www.industrie-afrique-du-nord.com
31
'20
Written on Modified on
Fabrication additive : un potentiel de disruption exceptionnel
L'engouement général vis-à-vis de l'impression 3D ou de la fabrication additive est de bon augure pour l'avenir de la planète.
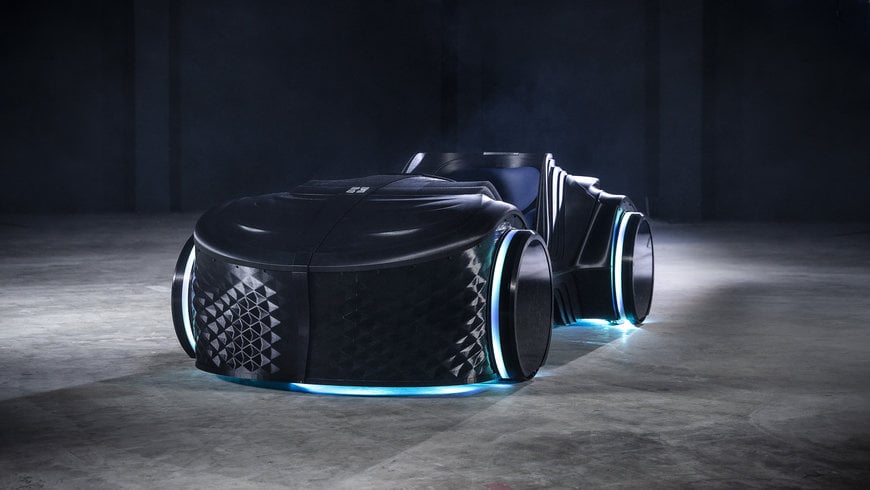
L'impression 3D ou la fabrication additive est considérée comme l'une des technologies les plus disruptives de l'ère moderne, la clé de l'avenir de la production. Inventée au début des années 1980, elle suscite un engouement considérable depuis quelques années grâce à l'évolution et à la convergence rapides de plusieurs technologies de l'ère numérique, qui l'ont rendue plus accessibles aux professionnels et aux amateurs. Autrefois chasse gardée du prototypage rapide, la fabrication additive ou impression 3D est désormais perçue comme la solution idéale pour fabriquer des produits ou pièces en tout lieu et à tout moment. À la différence de la fabrication classique ou soustractive, qui fait appel à des procédés comme le fraisage, la découpe ou le meulage pour éliminer de la matière, la fabrication additive implique l'ajout de matière par couches successives pour former un objet ou une pièce à l'aide d'un logiciel de CAO ou d'un scanner d'objets 3D. De nombreux procédés, technologies et matériaux sont employés en fabrication additive. Les matériaux vont des thermoplastiques aux métaux et des céramiques aux produits biochimiques, ces derniers étant souvent utilisés dans les implants médicaux.
L'un des principaux avantages de la fabrication additive est le fait qu'elle facilite la production de pièces personnalisées à la demande à un prix relativement abordable, qu'il s'agisse de remplacer une roue d'une petite voiture ou celles d'un rover envoyé sur Mars. Surtout, le procédé permet aussi d'utiliser des designs très sophistiqués à la géométrie complexe, qui réduisent le poids tout en renforçant la solidité de pièces difficiles et/ou coûteuses à fabriquer via les méthodes traditionnelles. L'exemple de l'injecteur de carburant conçu et fabriqué par GE pour le moteur LEAP est bien connu. Auparavant assemblée à partir de 20 éléments, cette pièce complexe de la taille d'une noix est devenue une merveille d'ingénierie, produite d'un seul tenant grâce à l'impression 3D. Elle est aussi 25 % plus légère, cinq fois plus durable et 30 % plus économique que la version produite de manière classique. Comme le soutient Janne Kyttanen, visionnaire de la 3D et inventeur de 3DTI, la toute première technologie de fabrication intégrant l'impression 3D pour la personnalisation de masse, les applications de fabrication additive ne sont limitées que par la créativité.
