www.industrie-afrique-du-nord.com
09
'20
Written on Modified on
Rockwell Automation, leader mondial de l'automatisation industrielle et de la transformation numérique, vous présente le retour d' expérience de Toyota
Le nouveau système économise annuellement 1 million de kWh.
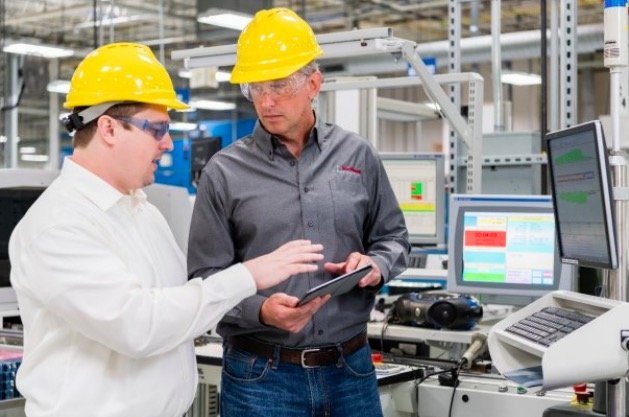
Cliquer ici pour accéder au témoignage complet :
Une usine Toyota réduit sa facture énergétique avec une nouvelle commande de compresseur d' air
Réduction des émissions
Vous avez déjà entendu parler des véhicules zéro émission. Mais quid de la production zéro émission ?
Telle est la vision de Toyota, un des plus grands constructeurs automobiles au monde. Son Toyota Environmental 2050 Challenge impose au groupe d' éliminer les émissions de CO2 de ses usines de production dans le monde d' ici 2050.
Pour atteindre ces objectifs ambitieux, Toyota adopte des mesures visant simultanément à réduire sa consommation énergétique et à adopter les énergies renouvelables. À l' instar de l' usine de Huntsville, dans l' Alabama (États-Unis), ces efforts aident Toyota à réduire son empreinte écologique et impactent aussi positivement ses résultats financiers.
Une facture énergétique excessive
L' usine de Huntsville fabrique les moteurs de modèles Toyota populaires tels que le Tacoma, le Tundra et le Highlander. Le personnel assure l' usinage des composants forgés sur d' autres sites et assemble les moteurs. Ceux-ci sont ensuite envoyés ailleurs pour y être intégrés aux véhicules.
Le système de compression d' air de l' usine est crucial pour le processus de production. Constitué principalement de cinq grands compresseurs centrifuges, le système fournit de l' air à cette usine de 93 000 mètres carré pour différents processus de machines, l' automatisation et le séchage des composants du moteur.
Les systèmes d' air comprimé (AC) sont, par nature, énergivores. Le système à Huntsville ne fait pas exception à la règle et représente 25 % de la facture énergétique annuelle de l' usine.
Avec les commandes existantes, le système était encore plus énergivore que ce qu' il aurait dû être. Les commandes vieillissantes démarraient lentement les compresseurs et ne leur permettaient pas de fonctionner ensemble en tant que système intégré. Par ailleurs, l' air comprimé stocké n' était pas suffisant pour les pics de consommation.
Du fait de ces limitations, les membres de l' équipe devaient maintenir les compresseurs en marche plus que nécessaire la majeure partie de la journée, afin de pouvoir faire face aux brefs pics de demande occasionnels.
« Nous avons besoin d' au minimum 81 PSI pour un fonctionnement sans interruption des machines », déclare Eddy Kiggen, un spécialiste des installations chez Toyota. « Mais comme le temps de démarrage des compresseurs était nettement trop long, nous devions maintenir 91 PSI, juste pour être sûrs que la pression d' AC ne passe pas sous la barre fatidique des 81 PSI. »
Le contrat d' électricité de l' usine était source de difficultés supplémentaires. Celui-ci facture plus cher l' énergie consommée pendant les heures de pointe. Lorsque les membres de l' équipe devaient démarrer un des grands compresseurs pendant cette période pour maintenir la capacité de l' usine, un seul démarrage de machine pouvait augmenter la facture d' électricité de 100 % du coût d' une journée.
Mises à niveau locales et à l'échelle de l'usine
Pour mieux maîtriser la facture énergétique et soutenir l' initiative Zéro CO2 pour 2050, Toyota Motor Manufacturing Alabama (TMMAL) a décidé de mettre à niveau les systèmes de commande de compresseur d' air de l' usine et s' est alors adressé à IZ Systems et Case Engineering, un partenaire constructeur de machines du programme PartnerNetwork de Rockwell Automation. Cette société a fourni une solution en deux volets incluant des commandes locales et au niveau de l' usine.
