www.industrie-afrique-du-nord.com
08
'19
Written on Modified on
Automatismes pneumatiques : polyvalence, attractivité, réduction des coûts et… ouverture vers le 4.0
La sécurité, les faibles coûts d’exploitation, la simplicité de déploiement et la rentabilité sont quelques-unes des principales raisons pour lesquelles de nombreux sites de production dans le monde entier privilégient l’automatisation pneumatique. Il faut dire, que les constructeurs n’ont jamais ménagé leurs efforts pour améliorer continument cette technologie, allant maintenant jusqu’à contribuer largement à la migration des automatismes vers l’Industrie 4.0.
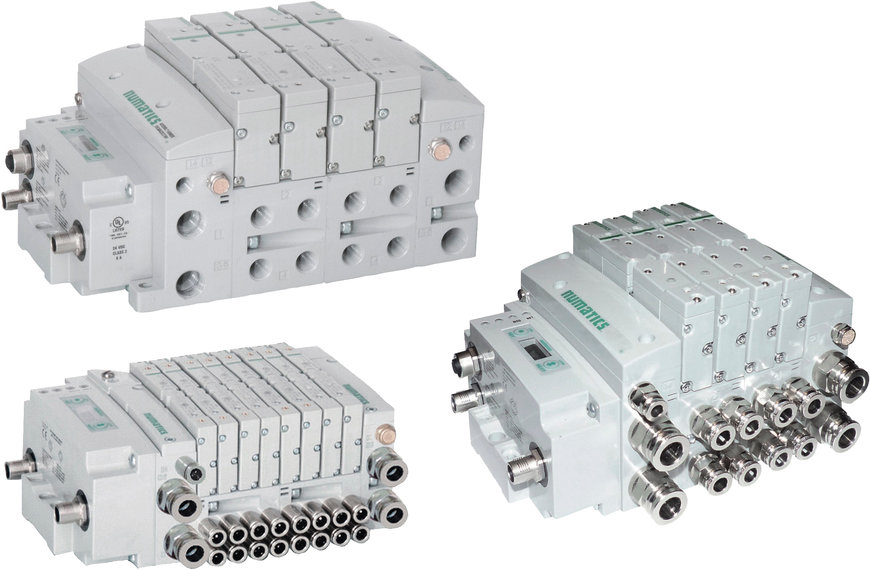
La technologie pneumatique est de longue date au cœur des automatismes. Simple et accessible, elle présente de nombreux avantages. Ils sont tout d’abord dus aux caractéristiques de sa source d’énergie : l’air comprimé. Et puis, les composants pneumatiques sont puissants, robustes, naturellement protégés contre l’humidité, les vibrations, la chaleur et les interférences électromagnétiques, utilisables sans difficulté ni surcoût dans les zones à risque d’explosion (pas de risque d’étincelle).
Ils n’ont pas manqué les évolutions et révolutions internes au monde des automatismes. Suivant l’arrivée des bus de terrain, ils sont devenus communiquant ; ils participent maintenant pleinement à la distribution de l’intelligence sur le terrain et contribuent largement à l’industrie 4.0 et ses bénéfices pour les responsables de production.
Cette tendance est confirmée par Leonardo Brand, superviseur en charge de l’ingénierie chez ASCO-EMERSON : « La pneumatique est un outil extrêmement attractif pour la majorité des entreprises en raison de sa polyvalence et son faible coût. » Dans le monde, les industries de la chimie et pétrochimie, de l’automobile et autres secteurs manufacturiers, ou encore de la manutention, l’utilisent depuis longtemps ; elle est tout aussi répandue dans une grande variété d’autres industries : métallurgie, exploitations minières, papeterie, emballage, conditionnement, etc.
En matière d’automatisation pneumatique, Leonardo Brand met l’accent sur le marché des procédés : « Notre savoir-faire dans ce domaine, qui couvre des secteurs d’activité comme la chimie, l’industrie minière, la papeterie, la médecine et les analyses, la production d’énergie et le raffinage du pétrole, nous permet de proposer des solutions d’automatisation pneumatique exclusives. »
Pour M. Brand, l’industrie minière fait partie des principaux segments, surtout en ce qui concerne les procédés de récupération, de traitement et de contrôle des eaux usées. Dans le cadre de ceux-ci, les solutions pneumatiques comme les vérins, les distributeurs et les kits de préparation pour la qualité de l’air sont très répandus.