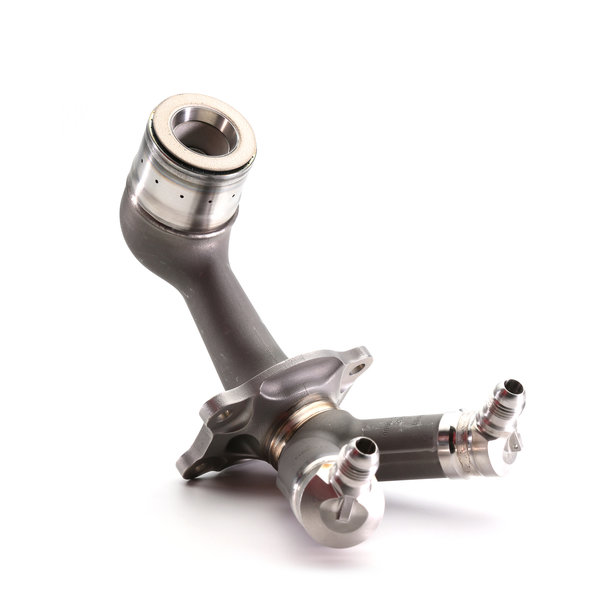
Injecteur de carburant fabriqué par GE pour le moteur LEAP
S'il présente de nombreux avantages, le procédé n'est toutefois pas exempt d'inconvénients, le principal étant le coût, tant en termes d'investissement initial que de frais d'exploitation. Ces derniers sont dus au prix élevé des matériaux qui, dans la plupart des cas, sont fournis par les fabricants du matériel et liés à des contrats OEM. Cette technologie exclut aussi la production de masse, en particulier des pièces de grandes dimensions, leurs procédés de fabrication conventionnels demeurant clairement plus économiques. En revanche, pour les besoins spéciaux, la fabrication additive présente des avantages considérables, indépendamment de la taille et des volumes. La fixation de siège fabriquée par General Motors à l'aide du logiciel de conception générative d'Autodesk illustre ce cas de figure à merveille. Cette pièce automobile standard permet de fixer les ceintures de sécurité au siège et ce dernier au sol. L'ancienne version constituée de huit éléments soudés a laissé place à une élégante pièce d'ancrage en acier inoxydable fabriquée par impression 3D. Cette version moderne est 40 % plus légère et 20 % plus solide. En outre, sa production est plus économique, car elle réduit le nombre de fournisseurs et élimine le soudage. Il est donc peu étonnant que tous les constructeurs automobiles aient investi dans des systèmes de fabrication additive pour optimiser la conception des véhicules et réduire les coûts. En moyenne, une voiture comporte environ 30 000 pièces. S'il est impossible de toutes les fabriquer par impression 3D, certaines comme la fixation de siège évoquée ci-dessus bénéficient clairement de cette avancée technologique.
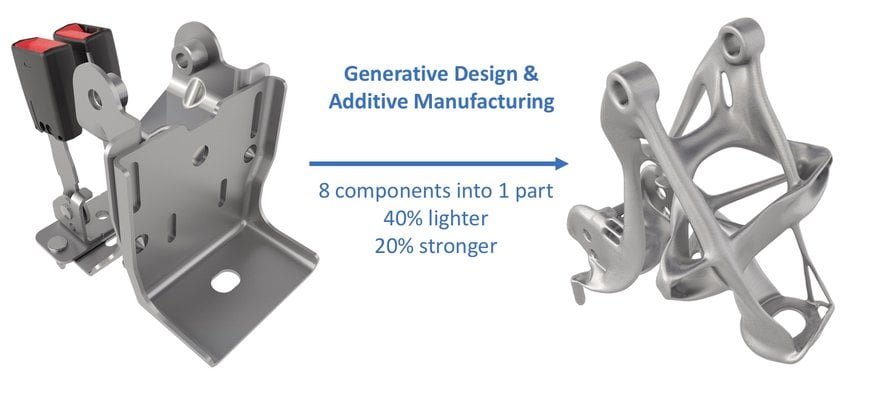
Fixation de siège produite par General Motors
L'innovation à l'honneur à Formnext
À Francfort en novembre dernier, le salon Formnext 2019, plus grand événement professionnel en Europe pour la fabrication additive et la nouvelle génération de solutions de production intelligente, a rassemblé des entreprises de renom comme 3D Systems, Addup, BigRep, DMG Mori, EOS, Formlabs, GE Additive, HP, Markforged, Renishaw, Siemens, Stratasys et Voxeljet. Elles y ont présenté plusieurs technologies de fabrication novatrices et efficaces pouvant être utilisées dans un cadre industriel – logiciels, matériel et services –, sans compter une multitude d'annonces de rapprochements et d'alliances technologiques.
