Révolution de la fabrication 4.0 avec l'Internet industriel des objets
Par : Marlon Schwank, expert en Industrie 4.0, Motion Systems Group Europe - Division Industrial Systems Europe.
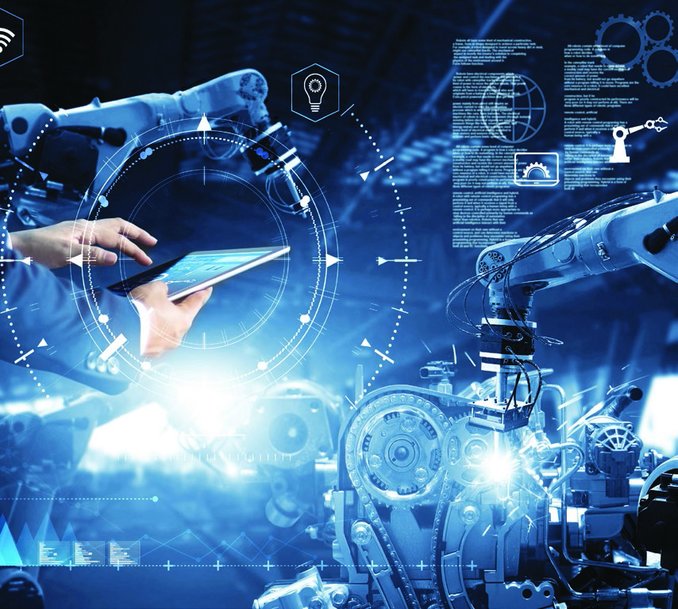
En 1712, Thomas Newcomen a inventé la première machine à vapeur pleinement fonctionnelle, conçue pour pomper l'eau des mines en activité et assurer la continuité de la production. Cette invention était peut-être le premier exemple de système de maintenance industrielle et a marqué le début de la première révolution industrielle.
Trois cent dix ans plus tard, il ne fait aucun doute que, quel que soit le secteur d'activité de votre entreprise, l'industrie manufacturière se trouve aujourd'hui au cœur d'une quatrième grande révolution industrielle.
Comme le montre l'histoire, les trois révolutions industrielles précédentes ont été caractérisées par des évolutions progressives. Tout d'abord, la production mécanique utilisant l'eau et la vapeur a évolué vers la production de masse utilisant l'énergie électrique, suivie d'une production automatisée utilisant l'électronique numérique.
La quatrième révolution s'appuie sur cette dernière évolution et progresse à un rythme exponentiel plutôt que linéaire. Elle englobe trois tendances technologiques, à savoir la connectivité, l'intelligence et l'automatisation, et utilise des avancées technologiques numériques pour mettre en œuvre des systèmes cyber-physiques (CPS) capables de communiquer entre eux et de prendre des décisions autonomes et décentralisées.
C'est cette capacité unique à consigner des données et à prévoir en temps réel qui permet d'améliorer l'efficacité industrielle, la productivité, la sécurité et la transparence pour un grand nombre de processus de fabrication.
L'interconnectivité permet d'optimiser des processus et des fonctionnalités auparavant inaccessibles dans la fabrication. Elle est communément connue sous le nom d'Industrie 4.0 ou d'Internet industriel des objets, et elle est en train de révolutionner à jamais la fabrication industrielle.
PRISE DE DÉCISIONS FONDÉES SUR LES DONNÉES
Alors, qu'implique l'Internet industriel des objets pour l'avenir de la fabrication, et comment fonctionne-t-il ?
Dans le cadre de l'Industrie 4.0, les composants et les équipements qui fonctionnent dans l'usine, notamment la robotique autonome, doivent être intégrés avec des capteurs et une connectivité Internet qui permettent aux fabricants, sous-traitants et constructeurs de machines de collecter et d'analyser des données en continu.
Les données collectées peuvent être utilisées pour améliorer les opérations en usine, suivre les performances des équipements, prévoir la maintenance et réduire les temps d'arrêt des machines. Prenons l'exemple de la tâche consistant à planifier la maintenance d'un composant hydraulique critique d'un bras robotisé ou d'une machine d'usine. Les décisions à prendre concernant l'arrêt du système, l'interruption des opérations et la réalisation des opérations de maintenance dépendent de plusieurs facteurs.