Localement, Case a migré les automates des cinq grands compresseurs vers sa solution AirLogix. Celle-ci repose sur la plate-forme de commande CompactLogix et inclut une interface opérateur PanelView Plus 7 fournissant au personnel des données de performances et de diagnostics pour chaque compresseur.
Au niveau de l' usine, Case a utilisé sa solution de partage de la charge AirMaster pour constituer un système de commande d' air maître. Cette solution repose sur la plate-forme ControlLogix et utilise le logiciel FactoryTalk View SE pour la collecte et la visualisation des données. Case a travaillé avec IZ Systems,qui a aussi installé un réservoir de 19 000 litres pour une pression d' AC décuplée de 500 PSI, afin de permettre au système de se réenclencher sans défaut.
Une soupape modulante fournit l' air pendant les pics de demande. Cet air stocké assure une transition progressive lorsqu' un compresseur centrifuge supplémentaire doit entrer en action pour couvrir les besoins en air de l' usine.
Coup d'accélérateur sur les économies
Les nouvelles commandes plus efficaces ont aidé l' usine de Huntsville à réduire sa consommation d' énergie annuelle de près de 1 million de kWh, sans compter les économies réalisées en évitant les démarrages pendant les heures de pointe.
Ainsi, le retour sur investissement des nouvelles commandes a été inférieur à l' objectif initial de deux ans.
« Nousavons réussi à abaisser notre valeur de consigne pour le système de 91 à 85 PSI », explique Kiggen. « C' est là où se situe la majorité des économies liées à ce projet. »
Les commandes locales mises à niveau contribuent à un fonctionnement plus efficace des compresseurs en augmentant la capacité de montée en charge de chacun d' entre eux. Le nouvel automate maître surveille la pression, et le débit d' air enclenche ou déclenche les compresseurs selon la demande. L' automate prélève de l' air comprimé du réservoir haute pression pendant le démarrage d' un compresseur, gère les pics de demande et assure la protection contre les problèmes potentiels.
« Grâce à la nouvelle configuration, nous avons toujours suffisamment de pression dans le réservoir pour les baisses ou défaillances de compresseur », déclare Kiggen. « Même si un compresseur subit une défaillance lorsque nous essayons de le démarrer, nous pouvons toujours en démarrer un autre et c' est transparent pour le personnel de l' atelier. » Le nouveau système fournit des informations de tendance pour surveiller la pression et le débit de l' air, la consommation d' énergie, ainsi que des données critiquesau niveau de chaque machine, notamment les vibrations. La disponibilité quasiment en temps réel de ces informations, qui constitue une nouveauté pour les membres de l' équipe, facilite l' analyse du système d' AC et le dépannage.
Les membres de l' équipe peuvent voir les informations en local sur chaque machine pendant la supervision normale des opérations. Toyota et Case Engineering peuvent les visualiser n' importe où grâce à l' accès à distance.
« Après l' électricité, l' air est notre service d' utilité le plus important et nous le surveillons donc de près », fait savoir Kiggen. « J' examine quotidiennement les données pour voir les performances du système et son efficacité. Je reçois une alerte en cas de problème, par exemple, une baisse de pression ou une chute du niveau du réservoir sous un certain seuil. Nous apprécions aussi d' avoir Case dans la boucle et de pouvoir les informer d' un problème, afin qu' ils puissent se connecter pour le résoudre immédiatement. »
Toyota cherche à reproduire ce projet ailleurs pour réaliser des économies d' énergie similaires et continuer à tendre vers l' objectif zéro émission de CO2.
« L' objectif zéro CO2 lors du processus de fabrication d' un véhicule est une mission monumentale », selon Kiggen. « Dès à présent, nous essayons d' économiserau maximum l' énergie avant de passer aux énergies renouvelables. Et, pour cette usine, ces mises à niveau des commandes est notre plus grande réussite depuis longtemps dans le domaine de l' énergie. »
Les résultats ci-dessus sont spécifiques à l' utilisation par Toyota des produits et services Rockwell Automation en association avec d' autres produits. Les résultats spécifiques peuvent différer pour d' autres clients.
www.rockwellautomation.com