Augmentation des volumes…
GE Additive, acteur majeur et pionnier du secteur de la technologie additive, a dévoilé de nombreux produits, notamment l'Arcam EBM Spectra L, une imprimante 3D métal qui répond à l'augmentation de la demande en équipements de ce type, en particulier de la part du secteur aéronautique. Ce nouveau modèle offre un volume de fabrication supérieur, une vitesse accrue, une architecture système intégrée et des fonctions d'analyse de l'état de la machine et d'automatisation. La Spectra L a été conçue pour renforcer la productivité et réduire de 10 % le coût par pièce, grâce à un volume de fabrication près de deux fois supérieur à celui de l'Arcam EBM Spectra H. Son faisceau d'une puissance de 4,5 kW réduit de 20 % le temps de fabrication par rapport à l'Arcam EBM Q20plus. L'entreprise a également présenté l'imprimante métal Concept Laser M2 Series 5 qui répond aux exigences de qualité et d'homogénéité des pièces des clients, surtout ceux des secteurs fortement réglementés comme l'aéronautique et la médecine qui, avec l'automobile, sont les trois principaux utilisateurs des technologies de fabrication additive.
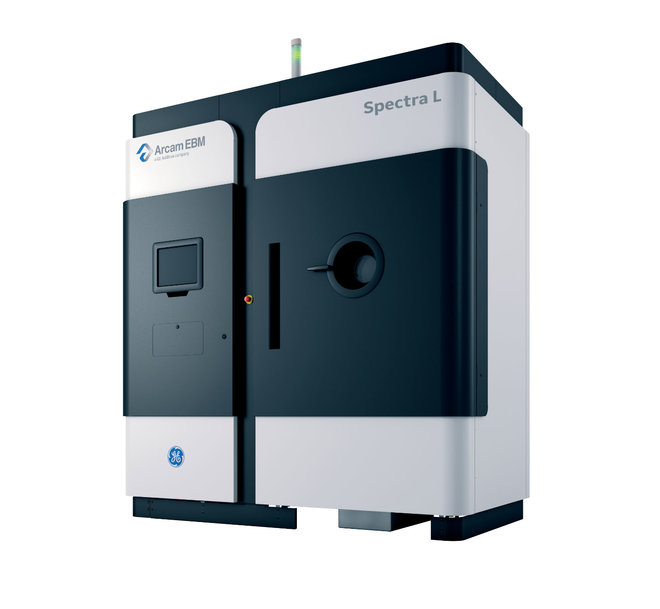
Arcam EBM Spectra L de GE Additive
… pour des pièces de plus en plus complexes…
BigRep, l'entreprise qui fabrique les plus grandes imprimantes 3D de production en série au monde, a présenté un concept de robot taxi électrique autonome, le LOCI, entièrement fabriqué par impression 3D. Spécialement conçu comme « solution de transport pour le dernier kilomètre » dans les environnements urbains, ce prototype est destiné aux aéroports et aux gares ferroviaires, aux transports en commun et aux autres trajets courts, ou encore aux livraisons locales. Développé via la modélisation paramétrique, le LOCI tire pleinement parti du potentiel de la fabrication additive, notamment de son extrême souplesse. La conception de ce robot taxi peut facilement être personnalisée pour un environnement ou une application donnée, en adaptant les capacités de manutention, les matériaux, les propriétés structurelles, les pneus selon le type de terrain et l'identité visuelle de la marque, ainsi qu'en intégrant ou non des panneaux solaires. À Formnext, l'entreprise a présenté trois versions de son concept : le modèle de Berlin destiné au transport individuel sur un campus étudiant, celui de San Francisco au corps étroit pour les trajets urbains quotidiens et celui de Dubaï, une luxueuse navette d'aéroport équipée de panneaux solaires et de pneus renforcés parfaitement adaptés au climat désertique, avec un espace spécialement aménagé pour les bagages.
