www.industrie-afrique-du-nord.com
19
'14
Written on Modified on
Le système d’entraînement sans armoire le plus flexible : le nouvel IndraDrive Mi de Rexroth
L'intégration complète de l'ensemble motopropulseur dans la machine améliore la flexibilité et le rendement
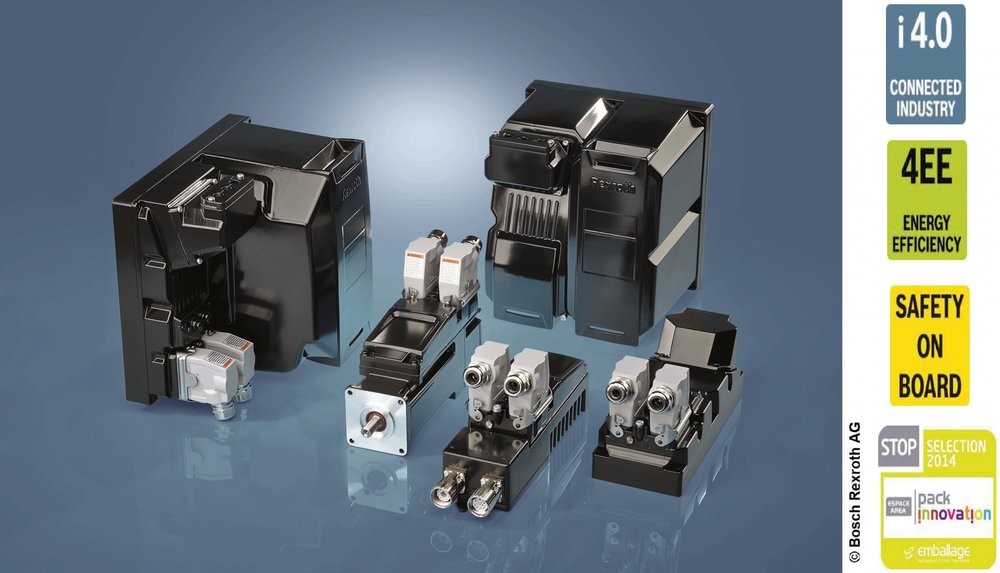
Le câblage des composants électriques d'une machine dans l'armoire de commande prend beaucoup de temps, représente un coût non négligeable et est une source d'erreurs. De plus, un système de refroidissement gourmand en énergie est souvent nécessaire. Dans le même temps, un nombre croissant d'utilisateurs demandent des machines plus compactes, afin d'améliorer le rendement des sites de production. Les concepts de machine sans armoire de commande permettent de réaliser des économies considérables et améliorent la flexibilité.
Alimentation décentralisée et module secteur en IP 65
Rexroth a montré la voie dans ce domaine dès 2007 avec l’IndraDrive Mi, le premier système d’entrainement mondial intégré au moteur. Seuls les composants d'alimentation nécessitaient alors un espace, déjà limité, dans l'armoire de commande. Aujourd'hui, le fabricant d'entraînements et de systèmes de commande va encore plus loin : la totalité du système d'entraînement peut désormais être intégrée directement dans la machine, le module d'alimentation étant aussi exécuté en IP 65. Le module secteur rassemble le filtre, la self de comutation et le contacteur réseau dans un seul équipement, qui est directement relié au secteur. Le module d'alimentation régénérative à système de contrôle électronique, résistance de freinage et transistor de freinage a totalement remplacé l'alimentation et le système de contrôle électronique de l'armoire de commande. Tous les composants jusque-là situés dans l'armoire de commande ayant été supprimés, cette dernière est donc désormais obsolète.
Pour sa technologie d'entraînement sans armoire, Rexroth a également mis au point un nouveau contrôleur monobloc doté d'un courant maximal de 36 A. Utilisateur pilote, le fabricant de machines d'emballage Gerhard Schubert GmbH a dévoilé le tout premier modèle sans armoire au printemps dernier, à l'occasion du salon interpack 2014.
Flexibilité accrue et réduction des coûts
La technologie d'entraînement sans armoire comporte de nombreux avantages pour les fabricants de machines : l'installation et les coûts associés sont considérablement réduits, tout comme l'espace requis pour la machine. La technologie d'entraînement sans armoire ouvre également de nouvelles possibilités de modularisation et renforce la flexibilité pour les machines configurées individuellement. Les fabricants peuvent désormais assembler entièrement les modules au préalable, puis les mettre en service sans devoir les relier par câble à l'armoire de commande de la machine. De cette façon, l'association de plusieurs modules est considérablement simplifiée en termes d'installation. Il suffit désormais d'alimenter chaque module, puis de le connecter au contrôleur de la machine via un seul câble hybride.
