www.industrie-afrique-du-nord.com
27
'13
Written on Modified on
Tournage vertical pour une efficacité maximale
Siegerland Bremsen a été fondée en 1958. Initialement, son offre se limitait à des fabrications personnalisées de freins à tambour. En 1986, la société a été rachetée par la famille Kring et l’outil de production a été modernisé - tous les investissements se sont concentrés sur des machines à commande numérique. La société a également mis l‘accent sur internalisation et possède à présent des succursales en Espagne, en Chine (depuis 1999) et en Inde. La gamme de produits comprend des freins industriels pour des applications comme les équipements portuaires, les bandes transporteuses, les aciéries, les éoliennes, les systèmes de levage, et, en tant qu’un ajout récent, des ensembles complets d’essieux montés pour les grues.
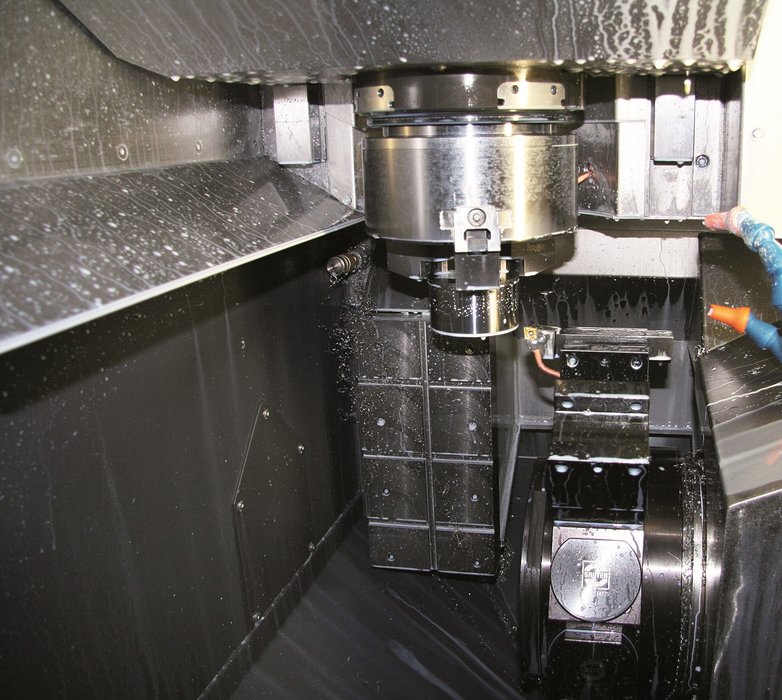
Quand il s‘agit de machines-outils, Andreas Jung, directeur de l’usine à Siegerland Bremsen, ne peut pas se tromper. Après tout, dans sa «première vie professionnelle» - qui a duré 33 ans - il a occupé plusieurs postes différents dans la machine-outil chez le fabricant Waldrich à Siegen. Grâce à cette expérience, il connait forcément ses machines-outils. Et quand quelqu‘un comme Andreas Jung a que des choses positives à dire sur une machine, alors cela a une réelle signification. À cet égard, nous parlons du modèle Emco VT 250. Deux tours verticaux, fabriqués à Hallein, sont actuellement utilisés à Siegerland Bremsen où ils ont révolutionné (au sens propre) la production de composants hydrauliques - même si cela a été de manière progressive.
Selon le site Web de la société, «Le système de freinage est le dernier maillon d‘une chaîne de composants liés à la sécurité dans un système d’entraînement. Une équipe d‘ingénieurs, de techniciens et de concepteurs hautement qualifiés réalise des développements continus dans la technologie de freinage qui vont garantir une solution adaptée en dépit de système d’entraînement de plus en plus complexes. « Les freins de la série Texu résultent de ces constants efforts. Ceux-ci sont des freins à disque à double effet pour lesquels, de manière analogue aux freins à tambour, la force de freinage est transmise de façon symétrique des deux côtés, compensant les forces radiales sur l‘arbre de frein. Ce qui rend ce frein spécial, c‘est que les deux étriers de frein opposés peuvent être actionnés simultanément par deux ressorts montés en parallèle, en combinaison avec un actionneur électro-hydraulique monté de façon concentrique. Malgré l’évolution constante de sa gamme de produits au fil des années, une chose n‘a jamais changé chez Siegerland Bremsen: l’importance accordée à l‘intégration verticale, d’abord pour assurer la qualité et ensuite pour maîtriser les temps d‘usinage et donc de livraison. Selon Andreas Jung, il y a un refus intentionnel de se plier aux méthodes et philosophie de production communément admises : «Contrairement à beaucoup d‘autres entreprises, nous gardons un stock très grand de pièces. Cela nous permet à la fois de concevoir de manière optimale nos processus de production de pièces et de maintenir une grande capacité à livrer rapidement. Cela correspond parfaitement à notre structure. „Presque toutes les pièces de nos produits sont donc fabriquées sur notre site de production de Haiger-Rodenbach, puis transférées à l‘usine d‘assemblage à proximité.