… et de très grande taille
Toujours sur le même salon, BigRep a lancé NEXT AGV. Développé conjointement avec Bosch Rexroth, ce véhicule autoguidé est destiné aux usines intelligentes. Étroitement intégré aux sites de production agiles, ce véhicule fabriqué par impression 3D est alimenté par un module d'énergie inductif lui-même alimenté par le réseau électrique. Doté d'une capacité de charge maximale de 250 kilos, il peut servir de transporteur logistique automatisé. Des outils et dispositifs supplémentaires, par exemple des robots, peuvent être fixés sur la plateforme. Grâce à des roues spéciales fabriquées par impression 3D à partir de deux matériaux différents, la plateforme peut effectuer des mouvements latéraux.
Des pièces spéciales, pour les industries de pointe
3D Systems, entreprise cofondée en 1983 par Chuck Hull, l'inventeur de l'impression 3D, a présenté à Formnext 2019 quatre solutions de production spécialement conçues pour le secteur médical, l'aéronautique et l'automobile. L'entreprise est idéalement placée pour proposer des solutions sur mesure en réponse aux besoins des clients par le biais de matériel, de logiciels, de matériaux et de services professionnels, en intégrant la fabrication additive aux environnements de production traditionnels. Dans le cadre d'un partenariat stratégique avec GF Machining Solutions, 3D Systems allie ses innovations et son expérience de la fabrication additive au savoir-faire de GF Machining Solutions en matière d'usinage de précision. Les fabricants peuvent ainsi associer facilement les technologies additives et soustractives pour produire plus efficacement des pièces métalliques complexes selon des tolérances strictes et réduire le coût total d'exploitation. Parmi les solutions présentées sur le stand commun aux deux entreprises, les visiteurs ont pu découvrir un procédé de production permettant de créer un support aéronautique en sept étapes intégrant des technologies additives, des technologies métal traditionnelles et des solutions logicielles innovantes pour obtenir des pièces de grande qualité et reproductibles à un coût unitaire optimisé.
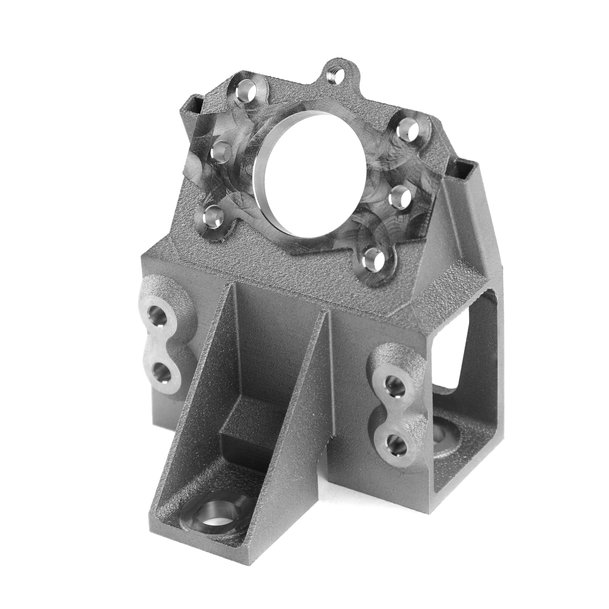
Support aéronautique hybride développé par 3D Systems
Métaux et polymères
EOS, premier fournisseur technologique mondial dans le domaine de l'impression 3D industrielle de métaux et polymères, a présenté pour la première fois sa technologie Fine Detail Resolution (FDR) pour le traitement des polymères. EOS est le premier fabricant à mettre au point une solution pour l'impression 3D industrielle sur lit de poudre à l'aide d'un laser CO. Cette solution permet de produire des composants très délicats, mais robustes, avec des surfaces aux résolutions très fines et des parois très minces de seulement 0,22 mm. Elle ouvrira la voie à de nouvelles applications de production en série, et permettra de proposer un large choix de technologies d'impression 3D EOS pour le traitement des polymères. La technologie FDR réunit le meilleur des deux mondes : la résolution détaillée de la stéréolithographie (SLA) et la durabilité et la qualité du frittage laser sélectif (SLS). Elle ouvre la voie à de nouvelles applications dans le domaine de la fabrication additive de polymères : unités de filtration, canaux de fluides, connecteurs et autres composants électroniques, mais aussi produits de grande consommation comme les lunettes.
