Des pignons pour prendre la relève de courroies
Les gravières baissent leurs coûts et réduisent leurs frais de maintenance grâce aux motoréducteurs. Pour de nombreuses carrières, unités de concassage et autres industries similaires, le système d’entraînement des convoyeurs à courroie est constitué d’un arbre et de courroies d’entraînement. C’était le cas encore récemment pour la gravière NorStone AS de Tau, située dans le sud-ouest de la Norvège. Dernièrement, NorStone, filiale de HeidelbergCement AG, a décidé de passer à un système d’entraînement par motoréducteurs. Cette option promettait un coût d’investissement inférieur pour une fiabilité opérationnelle supérieure, ainsi qu’une plus grande sécurité des process. Une baisse de la consommation d’énergie, grâce à des rendements améliorés, était également prévue.
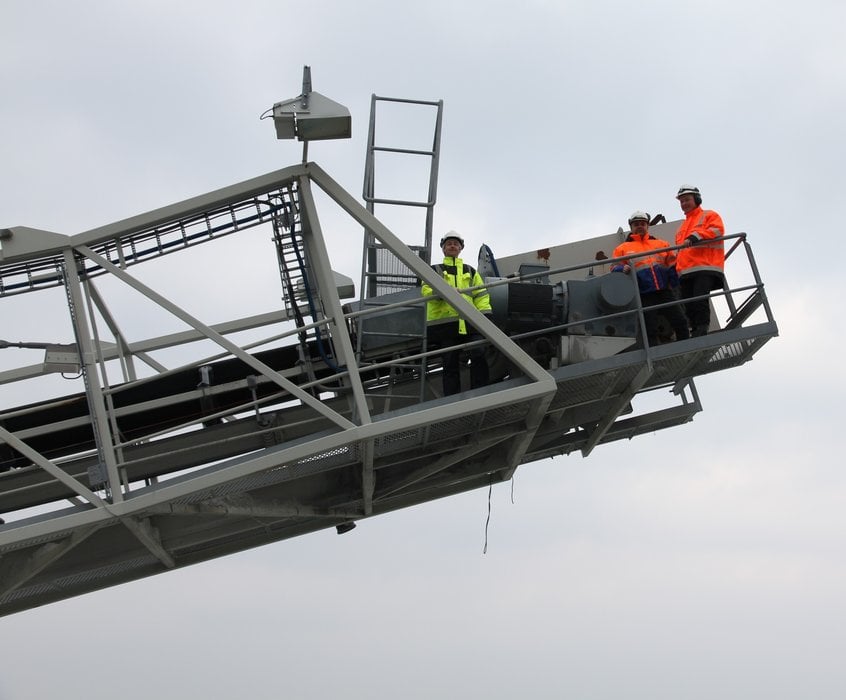
NorStone est le plus grand producteur norvégien de graviers et sables. L’entreprise fournit des granulats pour le béton et l’asphalte, du gravier pour la couverture de canalisations enterrées dans les régions côtières et d’autres produits spécifiques. NorStone produit annuellement sur ses sites plus de 6,6 millions de tonnes de graviers de différentes sortes et qualités. Les besoins sont vastes et, même avec sa capacité annuelle de production de 2,3 millions de tonnes de matériau, l’usine de Tau peine à satisfaire à la demande. De ce fait, il est particulièrement important que l’usine soit pleinement opérationnelle, avec un minimum d’arrêts non planifiés.
Avantages et fiabilité accrue des systèmes d’entraînements directs
Les motoréducteurs ne sont pas une nouveauté en soi dans les gravières. Les systèmes d’entraînements directs de ce type étaient déjà couramment utilisés dans les années quatre-vingt ; mais au cours des années suivantes, beaucoup d’usines sont passées aux entraînements par courroie, en raison de la disponibilité rapide des pièces détachées de ces entraînements, alors que dans le même temps, les fabricants et fournisseurs de motoréducteurs étaient incapables d’offrir des stocks de pièces de rechange avec la même disponibilité. « Nous avons découvert que le service et les pièces de rechange pour les motoréducteurs étaient maintenant rapidement disponibles. Nous détenons nous-mêmes un stock de pièces et pour le reste, nous faisons entièrement confiance à NORD Drivesystems comme fournisseur, explique Ivar Ullestad, Responsable Maintenance à Tau, pour justifier le retour à la solution antérieure. « Nous pouvons ainsi exploiter pleinement les avantages bien connus des solutions d’entraînement par motoréducteurs. En particulier, les entraînements directs se traduisent par une plus grande fiabilité, autrement dit moins d’immobilisations machine et moins de perte de temps de production. Autre aspect non négligeable, une moindre maintenance. Outre la baisse des coûts de maintenance, cette solution accroît la sécurité dans l’usine ».
