www.industrie-afrique-du-nord.com
12
'20
Written on Modified on
LE RAINURAGE EN TOUTE FIABILITÉ
Afin de pouvoir séparer des circuits imprimés, ceux-ci sont préalablement rainurés, les découpes et les contours sont fraisés. Dans ce but, la société LHMT GmbH développe des machines-outils hautement spécialisées grâce auxquelles non seulement le processus de rainurage et de fraisage proprement dit a lieu de manière entièrement automatique, mais aussi le chargement et le déchargement des platines sensibles. Pour une manipulation sûre et en douceur, LHMT s’est adressé aux experts de l’entreprise J. Schmalz GmbH, lesquels ont pu mettre en œuvre une solution de préhension fiable, entre autres grâce aux nouvelles ventouses NBR-ESD.
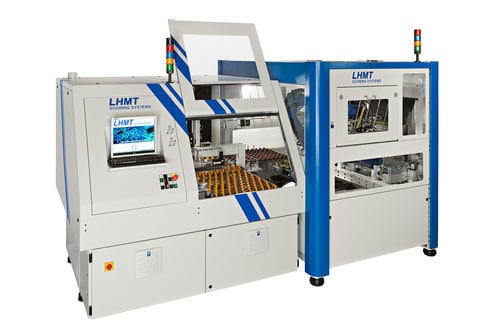
Les machines produites à Neuhausen, près de Pforzheim dans le Bade-Wurtemberg, font ultérieurement partie d’un processus de fabrication moderne. En effet, la société LHMT GmbH développe des machines spéciales dans le domaine de la technique d’automatisation et CNC, ainsi que l’automation robotisée et le traitement d’images pour l’industrie des semi-conducteurs. LHMT, « Leiterplatten-Handling und Manufacturing Technologies », (« Technologies de manipulation et de fabrication des circuits imprimés » – le nom de la société en français) a ouvert ses portes en 2002 et fait partie du groupe « Schmoll-Maschinen », lequel met au point des installations pour la production électronique de masse et le micro-usinage.
Un circuit imprimé terminé passe par de nombreuses étapes de processus différentes avant d’être prêt à être intégré. Des procédés chimiques humides tels que la gravure du cuivre au perçage et à l’exposition, le produit brut doit endurer beaucoup de choses avant d’arriver dans les machines LHMT. Dans ce contexte, les dispositifs de manipulation de la société LHMT servent au chargement et au déchargement des différents processus de fabrication. Avec les machines de rainurage, le panneau individuel, c’est-à-dire le circuit imprimé entier, reçoit à la fin de son processus de fabrication complet ses positions de rupture, afin de permettre plus tard la séparation de chaque circuit imprimé. Il s’agit là d’une étape importante, car la phase d’usinage fournit au circuit imprimé l’agencement requis pour l’utilisation ultérieure. Knut Handte, directeur de la construction de la société LHMT GmbH, déclare : « Étant donné que les pièces sont de plus en plus fines et sensibles, nous misons ici sur un procédé entièrement automatique ». En d’autres termes : les ébauches de circuits imprimés fournies dans des cassettes inclinées ou des supports de produits sont automatiquement retirées individuellement par un dispositif de manipulation via un robot à 6 axes, les supports de broches sont mesurés par une caméra CCD (Charge Coupled Device), puis les ébauches sont ensuite transférées vers la machine à rainurer.
Un objet sensible
« Ce qui peut paraître simple implique plusieurs défis à relever. La raison : il existe de très nombreux types de circuits imprimés différents », souligne Handte. Tandis que les smartphones contiennent des platines particulièrement fines et légères, on utilise dans des serveurs plutôt des versions épaisses et massives avec beaucoup de cuivre. Le point commun de tous les exemplaires est la surface extrêmement sensible, laquelle doit être exempte d’empreintes. « C’est la raison pour laquelle la préhension a généralement lieu à l’extérieur, au niveau de l’arête dite aveugle, et évidemment à l’aide du vide », explique le directeur de la construction. Ce faisant, le préhenseur doit non seulement s’adapter aux différents formats, mais aussi aux alésages de référence existants. La machine à rainurer agit en conséquence et fournit ainsi un résultat précis. De plus, le préhenseur a de moins en moins de place : la complexité des platines augmente parallèlement à l’exigence de placer de plus en plus de fonctions sur des surfaces de plus en plus petites. « Nous devons également tenir compte du fait que différents circuits imprimés sont usinés sur nos machines. De fait, les étapes de processus et le système de manipulation doivent être universels et flexibles. C’est la seule manière pour nous d’éviter des temps d’équipement importants », ajoute Handte.