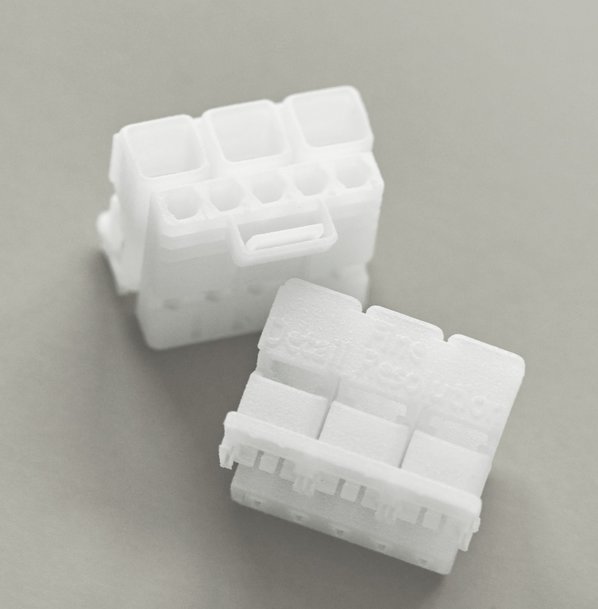
Connecteurs fabriqués par impression 3D via la technologie FDR d'EOS
Essentium, Inc., a annoncé l'extension de sa plateforme de fabrication additive avec l'introduction de matériaux haute température (HT) et de nouveaux modèles de sa plateforme d'impression par extrusion à grande vitesse (HSE). La température de buse de la nouvelle HSE 180•S HT peut atteindre 550 °C et utilise une grande diversité de matériaux pour produire des pièces capables de résister à des températures de 180 °C. En proposant des capacités de fabrication additive à haute température sur le marché sans transiger sur la vitesse, la solidité, l'évolutivité ou les coûts, Essentium a accéléré le potentiel de la fabrication additive à l'échelle industrielle, et tenu son engagement de créer un écosystème ouvert et mondial offrant aux clients la maîtrise de leurs innovations. L'entreprise a également introduit quatre nouveaux matériaux, notamment le PEEK, le nylon haute température (HTN), le HTN-CF25 et le HTN-Z (résistant aux décharges électrostatiques), conçus pour offrir une grande résistance à la chaleur, aux produits chimiques et à la fatigue ainsi qu'une grande robustesse pour les applications industrielles. La marque a également annoncé l'intégration du logiciel d'impression 3D Materialise Magics Essentials avec son imprimante 3D HSE. Cette intégration permettra d'obtenir un workflow de bout en bout avec toutes les fonctionnalités nécessaires à la fabrication 3D à l'échelle industrielle pour transformer la production des usines.
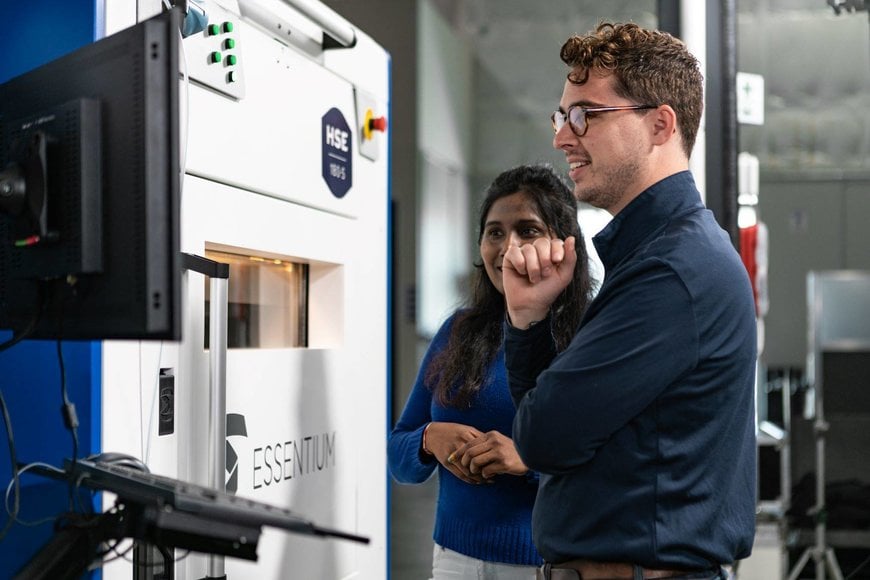
Nouvelle HSE 180•S HT d'Essentium
Mesure acoustique et logiciel au service de la quatité
Autre acteur de premier plan, Renishaw a lancé le logiciel de surveillance acoustique InfiniAM Sonic pour compléter sa suite InfiniAM d'outils de supervision des procédés de fabrication additive. InfiniAM Sonic permet aux ingénieurs de détecter les événements acoustiques dans la chambre de fabrication et de convertir ces données en informations utiles sur la qualité de fabrication. Ce