Une moindre usure constatée par rapport aux solutions avec arbres et courroies
Les conditions de travail constituent ici un facteur important à prendre en compte. « Il ne faut pas perdre de vue que nous travaillons en extérieur, 365 jours par an. La plupart des des convoyeurs à bande sont situés à l’air libre et sans protection contre les intempéries. En raison des conditions climatiques rigoureuses dans l’ouest de la Norvège, avec vent, pluie, neige et giboulées, ainsi que des poussières et de l’environnement assez désagréable sur site, nous nous efforçons de réduire au minimum les temps de maintenance et réparation pour notre équipe d’entretien ». L’usine de Tau fonctionne en équipes 24 heures sur 24. Les 168 heures de production incluent 16 heures d’opérations de maintenance programmées. L’usine ne ferme qu’au moment des vacances d’hiver. Au cours de cette période, les tâches annuelles d’inspections et révisions de maintenance se déroulent sur deux à trois semaines. Les entraînements directs ont contribué à une nette amélioration de la fiabilité, de l’ordre de 4,5%, sur les trois dernières années. « Cette tendance nous ravit. Grâce au passage d’un système d’entraînements par arbre et courroie à un sytème d’entraînements directs par motoréducteurs de chez NORD Drivesystems, nous éminons tout d’abord le problème de l’usure des courroies, qui est considérable. De plus, ni l’eau ni les poussières ne peuvent pénétrer dans le système d’entraînement. Autrement dit, le choix de motoréducteurs compactes et robustes présente des avantages évidents et s’est avéré très judicieux », explique Per Thu, Responsable Production de l’usine NorStone.
Les systèmes d’entraînements directs apportent davantage qu’un supplément de fiabilité et qu’une réduction des dépenses financières et de personnel liées aux opérations de maintenance. Les coûts d’investissement relatifs à l’acquisition de ces motoréducteurs s’avèrent également inférieurs. Le remplacement d’un ensemble complet traditionnel, comprenant un réducteur à arbre avec les poulies, les courroies, un abri, un carter de protection courroie et le moteur électrique se révèle être finalement plus onéreux que l’achat d’un motoréducteur comparable. Comme une série de remplacements périodiques de réducteurs était à l’étude, la mutation complète des entraînements à arbres et courroies constituait un choix logique dans l’esprit d’Ivar Ullestad. Il s’efforce actuellement de standardiser les systèmes d’entraînement. « Avec une réduction graduelle des systèmes d’entraînement pour convoyeurs à bande, nous standardisons certains aspects comme la dimension du moteur et du bout d’arbre, le diamètre du tambour, afin de limiter la variété et par conséquent de réduire la maintenance, la gestion de stock et le service. Nous développons également des solutions de dépannage, ce qui implique notamment d’avoir chez nous des pièces en stock », selon le Responsable Maintenance.
A propos de NorStone AS
La société norvégienne NorStone AS (http://www.norstone.no) est filiale à 100% d’HeidelbergCement AG, l’un des plus grands producteurs mondiaux de matériaux de construction tels que ciment, sable et gravier. L’usine de Tau gère, mixe, contrôle et fournit des granulats de haute qualité pour béton et asphalte ainsi que des matériaux de base à la qualité constante et de différents tailles. Les matériaux sont concassés et réduits à des dimensions différentes, puis mixés de façon à obtenir des courbes de distribution granulométrique des particules répondant aux besoins spécifiques des clients. Dans ce processus, ce sont les laboratoires en interne qui assurent les contrôles de conformité aux normes européennes. NorStone fournit entre autres le ballast pour le secteur des voies ferroviaires, les matériaux de construction des routes et des matériaux pour les régions côtières. L’usine de Tau produit chaque année 2,3 tonnes de matériau, dont environ 75% sont destinés à l’exportation.
Figure 1: usine NorStone
Figures 2 & 3 : L’usine NorStone avait jusque là l’habitude d’utiliser des convoyeurs d’excavation comme celui que l’on peut voir à gauche, avec un arbre et une courroie d’entraînement raccordés à deux moteurs de 55 kW. Par contre, les deux convoyeurs rénovés sont équipées de motoréducteurs, avec par exemple un réducteur SK 9086 couplé à un moteur électrique de 90 kW que l’on peut voir à droite.
Figure 4 : L’usine de Tau située en bord de mer possède son propre quai, qui reçoit 700 à 900 navires par an. Le convoyeur de charge est muni d’un moteur électrique 37 kW avec un réducteur SK 9082. 1-225S/4.
Figure 5 : Ambiances sévères et particulièrement poussiéreuses : entraînement de 15 kW avec motoréducteur SK 9052.1-160L/4 installé en-dessous des concasseurs sur la courroie 10.