La fabrication des pneumatiques (pour les marchés de l’automobile) est un autre domaine majeur, en particulier les systèmes de commande pour les autoclaves, dans lequel les solutions pneumatiques les plus fréquentes incluent les distributeurs intelligents et les régulateurs de pression électroniques.
L’industrie de la chimie est un secteur historique de l’utilisation des automatismes pneumatiques (pour le contrôle des vannes – sans risques d’étincelle électrique pouvant provoquer une explosion). Les solutions pneumatiques telles que les distributeurs intelligents et les kits de préparation pour la qualité de l’air sont souvent déployées dans les systèmes de contrôle des fluides.
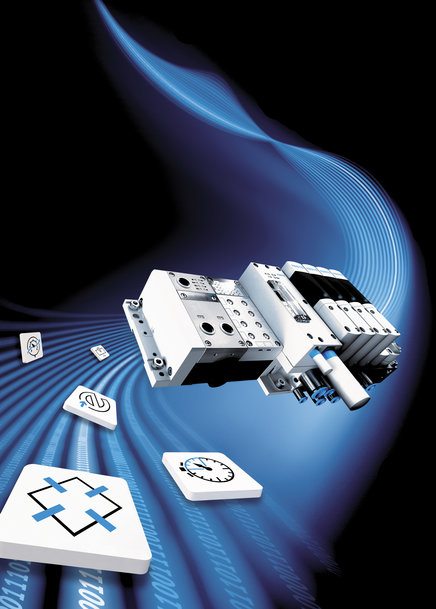
Osvaldo Tomio Sato, chef de produit chez FESTO, explique que comme il s’agit d’un simple système de contrôle de la force et du mouvement, la pneumatique peut être appliqué à de nombreux segments industriels : « Les applications sont très diverses. Elles incluent le déplacement d’une unité dans un convoyeur de conditionnement, le positionnement de pièces dans les machines-outils, le transport de pièces dans l’industrie automobile, les supports dans le secteur de l’électronique, l’ouverture et la fermeture des distributeurs dans l’industrie pharmaceutique, les mécanismes des portes de bus et trains ou encore les dispositifs de tri des céréales dans le secteur agroalimentaire. »
M. Sato indique que FESTO travaille sur différents marchés pour généraliser l’adoption de l’automatisation pneumatique, notamment certaines niches du secteur agroalimentaire comme la boucherie et la réfrigération, la confiserie, les chocolats ou encore les produits laitiers.
« Cette polyvalence s’explique principalement par le fait que l’automatisation pneumatique peut facilement être déployée dans les applications de transport, de manutention, de conditionnement ou d’inspection des produits. En outre, cette technologie peut contribuer au renforcement de la productivité et de l’hygiène. Par leur conception et le choix des matériaux qui les constituent, les composants pneumatiques, notamment les canalisations, les raccords, les actionneurs et les distributeurs, répondent aux critères hygiéniques les plus strictes, en conformité avec les attentes des organismes publics de contrôle. »
La pneumatique et l’industrie 4.0
Pour M. Brand, les principaux avantages de l’automatisation sont la flexibilité, la simplicité de développement et le coût.
« Toutefois, dans certains procédés, l’installation d’un système pneumatique efficace peut s’avérer difficile, par exemple lorsque les points d’accès et de distribution de l’air n’ont pas été pris en compte dès la conception du site », explique-t-il. « Dans ces cas, une solution électrique est préférable à la création d’un environnement idéal pour la pneumatique. »
M. Brand précise qu’à contrario, lorsque le site de production a été prévu dès le départ pour inclure un système de distribution pneumatique, les applications de manutention, de positionnement et de production en série ne gagnent pas à faire appel à des équipements électriques qui, selon lui, sont trois à quatre fois plus chers que les systèmes pneumatiques accomplissant les mêmes tâches.
« La pneumatique présente aussi l’avantage de pouvoir fonctionner dans les environnements industriels sans protection particulière, contrairement aux équipements électriques. En effets, des facteurs tels que l’humidité, les vibrations, la chaleur et les interférences électromagnétiques n’ont aucun impact sur les équipements pneumatiques. »
Dans ces conditions, peut-on considérer que l’automatisation pneumatique est idéale pour l’intégration aux procédés industriels modernes ? Pour M. Brand, cela ne fait aucun doute.