Multi-Ethernet pour une utilisation universelle
Des entraînements flexibles peuvent être ajoutés ou retirés de l'ensemble motopropulseur ultérieurement. Par ailleurs, IndraDrive Mi prend en charge tous les protocoles Ethernet courants tels que Sercos, ProfiNet, EtherNet/IP et EtherCAT via l'interface Multi-Ethernet sur un seul matériel. Une connexion avec Profibus est possible via une passerelle. Cela permet aux fabricants de machines d'intégrer dans le matériel des modules identiques via les différents protocoles de communication préférés de l'utilisateur final.
De 3 000 à seulement 110 m de câbles
IndraDrive Mi repose sur des servomoteurs intégrés au moteur ou monobloc. En général, 20 entrainements IndraDrive Mi sont utilisées pour former un système d'entraînement, via un harnais de câbles de 200 mètres maximum. Selon le type d'alimentation, la longueur des câbles et les options choisies, un nombre bien plus important d'entraînements peut être connecté en série. Rexroth utilise un câble hybride pour l'alimentation et la communication.
Cette méthode réduit le câblage jusqu'à 90 % par rapport aux systèmes d'automatisation habituels. Voici un bref exemple de calcul : pour un système d'automatisation doté de 50 entraînements et d'une armoire de commande, la longueur totale des câbles atteint facilement 1 500 mètres, auxquels il faut ajouter la même longueur pour le câble du codeur. En comparaison, un système sans armoire ne nécessite que 110 m de câbles. Cela réduit les coûts de matériel et le temps d'installation, ainsi que le risque d'erreurs de câblage.
Mais les économies potentielles ne s'arrêtent pas là, car les détecteurs, les E/S et les composants de bus de terrain peuvent être connectés directement aux entraînements IndraDrive Mi. Les périphériques décentralisés sont reliés via le Multi-Ethernet.
Réduction de moitié de la consommation électrique
Le couplage énergétique inhérent au système via le câble hybride commun permet d'échanger l'énergie entre les moteurs. Par exemple, lorsqu'un moteur freine, l'énergie de freinage peut être distribuée simultanément à un système d'entraînement en cours d'accélération. L'énergie est soit utilisée au sein du système, soit redistribuée sur le réseau électrique. Cela permet de réaliser jusqu'à 50 % d'économies d'énergie. Grâce à la réduction importante du volume de câbles, le module a également été allégé. Dans de nombreux cas, cela permet aux moteurs d'être plus compacts, ce qui optimise davantage leur rendement.
De la solution décentralisée à la sécurité fonctionnelle
Le concept de décentralisation signifie aussi la conformité avec la directive européenne relative aux machines. De Safe Torque Off à Safe Motion, Rexroth propose aussi des fonctions de sécurité certifiées dans le cadre de ses solutions IndraDrive Mi sans armoire de commande. Les équipementiers bénéficient ainsi de différentes zones de sécurité pouvant être activées séparément par l'utilisateur final. En cas d'intervention manuelle, il n'est pas nécessaire d'arrêter toute la machine : seule la zone de sécurité concernée est désactivée. Cela simplifie la procédure de démarrage et raccourcit le temps de redémarrage de la machine après la réparation d'un dysfonctionnement.
Prêt pour l'Industrie 4.0 grâce au contrôleur intégré au moteur
La modularisation appliquée à la conception des machines a progressivement transféré les fonctions de contrôle aux modules individuels d'une machine. Avec la commande intégrée à l'entraînement de Rexroth, les fonctions d'entraînement, le contrôle du mouvement et la logique d'exécution fusionnent pour former une plateforme d'automatisation ouverte. Ce système, appelé Motion Logic, est conforme à la norme CEI 61131-3 et est également capable de réguler les tâches de mouvement complexes. La commande d'entraînement Rexroth peut coordonner en temps réel neuf unités IndraDrive Mi configurées en tant qu'esclaves. Le fabricant de machines peut ainsi configurer des mouvements et processus complexes grâce à une technologie d'entraînement intelligente. Ces fonctions partielles peuvent être créées sous forme de modules logiciels. Cela est aussi possible lorsque différents contrôleurs de machine sont employés. Ce processus de décentralisation et de modularisation gagne de l'importance. Avec les interfaces ouvertes, il constitue l'une des conditions préalables à l'intégration horizontale et verticale imposée par les concepts de l'Industrie 4.0.
Des avantages pour le fabricant et pour l'utilisateur
La technologie d'entraînement sans armoire présente un important potentiel d'économies en matière de coût de production et accroît le degré de liberté pour la mise en oeuvre de concepts modulaires. L'utilisateur final peut installer davantage de machines au même endroit et réduire à la fois la consommation électrique.
