www.industrie-afrique-du-nord.com
27
'19
Written on Modified on
Priorité à la sécurité
Pour permettre aux hommes et aux robots de travailler harmonieusement dans des zones d'usinage communes sans barrières de protection de séparation, il est nécessaire de respecter des exigences de sécurité strictes.
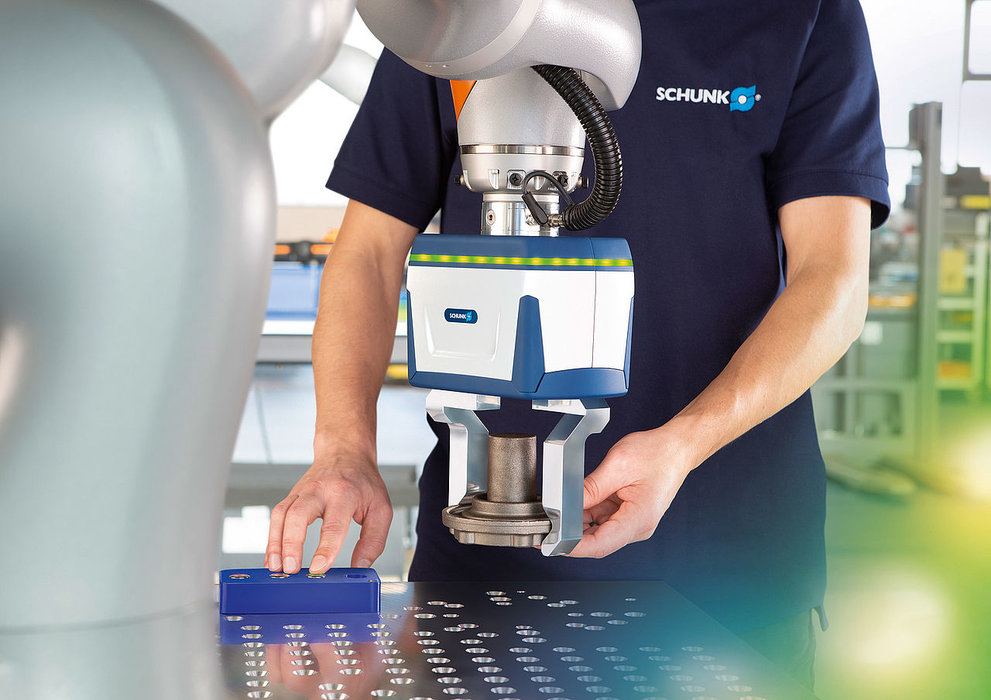
Ainsi, des aspects sécuritaires sont incorporés d'emblée dans les nouveaux systèmes de préhension.
Cela permet de raccourcir le processus de développement avec des composants standard, de réduire les coûts et d'accélérer les projets HRC spécifiques aux applications.
"La validation des applications HRC est un défi particulier," indique Prof. Dr. Markus Glück, directeur du département recherche et développement chez SCHUNK. Du point de vue de l'utilisateur, il régnait une certaine incertitude concernant la manière d'implémenter les exigences concernant la sécurité et la santé au travail dans les directives et les normes. "Pour une collaboration sûre entre les hommes et les robots, une connaissance approfondie de l'application robot est nécessaire, tout comme des connaissances spécialisées dans l'évaluation des risques," indique Glück.
Comme aucune application HRC ne ressemble à une autre, une évaluation individuelle des risques est chaque fois nécessaire. "La force, la vitesse, les courses de déplacement du robot et de la pièce à usiner, ainsi que du porte-pièce ne sont pas sans danger pour les ouvriers." Elles doivent être limitées grâce à des mesures de protection inhérentes ou, si nécessaire, grâce à des mesures supplémentaires de protection contre les risques, souligne Prof. Dr. Glück. "Notre objectif est de fournir aux fabricants de robots, intégrateurs et constructeurs de systèmes des composants matures, testés indépendamment pouvant être utilisés pour réaliser rapidement des scénarios collaboratifs et les certifier."
Série Co-act certifiée
Cela est illustré par la série Co-act EGP-C certifiée pour les applications collaboratives. La gamme de pinces comprend quatre tailles, est conçue pour des tâches de manutention simples et peut théoriquement être installée intuitivement sur tous les robots légers usuels, en tant que solution Plug & Work. "Avec plus de 400 installations de produits actuellement en place chez nos clients et partenaires, Co-act EGP-C a largement fait preuve de maturité," indique Markus Glück.
Pour des raisons de sécurité, la force de préhension agissant sur le doigt, dont la sécurité est inhérente à la conception, est limitée à 140 N.
Les modules de programmation haute performance et des plug-ins simplifient l'installation. Des doigts standardisés avec inserts interchangeables pour une utilisation universelle permettent aux nouveaux venus de se familiariser plus facilement avec l'univers des robots collaboratifs.
"Lorsque des êtres humains et des robots partagent une zone d'usinage, les angles doivent être arrondis afin que les hommes ne se coupent pas si la pince les érafle ou pèse activement contre les personnes," souligne Glück.
"De la même manière, il convient d'éviter le coincement des doigts et de la peau". Une visualisation claire de la situation de fonctionnement réelle grâce à des LED colorées favorise également la confiance.
Consultation pendant le développement du produit
Avec la Co-act EGL-C, SCHUNK franchit une étape supplémentaire. Grâce à cet outil puissant, il a été possible, pour la première fois, de produire une pince destinée aux applications collaboratives, dans lesquelles la force de préhension agissant sur le doigt est supérieure à la valeur de 140 N qui est considérée comme le seuil limite pour éviter les risques pour la santé.