Quel est le calendrier de production ? Des temps d'arrêt sont-ils prévus ? Quel est le coût du remplacement ? Quel est le coût de la perte de performance par rapport au coût de remplacement ? Combien de temps la machine sera-t-elle arrêtée ? Si un composant usé n'est pas remplacé, en quoi cela affecte-t-il les performances ou la sécurité ?
Comprendre les réponses à ces questions est essentiel pour prendre de meilleures décisions. Toutefois, il est tout aussi important de collecter et d'analyser les données pertinentes de manière à pouvoir fournir des informations exploitables sur la machine elle-même.
SURVEILLANCE DES MACHINES DE FABRICATION
Alors que les constructeurs et les fournisseurs de machines sont confrontés à une pression commerciale croissante pour être en mesure de contrôler et d'entretenir plus efficacement de nombreux systèmes et appareils différents (notamment dans le cadre des calendriers de maintenance), les composants intelligents – produits dotés d'interfaces de diagnostic et de communication – deviennent monnaie courante. Avec l'installation d'équipements adaptés, la durée des diagnostics des machines peut être réduite jusqu'à 70 %.
Par exemple, dans le passé, un filtre encrassé pouvait entraîner des temps d'arrêt et nécessiter une intervention sur site. À l'heure actuelle, cette condition peut déclencher une alerte indiquant que le filtre doit être remplacé, ce qui permet d'assurer un fonctionnement sans interruption. Dans certains cas, l'utilisation de composants intelligents évite aux contrôleurs humains de devoir surveiller les systèmes physiquement.
Grâce à l'accès à distance pour surveiller les machines et les mettre à jour, les contrôleurs peuvent garantir la productivité et résoudre rapidement les problèmes techniques sans être présents. Les données machine clés en temps réel, telles que la température, la pression/le couple, le débit, le courant et la tension, peuvent être transmises et analysées rapidement et en toute sécurité lorsque les paramètres de performance définis ne sont pas atteints. Ces données personnalisées peuvent fournir des recommandations aux opérations commerciales sur la façon d'optimiser les performances et de prolonger la durée de vie.
LES AVANTAGES DE L'INDUSTRIE 4.0 POUR LA FABRICATION
Les machines équipées de composants compatibles Industrie 4.0 peuvent bénéficier des avantages suivants :
- Connaissance des données de maintenance : permet de programmer des recommandations de maintenance basées sur l'utilisation de la machine ou son état avant la défaillance de l'équipement.
- Diagnostic et programmation à distance : fournit des informations détaillées sur les défaillances de l'équipement sans nécessité d'inspection physique. Il n'est pas nécessaire qu'un technicien se rende sur le site initialement, mais lorsqu'il le fait pour effectuer la tâche de maintenance, il s'assure d'avoir les bons outils et les bonnes pièces dès la première visite, ce qui permet de réduire les temps d'arrêt, les coûts de main-d'œuvre et les coûts de déplacement.
- Localisation et suivi : enregistre où, quand et combien de temps chaque machine est utilisée. Cela permet de définir des alertes si un équipement d'usine dépasse une limite définie afin d'éviter les temps d'arrêt imprévus.
- Rapports automatisés : cette fonction permet de générer des rapports personnalisés à intervalles spécifiques pour comprendre les principaux KPI et performances de l'usine.
- Utilisation et emploi des machines : cette fonction permet de vérifier l'efficacité opérationnelle en temps réel, et de surveiller les paramètres clés, notamment l'état des machines, le rendement des équipements et l'OEE.
- Fréquence et durée d'utilisation : cette fonction enregistre et indique la fréquence et la durée d'utilisation de chaque machine d'usine. Elle peut contribuer à la répartition efficace des ressources en équipements et à la gestion des accords de garantie.
LA CONNAISSANCE : LA CLÉ D'UNE PRODUCTION RENTABLE
L'Industrie 4.0, la transformation numérique et l'interconnectivité sont essentielles à la rentabilité future de l'industrie manufacturière. Ces technologies révolutionnent le mode de fonctionnement du secteur.
