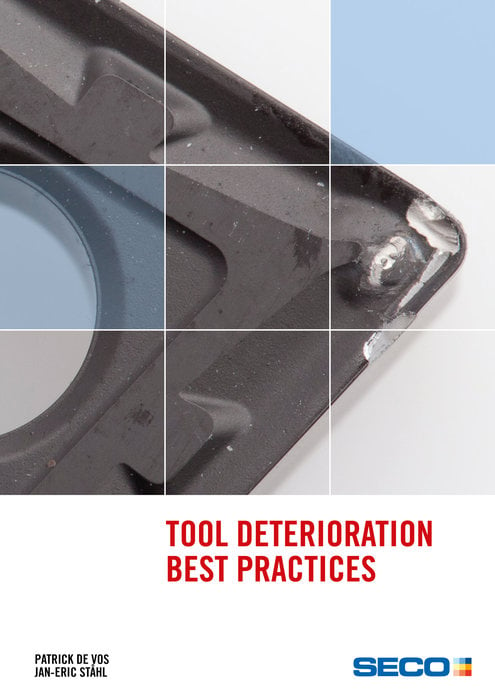
HQ_IMG_Les meilleures pratiques en_Détérioration_des_Outils_2014.jpg
Figure 8
Par :
Patrick de Vos, Responsable de l'enseignement technique en entreprise, Seco Tools