logiciel est le premier en son genre au sein du secteur de la fabrication additive. Le package InfiniAM Sonic est installé au sein du système RenAM 500Q en option et inclut quatre capteurs acoustiques pour détecter les vibrations de fabrication. Le système RenAM 500Q dispose de quatre lasers 500 W haute puissance capables de quadrupler la vitesse de fabrication par rapport aux systèmes classiques à un seul laser. Le RenAM 500Q offre un rendement de fabrication réellement plus élevé, car ses lasers sont chacun capables d'atteindre tous les points de la plaque de base. Les interactions entre les lasers peuvent ainsi être gérées efficacement, pour éviter que la qualité ne soit affectée par plusieurs interactions de laser en cours de traitement. Renishaw collabore également avec Sandvik Additive Manufacturing pour qualifier de nouveaux matériaux de fabrication additive pour les applications de production. Il s'agit d'une large gamme de poudres métalliques, notamment de nouvelles compositions d'alliages optimisées pour le procédé de fusion laser sur lit de poudre (LPBF) et qui offrent des propriétés matérielles supérieures.
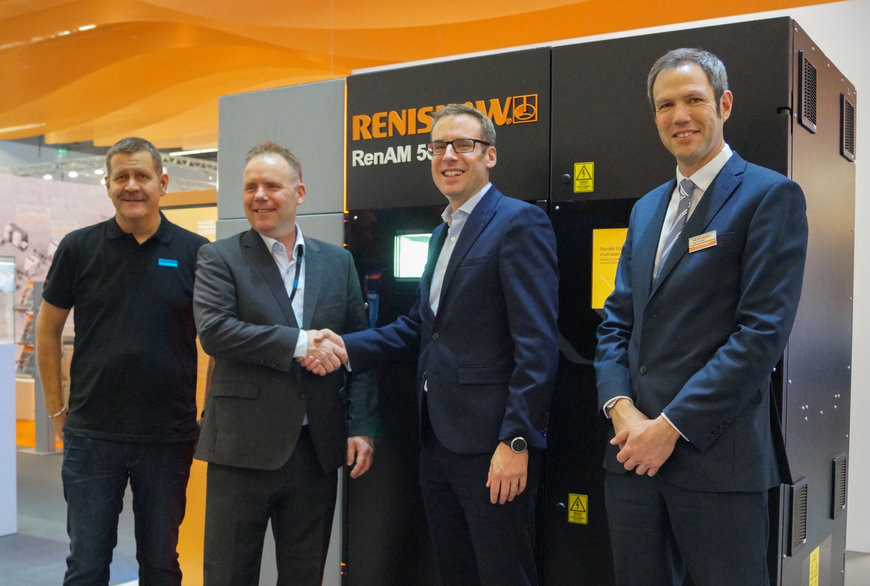
L'équipe de Renishaw au salon Formnext 2019
Sans oublier la sécurité
Si l'impression 3D est capable de répliquer un objet uniquement en le numérisant et en l'imprimant, le procédé crée un risque de sécurité. Une clé peut par exemple être facilement photographiée ou scannée, puis une copie imprimée. La société suisse UrbanAlps AG a conçu et produit une solution qui devrait mettre un terme au problème. Fabriquée par impression 3D, la Stealth Key, une clé qui n'a rien d'ordinaire, a remporté le premier prix du purmundus challenge à Formnext 2019. Grâce à la technologie furtive, UrbanAlps a créé une clé physique dont le codage (ou taillage) unique est dissimulé sous des rebords étroits. Cette clé purement mécanique ne pouvant être scannée, elle offre une sécurité maximale et fonctionne indépendamment des systèmes numériques, neutralisant ainsi la menace de manière efficace à l'aide la même technologie.