Les produits de contrôle et de mouvement compatibles créent de la valeur pour le client grâce à des gains de disponibilité et de productivité en exploitant pleinement les capacités d'analyse de l'IoT. L'investissement dans l'Industrie 4.0, notamment dans le secteur des équipements industriels, permet d'accéder à des quantités sans précédent de données qui peuvent fournir des informations sur les opérations et donner aux entreprises un avantage concurrentiel, ce qui se traduit par une rentabilité accrue. L'expérience a prouvé que l'investissement dans une solution IoT est financièrement avantageux au cours des deux premières années. Comprendre l'état actuel d'un actif, ainsi que les répercussions des éventuelles mesures nécessaires, permet d'évaluer les coûts et les avantages des décisions avant qu'elles ne soient prises, ce qui aide à déterminer la meilleure stratégie pour optimiser la productivité et, par conséquent, la rentabilité.
RECOURS À L'INDUSTRIE 4.0 POUR INNOVER ET RENFORCER LA FIDÉLITÉ DES CLIENTS
Pour les OEM et les constructeurs de machines, l'Industrie 4.0 peut offrir des avantages uniques et inattendus. En exploitant les données des solutions IoT industrielles d'un fournisseur de composants comme Parker, les OEM et les constructeurs de machines peuvent non seulement améliorer leurs concepts d'ingénierie et de conception, mais aussi créer des équipements différents qui nécessitent moins de simulation et de modélisation à l'étape de la conception.
Cela permet de stimuler l'innovation et de créer de nouvelles possibilités pour les fabricants, ainsi que d'améliorer les relations commerciales et de fidéliser davantage la clientèle du fournisseur. À partir des données en temps réel de l'infrastructure existante, les possibilités offertes pour élaborer de nouvelles conceptions, voire de nouvelles utilisations des équipements, peuvent mener à l'ouverture de nouveaux marchés et au développement de nouvelles gammes de produits pour les OEM et les constructeurs. Il s'agit d'un énorme avantage pour ces acteurs qui souhaitent conserver une longueur d'avance sur la concurrence et accroître leur rentabilité.
Les OEM et les constructeurs d'équipements devront se rendre compte que les systèmes intelligents et connectés peuvent également aider leurs clients à réduire leurs coûts, à optimiser leur productivité et à réduire les temps d'arrêt. Les solutions IoT industrielles, comme la surveillance de l'état des actifs et les systèmes hydrauliques, tels que ceux proposés par les experts du contrôle et du mouvement Parker, ajoutent non seulement de la valeur pour les clients des OEM, mais renforcent également la fidélité à la marque du fournisseur, surtout si les offres concurrentes ne sont pas intégrées à une solution IoT. Grâce à une solution IoT axée sur le client, il est possible de répondre aux exigences spécifiques des OEM, ce qui permet de réduire les coûts grâce à une production plus efficace et de générer des revenus grâce à un meilleur rendement des lignes et une meilleure qualité de production.
RÉDUCTION DES COÛTS DE GESTION DE L'USINE
L'utilisation de solutions IoT industrielles de pointe bouleverse aussi la maintenance en usine. Les responsables de la maintenance peuvent désormais recevoir des données en temps réel sur l'état mécanique et l'utilisation d'actifs coûteux, notamment des données déterminant l'état des machines, l'efficacité des équipements, les coûts des temps d'arrêt, l'OEE et d'autres facteurs contribuant aux coûts de gestion de l'usine. Avec cette capacité, les responsables de la maintenance en usine peuvent ainsi être proactifs et réparer les équipements avant qu'une panne ne se produise, évitant ainsi les pertes de revenus.
Les solutions d'IoT industriel de Parker aident également les responsables de la maintenance en usine à mieux comprendre leurs facteurs de coût et de rendement. La possibilité de suivre l'utilisation des équipements à la minute près et de surveiller les événements connexes, comme le rendement et la maintenance, permet de mieux calculer les coûts, de planifier la maintenance et de réduire les temps d'arrêt imprévus.