Parmi les pièces fabriquées en plus grand nombre, un composant de systèmes hydrauliques est produit à une cadence pouvant atteindre 5000 unités par mois. Face à cette quantité sans cesse grandissante, il a fallu complètement repenser les méthodes et moyens utilisés auparavant. Andreas Jung: «Comme vous vous en doutez, nous avons examiné toutes les options, de l’usinage complet via une machine complexe avec une broche principale et une contre-broche, jusqu’à une solution à base robotique pour alimenter en pièces deux tours simples. Initialement, nous avons privilégié une solution avec deux tours horizontaux simples mais un collaborateur nous a suggéré l‘utilisation d’un tour vertical. J‘avais effectivement envisagé cette technologie à un moment donné, mais le coût de ce type de machine aurait été tout simplement trop élevé pour les tâches d‘usinage en question ».
La principale raison est que, en tant que fournisseur, vous avez principalement à faire face aux «suspects habituels» et ce n‘est que lorsque nous avons découvert le nom de EMCO (et la liste des prix) que nos recherches sur les tours verticaux ont pris tout leur sens. Il est rapidement devenu évident que lorsque l‘on prend en compte la géométrie des pièces, les dimensions et les quantités relativement élevées, le tournage vertical est une technologie de coût bien inférieur à celui d‘une solution classique avec tours horizontaux.
À la lumière de cela, il était relativement facile de convaincre la direction du sens de cette aventure et nous avons investi dans un Emco VT 250 assez rapidement. Et il n’a fallu qu’un peu plus de cinq semaines avant que Andreas Jung n‘ait dû avouer à sa direction qu‘il avait mal évalué les choses lors de l‘achat de la machine. « J’ai dit à mon manager que j‘avais fait une erreur lors de l’achat de la VT 250. Je n’aurais pas dû commander juste une machine; J‘aurais dû en commander deux tout de suite. Juste après la première commande du VT 250, il est devenu évident que cela avait dépassé instantanément toutes nos attentes et que le tour vertical avait certainement mérité toutes les éloges qu‘il avait reçu ».
«Nous avons délibérément choisi de ne pas aller plus loin dans l‘automatisation. Je suis sûr que cela aurait réduit encore davantage la charge de travail pour l‘opérateur du tour, mais nous n‘aurions pas produit une pièce supplémentaire car quelqu‘un d‘autre aurait été nécessaire sur la machine pour effectuer des contrôles de qualité et des activités d’emballage simple ». De plus au sujet de l’automatisation, « si à n’importe quel moment des pièces doivent être produites en quantités inférieures, nous pouvons simplement les usiner sur la deuxième machine verticale sans réajustement ». Le site de Rodenbach a identifié suffisamment de pièces qui pourraient être produites sur ces équipements. « Une fois que vous avez installé la technologie de tour vertical, vous découvrez de plus en plus de potentiel d’utilisation ».
Après l‘installation de la deuxième VT 250, Andreas Jung a fait un premier bilan: «Nous avons réduit de moitié le temps d‘usinage, ce qui nous a permis de doubler la capacité. Il est logique que cela affecte également les coûts unitaires de chaque composant. Dans les faits, les quantités produites ont nettement augmenté depuis que nous avons commandé la première machine Emco, ce qui signifie que la réduction des temps d‘usinage a un effet très concret». De plus, «Nous utilisons certes deux machines, mais celles-ci ont un encombrement au sol beaucoup plus compacte que l‘ancienne solution et nous n‘avons besoin que d‘un seul opérateur que deux auparavant».