Comme dans le cas de la pince pour petits composants collaborative SCHUNK Co-act EGP-C, SCHUNK a accordé une grande importance à l'Assurance sociale allemande des accidents du travail et maladies professionnelles (DGUV) lors du processus de création du produit pour la Co-act EGL-C.
Cette collaboration a facilité très tôt la communication ainsi que la surveillance efficace et le respect des normes. De plus, il a été possible d'acquérir de l'expérience sur la manière dont l'étude de sécurité et la certification peuvent être conçues afin d'être conviviales pour les utilisateurs, sans compromettre la qualité en faveur de la sécurité. "Le concept de sécurité de cette pince est très sophistiqué," explique Prof. Dr. Glück.
"Grâce à une consultation en temps opportun pendant le développement de la pince, nous avons été en mesure de garantir que, en ce qui concerne l'électronique de sécurité, la technologie de contrôle sûre et le concept de sécurité dans leur ensemble, une attention particulière a été apportée d'emblée au respect des normes et des réglementations légales en vigueur." déclare-t-il encore.
Préhension en trois phases
Un système d'intelligence de sécurité mis au point par SCHUNK et pour lequel un brevet a été déposé, divise le processus de préhension de la pince Co-act EGL-C en différentes phases individuelles.
Tant qu'il existe un risque de coincement des doigts et des mains, le système d'intelligence intégré limite la force de préhension à une force sans danger de 30 N.
Ce n'est que lorsque l'éloignement de la pièce est supérieur à 4 mm, lorsqu'il n'y a plus de danger de happement, que les doigts de pince s'approchent avec la force de préhension librement définissable de 450 N max.
Si le système détecte une flexibilité lors de cette phase de fermeture, par exemple parce qu'une pièce saisie est trop petite, et que l’opérateur souhaite la retirer manuellement, alors ce déplacement est stoppé automatiquement.
Il en va de même si les dimensions attendues de la pièce à usiner dépassent de 2 mm, lorsque par exemple, aucun élément n'est disponible. Dans la troisième phase, la pince détecte si la pièce est serrée correctement et serre le frein.
En conséquence, la pince SCHUNK EGL-C satisfait aux exigences pour une collaboration homme/robot sûre et garantit que les pièces serrées par friction peuvent peser jusqu'à 2,25 kg, et ne sont pas perdues dans des situations d'urgence et lors du freinage complet qui y est associé. Dans le cas du serrage enveloppant, des poids atteignant 8 kg sont possibles.
Un concept de sécurité modulaire comme objectif
En ce qui concerne la certification cependant, beaucoup reste encore à faire : "Pour que la HRC puisse être à la hauteur de son potentiel, une solution permettant aux intégrateurs et aux opérateurs de réaliser leurs processus collaboratifs au prix d'un effort raisonnable est nécessaire.
Y compris la validation de la santé et de la sécurité au travail," souligne Glück. Des concepts de sécurité modulaires proposés par SCHUNK et qui doivent concerner l'ensemble des pinces certifiées peuvent permettre aux utilisateurs de s'orienter et simplifier énormément la validation de la sécurité et la santé au travail dans des cas individuels.
"Si les utilisateurs pouvaient compter sur des composants certifiés lors de la conception d'un poste de travail homme/robot, l'introduction de la collaboration homme/robot dans la production quotidienne serait sensiblement plus rapide," explique Glück.
De son point de vue, le paysage des normes HRC continuera également d'évoluer. Par exemple, la norme ISO/TS 15066 doit être révisée au plus tard après quatre ans en tant que spécification technique.
"Pour cette raison, il est important que les fabricants de robots, les fournisseurs d'outils de préhension, les effecteurs et intégrateurs coopèrent activement avec les organismes de contrôle comme le DGUV en vue d'une amélioration des normes," déclare Glück.
"Les aspects sécuritaires doivent être prioritaires, et cela sans compromis. Simultanément, leur acceptation sera améliorée si les thèmes de la sécurité et de la simplification peuvent être harmonisés pendant l'installation et la certification."
Normes et directives pour la collaboration homme/robot
Les exigences légales concernant les scénarios collaboratifs sont initialement décrites dans la directive Machines européenne 2006/42/CE annexe 1 : le constructeur d'une machine ou son représentant autorisé doit garantir qu'une évaluation des risques est réalisée afin de déterminer les exigences de santé et de sécurité applicables pour la machine.
Pour l'évaluation des risques, l'environnement immédiat des applications doit être pris en compte dans l'analyse. Une protection efficace contre toutes les collisions dangereuses, les coincements des membres, des gants de travail ou le trébuchement des ouvriers est nécessaire.
Les références normatives relatives à la sécurité fonctionnelle des applications HRC sont des normes générales comme IEC 61508, IEC 62061 et ISO 13849-1 et 2.
En plus de ces normes, les normes ISO 10218-1 et -2 doivent également être prises en compte pour la sécurité des robots industriels.
La spécification technique ISO/TS 15066:2017-04 définit notamment les exigences d'utilisation fondamentales pour les robots dans les opérations collaboratives et les dispositifs robotiques.
Cette "norme HRC" décrit des commentaires d'utilisation pour quatre types de collaboration et explique de manière détaillée les principes de sécurité requis.
Elle contient également des spécifications détaillées sur les seuils de douleur à respecter pour les différentes zones du corps.
www.schunk.com