VERS DES AMÉLIORATIONS OPÉRATIONNELLES EN TOUTE SÉCURITÉ
L'Industrie 4.0 offre de nombreuses améliorations qui ne sautent pas aux yeux au premier abord. La sécurité en fait partie. Ces améliorations contribuent grandement à réduire le risque de temps d'arrêt imprévus pour les opérateurs et les responsables. Voici comment cela fonctionne. Les données collectées permettent d'adapter les possibilités d'accompagnement pour les opérateurs dont le comportement sur site n'est pas conforme aux règles établies par l'entreprise, notamment concernant les procédures d'utilisation des équipements et les programmes de maintenance. L'Industrie 4.0 peut également améliorer les procédures opérationnelles sur site en permettant aux techniciens en chef, qui ne sont pas sur place, de contribuer à la résolution des problèmes qui ne peuvent pas être traités par les techniciens débutants en service. L'Industrie 4.0 peut fournir d'autres fonctions de surveillance et d'alertes, notamment :
Gains de productivité
Surveille les paramètres de fonctionnement, analyse et détermine l'état pour prévoir les performances et les défaillances.
Surveillance des paramètres opérationnels clés
Réduit le risque de fonctionnement inefficace des machines.
Amélioration du rendement opérationnel
Émet des alertes et des alarmes en fonction des conditions limites d'exploitation de l'usine.
Réduction des temps d'arrêt
Réduit des temps d'arrêt par la prévision des défaillances avant qu'elles ne surviennent.
L'investissement dans la technologie Industrie 4.0 devient extrêmement intéressant si l'on considère le coût d'une solution IoT par rapport au coût par temps d'arrêt imprévu. En utilisant la technologie de surveillance, les entreprises peuvent améliorer leur rendement opérationnel, réduire les temps d'arrêt et obtenir des gains de productivité. L'Industrie 4.0 peut apporter des améliorations et des gains :
- jusqu'à 30 % d'augmentation de la productivité ;
- jusqu'à 28 % de réduction des temps d'arrêt machine ;
- jusqu'à 47 % d'amélioration du rendement opérationnel ;
- jusqu'à 28 % de réduction des temps d'arrêt imprévus.
INDUSTRIE 4.0 ET DÉVELOPPEMENT DURABLE
Aujourd'hui plus que jamais, les entreprises doivent être gérées de manière durable. La protection de l'environnement est essentielle, mais l'exploitation d'une entreprise respectueuse de l'environnement peut s'avérer une tâche difficile et très coûteuse, surtout si vos équipements sont inefficaces. Les solutions d'IoT industriel peuvent avoir un impact positif sur l'environnement en fournissant des données permettant aux entreprises de réduire leurs émissions causées par la surutilisation de leurs équipements d'usine.
En optimisant l'utilisation des machines en usine et en améliorant le rendement, il est possible de réduire la consommation de carburant et de ressources, ainsi que les émissions rejetées. Par ailleurs, bien que l'utilisation des machines soit globalement réduite, grâce aux économies et aux meilleures pratiques créées à partir de l'utilisation de composants intelligents, la productivité est optimisée et l'utilisation de matières premières est réduite. En résumé, les solutions Industrie 4.0 contribuent favorablement au développement durable en réduisant l'utilisation d'équipements, de ressources et de matériaux, ce qui permet de réduire l'empreinte carbone.
MISE EN ŒUVRE D'UN SYSTÈME INDUSTRIE 4.0 IDÉAL
Pour les OEM ou les constructeurs de machines, la conception d'une plateforme IoT en interne peut s'avérer coûteuse et nécessite généralement des années de développement. La meilleure façon d'y parvenir est de s'adresser à un leader reconnu dans le domaine du contrôle et du mouvement hydraulique comme Parker et de collaborer directement ensemble. Vous bénéficierez non seulement de l'expertise complète en intégration technologique et en analyse de données dont dispose Parker, mais aussi d'un portefeuille complet de solutions intelligentes et connectées permettant de développer des approches hautement sécurisées, évolutives et axées sur les données pour votre entreprise. Votre entreprise dispose ainsi d'une solution intégrée d'appareils intelligents et connectés, de contrôleurs et d'API en usine, ainsi que du logiciel performant nécessaire à son exécution, le tout dans un écosystème numérique transparent.
www.parker.com