Mais ce ne sont pas les seuls avantages: «Auparavant, nous étions tout simplement incapables de créer les finitions souhaitées en interne et nous devions sous-traiter des pièces pour la finition. Maintenant, avec une solution basée sur des outils adaptés et les tours verticaux Emco, nous obtenons des résultats meilleurs qu‘avec notre ancien fournisseur. Les pièces sortent de la machine préfinies et vont directement vers le processus d‘assemblage ».
Herbert Bremer, chef de produit chez Emco Magdeburg AG, est responsable des tours verticaux et commente les avantages de ce processus : « les tours verticaux sont des machines de production multi-usinages qui ont un faible encombrement et qui peuvent être rapidement modulées. Par ailleurs, il n‘est pas nécessaire de remplacer ou de configurer les pinces de préhension pour la manipulation automatique des pièces à usiner, parce que celles-ci peuvent simplement être placées dans des systèmes de convoyage automatique. De fait, cela ne nécessite ni conversion ni palette, comme c‘est le cas à Sibre. De plus, il ne faut pas oublier l‘évacuation optimale des copeaux ».

Il a également commenté les points forts spécifiques du VT 250: «Ce n‘est pas comme si Emco avait inventé le tournage vertical, mais ce que nous avons réussi à faire, c‘est d’offrir à nos clients cette technologie d‘usinage à prix bas sans compromettre la qualité ou la précision. En outre, le VT 250 est une machine extraordinairement stable qui a été conçu pour l‘usinage à haut rendement. Le VT 250 est également équipé de la commande numérique Siemens 828D Solution Line, qui dispose d‘un système de refroidissement avec une pompe de 14 bar et offre beaucoup d‘espace de stockage pour les outils grâce à deux systèmes indépendants (12 positions de tourelle porte outils et une plaque multifonctionnelle pour les outils spéciaux). La machine satisfait presque à tous les besoins ».
Enfin, revenons à un autre commentaire d’Andreas Jung: «Autrefois, je n’étais lié à Emco que pour les machines de formation. Au sein de Siegerland, j‘ai eu mes premières expériences avec des machines de production Emco à travers le modèle EMCOTURN 365 - et j’ai été extrêmement surpris par la répétabilité et la précision de la machine. Avec les deux VT 250, nous avons trouvé l’outil de production idéal pour nos besoins et nos gammes de pièces. Nous penserons toujours à Emco pour nos futurs investissements ».
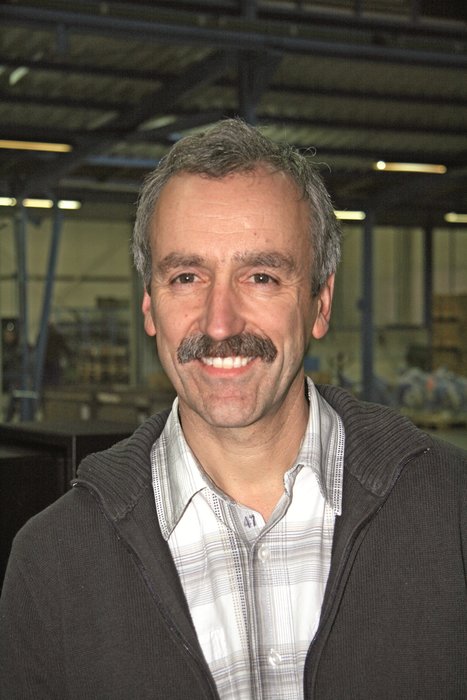
Andreas Jung, directeur de l‘usine à Siegerland Bremsen
“Il est devenu clair que l’alimentation automatisée des pièces rend la machine beaucoup plus facile à utiliser. Deux personnes ne sont plus nécessaires, comme avec la solution horizontale. Au lieu de cela, comme toutes les opérations importantes sont menées sur un tour vertical, un opérateur suffit. „La direction est allée aussi dans ce sens et une seconde VT 250 a été commandée après quelques semaines du premier achat. Celle-ci a été installée avec un angle de 180 ° par rapport à la première machine de sorte que les deux courroies d‘alimentation fonctionnent en parallèle les unes à côté des autres ».