« Depuis 15 ans, la pneumatique a prouvé sa fiabilité en association avec les bus de terrain, les commandes embarquées et les fonctions de collecte des données et de diagnostic », déclare-t-il. « De même que d’autres technologies, la pneumatique moderne présente des capacités compatibles avec le passage à l’Industrie 4.0. Par exemple, les distributeurs intelligents offrant une communication IO-Link sont désormais une réalité dans les environnements industriels. »
Pour M. Sato, l’automatisation pneumatique présente l’avantage d’être simple : « L’air comprimé est l’un des plus anciens types d’énergie connus de l’homme. Il utilise l’air atmosphérique comme source, présent en quantité partout sur Terre. La production d’air comprimé est aisée, et la maintenance de ces systèmes sans complication. En outre, l’automatisation pneumatique garantit un fonctionnement sûr et fiable, dû en grande partie à sa simplicité. »
Depuis ses débuts, l’automatisation pneumatique a pour objectif de remplacer la main-d’œuvre dans le cadre de tâches répétitives, renforçant ainsi la productivité des opérations tout en réduisant les coûts de production. De façon générale, l’idée a toujours été de permettre la réaffectation des ressources humaines à des tâches plus gratifiantes comme la maintenance préventive, la programmation, l’amélioration des procédés et l’optimisation des produits finis pour renforcer la qualité et réduire les coûts, afin de gagner en compétitivité sur les marchés européens et mondiaux.
M. Sato prend l’exemple du VTEM (Motion Terminal), l’une des dernières avancées de la marque, pour illustrer la volonté de FESTO de moderniser régulièrement ses produits de technologie pneumatique.
« Le Motion Terminal repose sur le concept de ‘pneumatique numérisée’, c’est-à-dire la fusion de la pneumatique et de l’électronique associée à un puissant contrôleur logiciel pour créer un produit extrêmement innovant, capable d’assurer les fonctions de plus de 50 composants différents », explique-t-il.
« Le Motion Terminal est exceptionnel par sa capacité à offrir de nombreuses fonctions par le biais d’une seule vanne, contrôlée à distance par des ‘Motion Apps’ dont les paramètres peuvent être modifiés en temps réel. Via une plateforme unique, ce produit répond à tous les critères de l’Industrie 4.0 comme la flexibilité, l’efficacité énergétique ou encore la surveillance pour la maintenance prédictive. Il est donc idéal pour les futurs projets d’automatisation de l’industrie. La pneumatique numérique du Motion Terminal optimise les procédés d’automatisation. Ses avantages vont de l’accélération des phases de planification et de conception à la simplification de la mise en service et du paramétrage. Par ailleurs, il renforce la productivité opérationnelle en offrant un moyen plus simple et rapide de convertir ou de moderniser un système. »
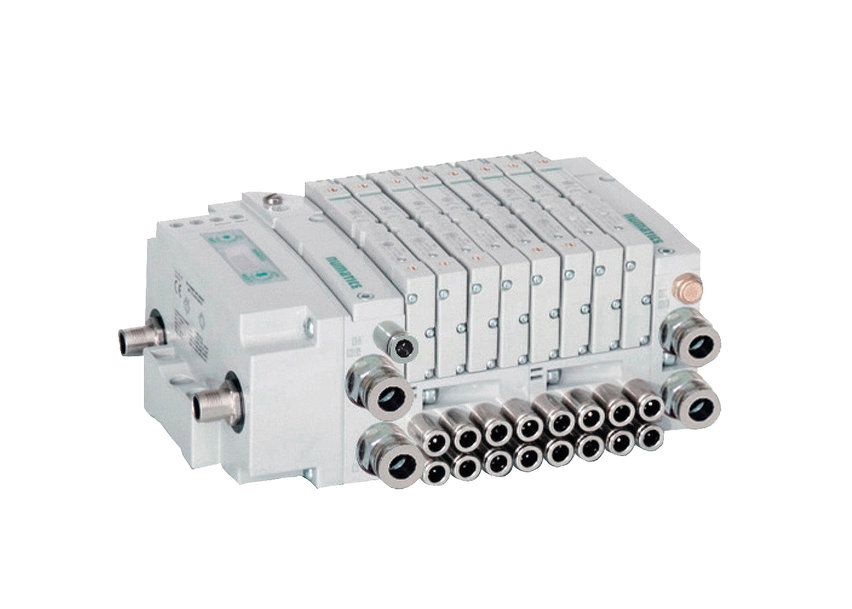
En résumé, l’automatisation pneumatique est bien établie au sein du marché, et ses ventes progressent continument. Son adaptation et sa contribution au nouveautés comme l’I-IoT (Industrial Internet-of-things – l’internet des objets adapté aux contraintes de l’industrie) ou l’Industrie 4.0 n’y sont évidemment pas étrangères. Et soyons assurés que les fabricants n’en resteront pas là !
