www.industrie-afrique-du-nord.com
04
'20
Written on Modified on
Une étape importante dans la fabrication hybride avec la technologie laser
KUKA travaille en collaboration avec l’institut de technologie laser Fraunhofer (ILT) et d’autres partenaires industriels sur un projet BMBF KIT (Karlsruhe) pour l’intégration d’une technologie LMD hybride dans la chaîne de production. Le procédé utilisé est le Laser Metal Deposition (LMD), également appelé impression 3D. Des robots KUKA forment la base de l’installation.
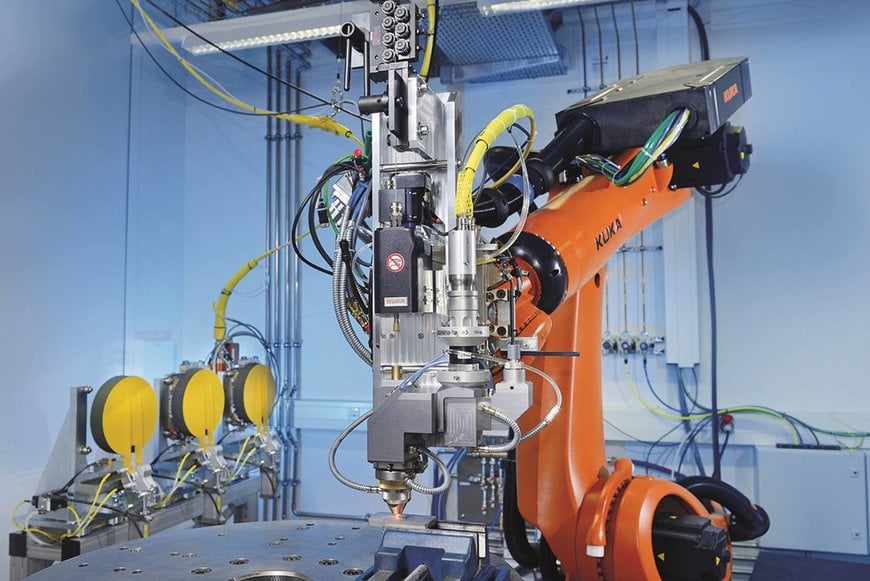
Les technologies conventionnelles et soustractives sont encore la norme dans les halls de fabrication. Les pièces coulées et moulées de formes complexes doivent alors souvent être usinées de façon complexe. Par exemple, lors de la fabrication de pièces de construction de haute performance et de pièces de construction légère dans le secteur de la construction aéronautique, jusqu’à 90 pour cent du matériel brut est retiré. Par contre, lors de la fabrication additive, les pièces sont fabriquées couche par couche. Cela permet d’économiser des ressources et d’éviter des chutes de production. De plus, la fabrication est extrêmement flexible.
La fabrication hybride additive : une alternative pratique
Une alternative pratique aux procédés courants est la fabrication hybride additive. Ce faisant, les pièces brutes sont fabriquées de façon conventionnelle, par forgeage ou coulage, par exemple. Les géométries supplémentaires sont cependant ajoutées de façon additive, ce qui permet d’individualiser les pièces avec le dépôt de matière par soudage laser LMD, dans le cadre du projet ProLMD promu par le ministère fédéral allemand de la formation et de la recherche (BMBF).
L’avantage par rapport à d’autres techniques additives est le rendement élevé. Il est ainsi par exemple possible de fabriquer avec efficience des pièces de structure d’avions localement renforcées ou des composants extrêmement fonctionnels pour turbines. Jusqu’à présent les coûts élevés et les conditions exigeantes pour l’usinage empêchaient souvent une utilisation complète de cette technologie.
"Les matériaux devant être protégés de l’oxydation lors du dépôt de matière par soudage laser et l’ensemble de l’installation se trouvant dans une atmosphère contrôlée, la taille des pièces à usiner est souvent limitée."
Günter Neumann, Head of KUKA Business Unit Laser Applications
Fabrication hybride de grandes pièces basée sur la technologie LMD KUKA
L’objectif du projet ProLMD est de développer une technique de processus et une ingénierie de systèmes pour l’utilisation de la technologie LMD lors de la fabrication de grandes pièces. Ce système doit être approprié aux techniques de production les plus modernes et être conforme aux exigences strictes en matière de sécurité dans des secteurs tels que l’aéronautique et l’aérospatiale.
L’ingénierie de systèmes standardisée basée sur des robots KUKA apporte des avantages financiers. Grâce à l’utilisation d’un système guidé par fibre, le robot reste pratiquement illimité dans son enveloppe d’évolution. Il est ainsi possible de réagir de façon flexible à la géométrie et à la taille de la pièce, même pour de petits lots.
Les avantages du dépôt de matière par soudage laser LMD : durée de fabrication réduite, faibles coûts
Les résultats de ProLMD seront intégrés dès les années à venir dans les systèmes de fabrication des partenaires du projet : MTU, Airbus et Daimler. « Nous prévoyons de poser un jalon lors de la réalisation industrielle du procédé de fabrication hybride », déclare Lars Ott, chef de projet ProLMD chez KUKA. Les experts partent du principe que cette technologie permettra de réduire la durée de fabrication de 50 pour cent et de baisser les coûts de 20 à 30 pour cent. De plus, l’implémentation permet de contribuer durablement à la gestion efficiente des ressources dans le domaine de la fabrication.
Avec ce projet, KUKA compte sur les nombreuses années d’expérience des experts du site d’Aix-la-Chapelle dans le domaine de la technologie laser basée sur des robots. Pour le projet, KUKA a conçu et réalisé deux lignes de production identiques pour la fabrication hybride additive. Ces lignes sont d’ores et déjà utilisées dans ses propres halls au site de Würselen près d’Aix-la-Chapelle ainsi qu’à l’institut Fraunhofer, situé à proximité. « À long terme, nous souhaitons préparer le procédé pour la fabrication en série », explique Günter Neumann.
www.kuka.com