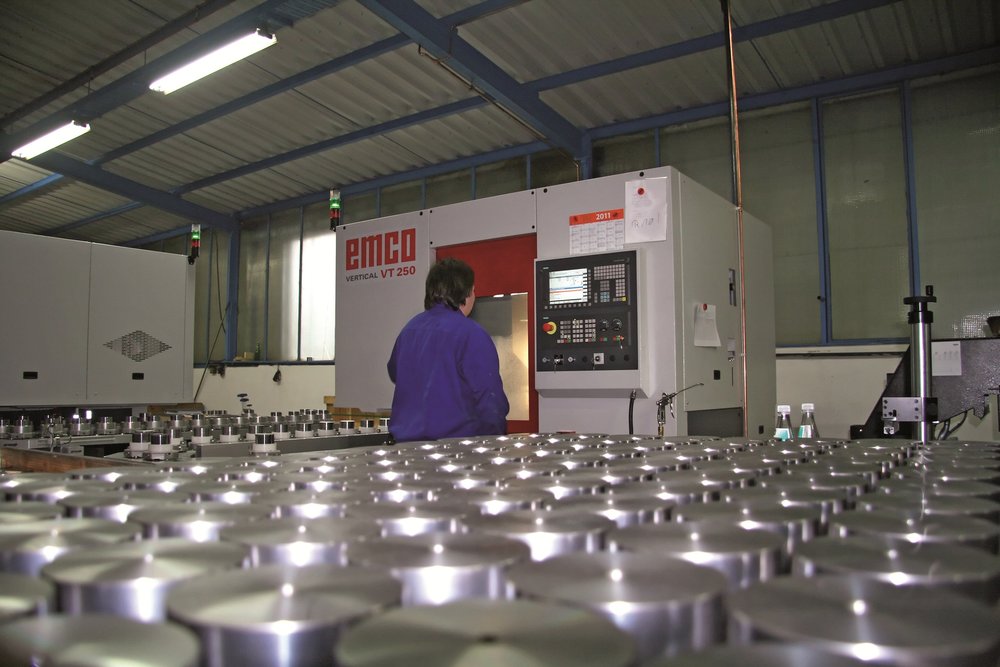
Chargement rapide grâce à la préhension directe par la broche de la matière à usiner
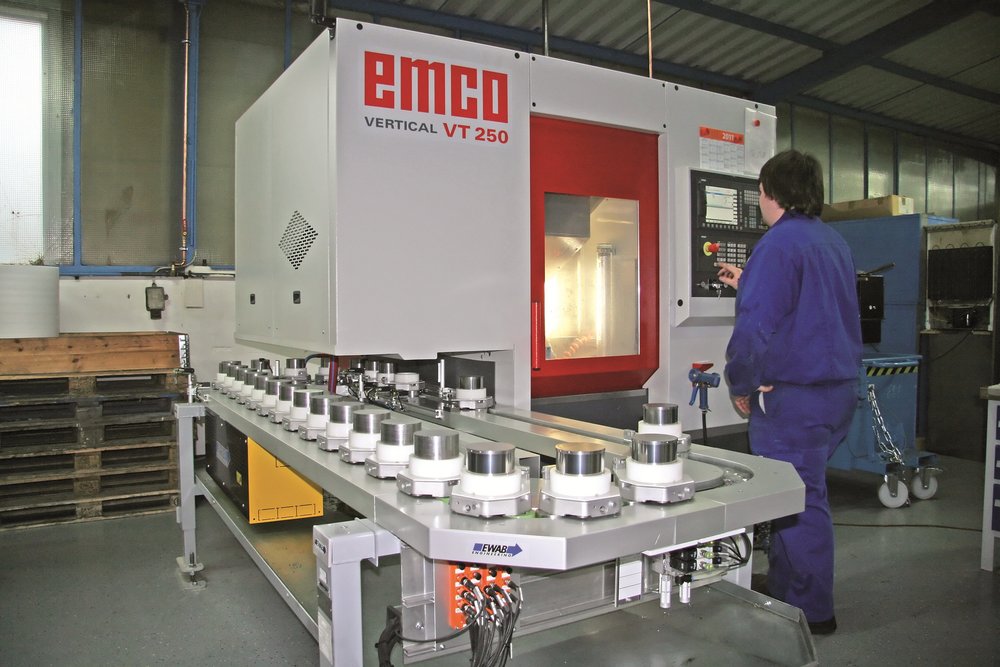
La VT 250 est une machine extraordinairement stable qui a été conçue pour l‘usinage à haut rendement