La technologie IO-Link intégrée aux composants électroniques de la série 580
Les actionneurs pneumatique sont devenus communicants. ASCO-EMERSON a introduit la communication IO-Link pour ses composants électroniques de série 580. Cette technologie est compatible avec les îlots de vannes séries 501, 502 et 503.
La norme IO-Link (CEI 61131-9) a été conçue pour fournir une connexion simple et intelligente entre les entrées/sorties (capteurs/actionneurs) et le contrôleur à l’aide de câbles non blindés standard peu coûteux. De plus, IO-Link permet de récupérer les paramètres de diagnostic et de configuration.
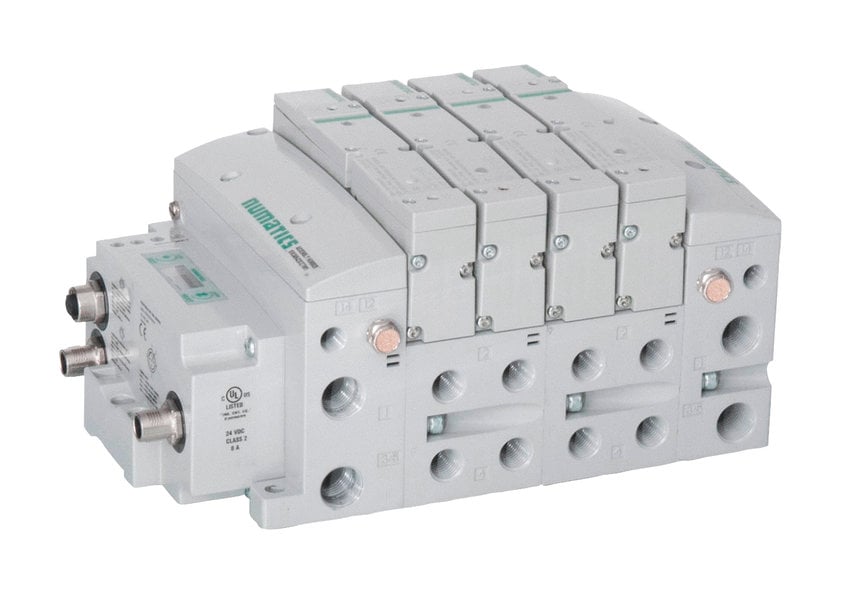
Principaux avantages
Les principaux avantages incluent la conformité à la norme internationale CEI 61131-9, qui garantit une communication entre différents équipements (interopérabilité). La productivité est également améliorée, IO-Link fournissant une communication des données numériques entre les équipements de terrain et le contrôleur.
Autre avantage : la réduction des temps de maintenance, les équipements IO-Link étant automatiquement identifiés et configurés en cas de remplacement. La gamme ASCO Numatics 580 IO-Link est aussi synonyme de gain de temps grâce aux caractéristiques suivantes : diagnostic des entrées/sorties mappées simple d’utilisation pour les programmeurs ; diagnostic basé sur les événements utilisant trois mots machines de moins (et traitement des données dans le cloud via un maître compatible) ; une solution économique en termes de matériel, grâce à l’utilisation de câbles non blindés et de connecteurs standard ; et flexibilité grâce à la compatibilité avec l’ensemble de la série 500 (501, 502, 503). ASCO-EMERSON peut aussi fournir sur demande des composants électroniques 580 IO-Link dans la série 2035.