Cette flexibilité représente un défi notamment pour le système d’alimentation automatisé. En coopération avec les experts du vide de la société J. Schmalz GmbH, LHMT a élaboré et testé deux solutions d’automation différentes. L’une d’entre elles utilise un bras de robot flexible, lequel peut effectuer différentes étapes de chargement et de déchargement dans un espace restreint. En guise d’alternative, les circuits imprimés peuvent être récupérés au moyen d’un système à plusieurs axes puis placés sur le convoyeur à bande. « De tels systèmes sont certes moins onéreux que les robots, mais ils ne sont pas si flexibles. Par contre, le temps de cycle est nettement plus court avec des systèmes à 2 axes : actuellement, nous atteignons avec notre installation RobiFlex2x1 un temps de cycle inférieur à six secondes. En utilisant des couches intermédiaires, l’installation a besoin de onze secondes. Ce faisant, toutes les pièces sont saisies exclusivement par un préhenseur par le vide », explique le directeur de construction. Pendant que LHMT développait des composants mécaniques comme la connexion robot, le préhenseur ou le système à plusieurs axes, Schmalz a livré les composants pour le processus de manipulation : les ventouses et leur connexion au préhenseur. « Chaque circuit imprimé doit être manipulé avec minutie, sans laisser d’empreintes. En même temps, les séquences de mouvements rapides requièrent un maintien fiable du circuit, bien sûr sans le déformer », explique Christian Stoisser, responsable de la gestion des grands comptes et des branches internationales de Schmalz dans le domaine de l’électronique. Une autre particularité concernant les circuits imprimés et autres composants électroniques est le risque de causer des dommages en raison de décharges électrostatiques, entre autres dans le système électronique de puissance. Ceux-ci ne sont certes pas visibles, mais ils se manifestent au bout du compte lors du test de fonctionnement. « Notre processus de fraisage et de rainurage se trouve relativement loin à la fin de la chaîne de valorisation. Cela signifie que la valeur du circuit imprimé est déjà très élevée et que, pour cette raison, nous souhaitons maintenir le taux de rebut le plus réduit possible », explique Handte.
Une combinaison dissipatrice
Spécialement pour la protection contre un déchargement indésirable, Schmalz a développé des ventouses de type NBR-ESD équipées d’une résistance spécifique. En combinaison avec les tiges à ressort conductrices FSTIm, l’expert du vide garantit une bonne connexion dans chaque position du préhenseur et protège ainsi le circuit imprimé de manière fiable. Les ventouses sont montées sur des préhenseurs par le vide, lesquels sont conçus individuellement en profilés en aluminium. « L’aluminium léger est une condition de base pour des temps de cycle courts. Un préhenseur mécanique rendrait la construction trop lourde et le robot ne pourrait plus se déplacer aussi rapidement », déclare le directeur de construction Handte.
Une fois la solution de manipulation raccordée à la machine spéciale, le circuit imprimé accède au dispositif de rainurage automatique après un retrait et un stockage réussi. De plus, LHMT propose également des dispositifs de manipulation pour le chargement et le déchargement d’étapes de fabrication complètes, par exemple pour des lignes de nettoyage ou de gravure. « Six circuits par minute est une cadence réaliste », explique Handte. Pendant ce temps, le système de manipulation doit encore déposer les couches protectrices entre les circuits imprimés de manière automatisée et séparément, ainsi que réagir de manière flexible au changement de cassette. « Cela signifie que l’automatisation doit être beaucoup plus rapide, afin de garantir un chargement continu de l’installation de traitement et d’effectuer toutes les tâches supplémentaires dans les temps ». Pendant ce temps, le processus de rainurage entièrement automatique du circuit imprimé a lieu, d’après un programme spécifique du client. Ce faisant, la machine peut créer des rainures longitudinales et transversales, selon le modèle. Suite au procédé, le circuit imprimé peut être retiré automatiquement sans intervention manuelle. Après la séparation et le contrôle final de qualité, les circuits imprimés sont prêts pour l’expédition et le montage.
« Nous sommes très satisfaits des solutions Schmalz », félicite Handte. « La qualité est au rendez-vous et, grâce à la ventouse NBR-ESD, nous sommes en mesure de proposer nos machines dans la version ESD-Safe », conclut le directeur de construction.
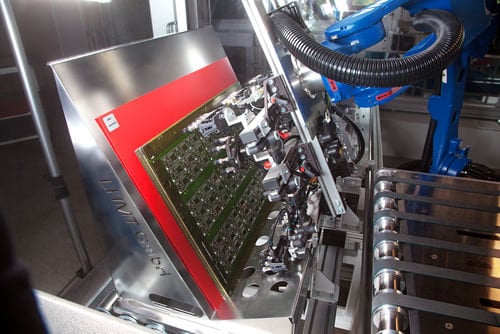
… et le places sur le convoyeur à rouleaux.
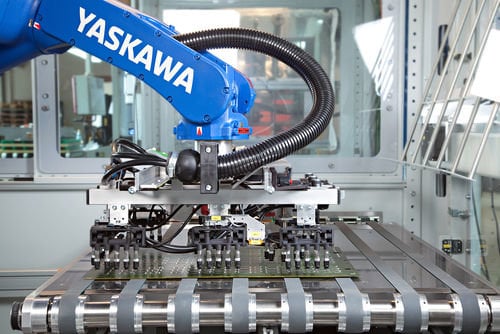
… et le places sur le convoyeur à rouleaux.
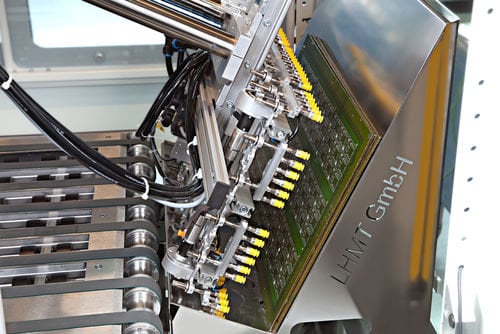
Au lieu d’un robot, un système à plusieurs axes peut également déposer les circuits imprimés sur le convoyeur à rouleaux en toute sécurité. Les ventouses NBR-ESD jaunes protègent de manière fiable contre des dommages dus à une décharge électrostatique.
www.schmalz.com