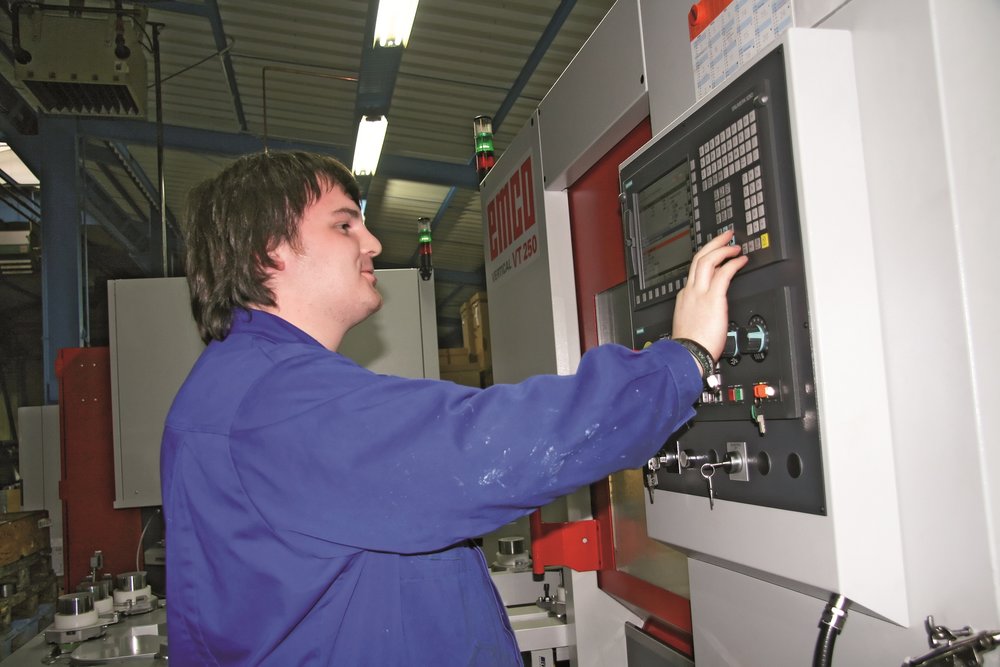
Une capacité doublée grâce à une réduction de moitié du temps d‘usinage, le tout, avec un seul opérateur au lieu de deux auparavant
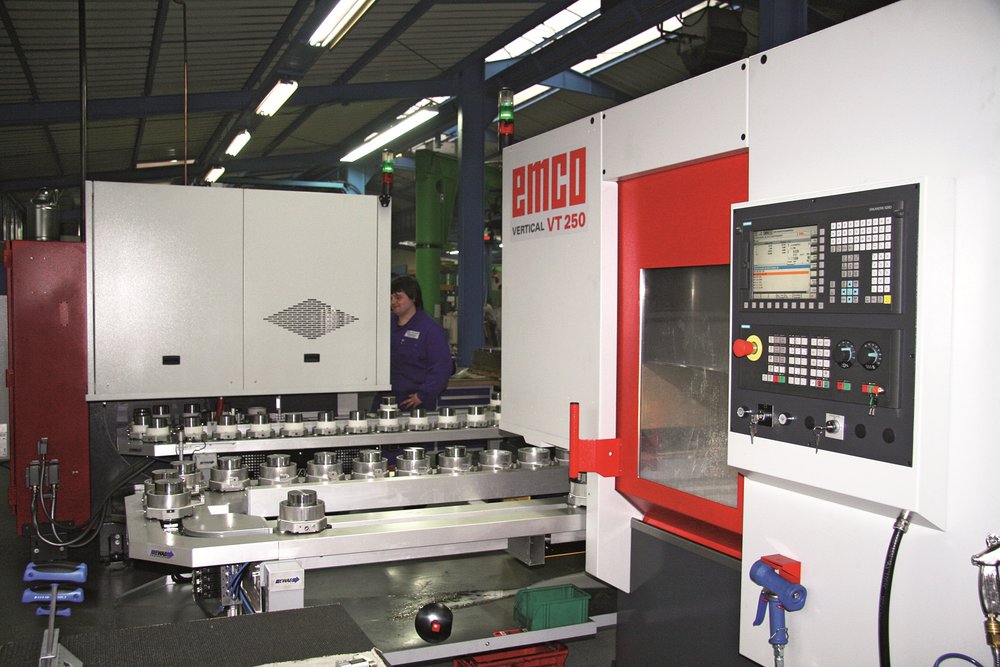