Les machines dont le système d'entraînement est totalement ou partiellement logé dans une armoire conserveront une part de marché, mais celle-ci est amenée à baisser, compte tenu du gain de flexibilité apporté par la technologie d'entraînement sans armoire.
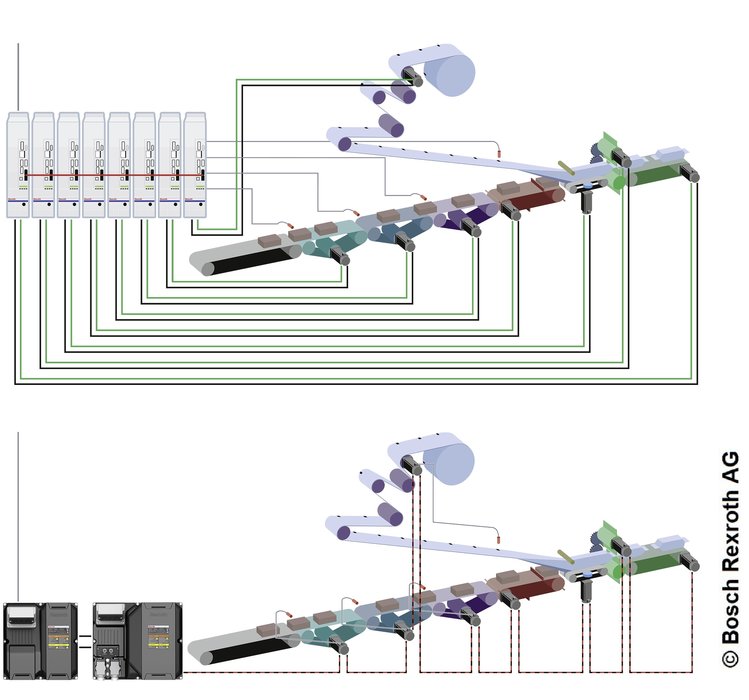
Suppression de l'armoire de commande et jusqu'à 90 % de câbles en moins: la technologie d'entraînement sans armoire simplifie l'automatisation et améliore la flexibilité.
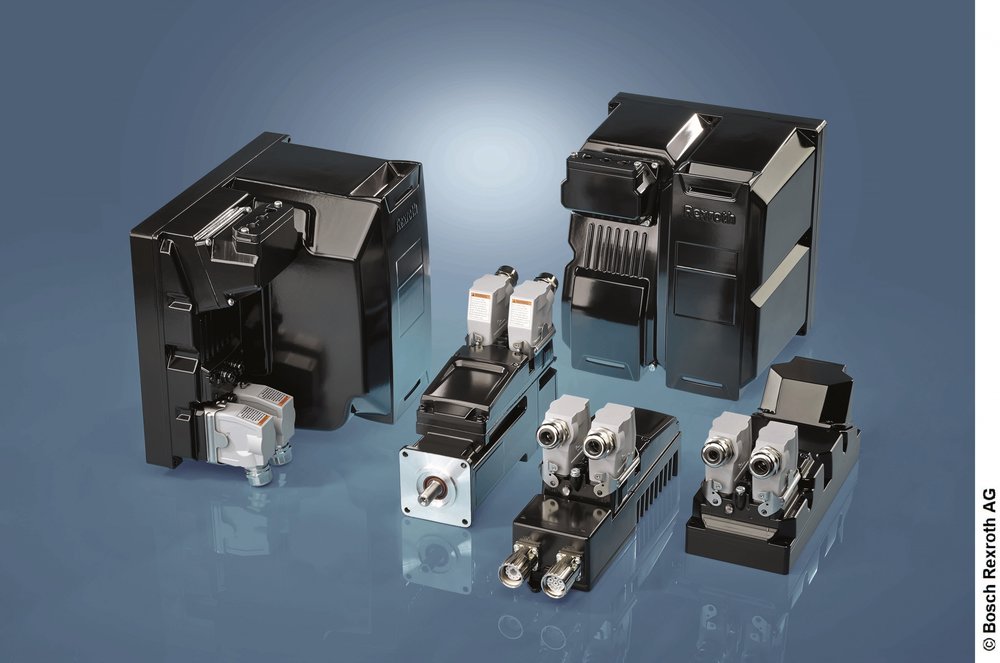
Tous les composants du système d'entraînement peuvent être intégrés directement dans la machine : grâce à cet agencement, les composants d'alimentation jusque-là situés dans l'armoire de commande sont supprimés