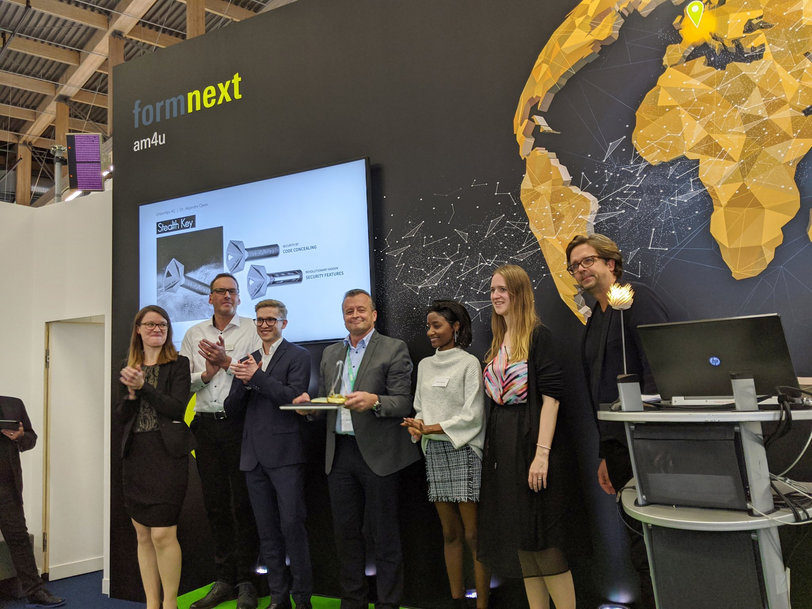
Les exemples évoqués ci-dessus ne sont que quelques-unes des innovations présentées par les 852 exposants (contre 632 en 2018) à Formnext 2019 pour illustrer l'ensemble de la chaîne de valeur de la fabrication additive. L'événement a attiré 34 000 visiteurs provenant de 99 pays, preuve que la communauté de la fabrication additive ne cesse de s'agrandir.
Développement durable : une solution pour l'avenir
L'inquiétude croissante vis-à-vis de la dégradation de l'environnement et des changements climatiques ont fini par attirer l'attention des gouvernements, et autres décideurs politiques et industriels du monde entier. Le est le nouveau leitmotiv et la carboneutralité le nouvel objectif, alors que plus de 60 pays ont annoncé à l'ONU vouloir parvenir à zéro émission nette de CO2 d'ici 2050. À la mi-2019, le fournisseur mondial de technologies et services Bosch a déclaré que l'entreprise atteindrait la neutralité carbone en 2020. Bon nombre d'entreprises mettent actuellement en place leur propre calendrier pour atteindre cet objectif.
Alors que le monde s'engage en faveur du développement durable, l'impression 3D aura un rôle important à jouer, en particulier dans le domaine de la mobilité. L'allègement de toutes les formes de transport terrestre, aérien et naval est l'une des grandes priorités des fabricants. Les logiciels de conception générative constituent la technologie permettant d'y parvenir. Quand General Motors a réinventé la fixation de siège à l'aide de la technologie de conception générative d'Autodesk dans Fusion 360, le logiciel a proposé plus de 150 designs alternatifs, le plus optimal ayant finalement été retenu. Autodesk et BMW travaillent actuellement à la création d'un nouveau genre de véhicule, plus léger, rapide, économique, fiable et facile à produire, grâce aux technologies de conception générative et aux méthodes de fabrication additive.
Cette association présente un potentiel d'applications bien plus vaste que le seul domaine de la mobilité. Elle pourrait s'avérer précieuse dans de nombreux domaines reposant sur les matériaux – architecture et construction, bâtiments et usines, machines industrielles, biens de consommation –, avec à la clé des gains de productivité et des économies d'énergie contribuant à réduire l'empreinte carbone. S'agissant des matériaux, l'impression 3D connaît également des avancées rapides dans le domaine alimentaire, en particulier le segment de la confiserie, en permettant de réaliser des modèles de gâteaux et chocolats complexes et attrayants.
Avec son évolution rapide et son accessibilité croissante à mesure que le matériel et les consommables deviennent plus abordables, l'impression 3D ou la fabrication additive va encore gagner en popularité dans les années à venir. Des chaussures aux engins spatiaux, cette technologie est en train de révolutionner les méthodes de conception et de fabrication, et s'impose de plus en plus comme la clé d'un avenir durable.
••• Bruno FORGUE