La topologie d’E/S distribuées modulaire d’ASCO-EMERSON offre un débit inégalé pour cette taille de produit, ainsi que de nombreuses configurations possibles. Les embases permettent d’utiliser différentes tailles sur un même îlot. De plus, l’utilisation d’embases et d’accessoires permet d’utiliser deux pressions nominales différentes sur un même îlot sans régulateurs individuels.
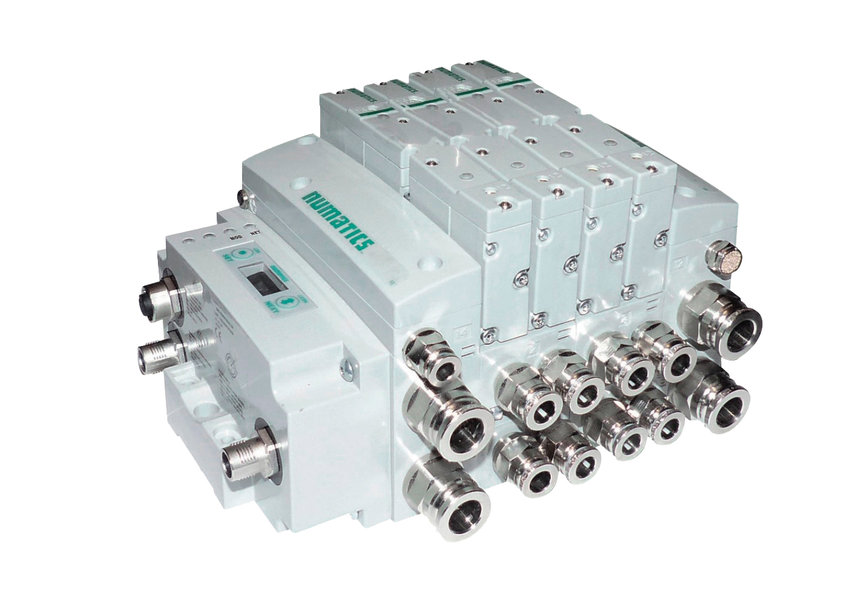
Secteurs et applications
La série 580 IO-Link est parfaitement adaptée aux concepts et applications modulaires dans lesquels les capteurs et les systèmes pneumatiques sont très proches les uns des autres (distance de câblage inférieure à 20 mètres).
Les scénarios d’utilisation typiques incluent les convoyeurs, les pinces de robot pneumatiques, les machines d’assemblage et les équipements de remplissage dans les applications agroalimentaires et cosmétiques.
www.asco.com
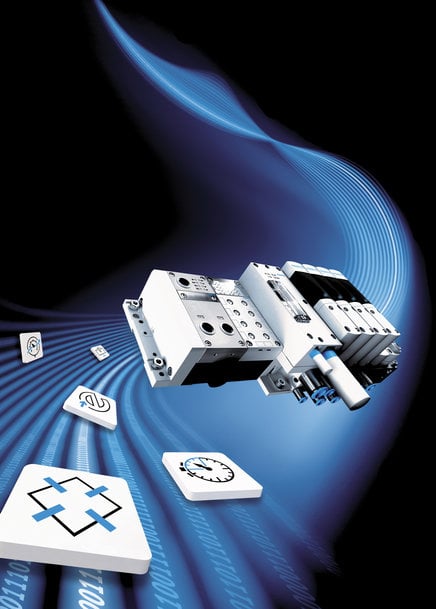
Motion Terminal : une innovation FESTO capable de remplacer 50 composants
Déjà bien établie, la technologie pneumatique s’apprête à devenir encore plus simple, polyvalente et flexible avec le nouveau Festo Motion Terminal VTEM. Ce produit marque le début d’une nouvelle phase de l’Industrie 4.0, avec des applications capables de remplacer plus de 50 composants différents. Ce résultat a été rendu possible grâce à diverses avancées en matière de technologie piézoélectrique et de logiciels.
Tout comme le smartphone a transformé le marché des communications mobiles, le Festo Motion Terminal va révolutionner les technologies d’automatisation et l’industrie dans son ensemble.
La nouvelle stratégie d’intégration des fonctions – associée à des applications logicielles – simplifie l’ensemble de la chaîne de création de valeur, puisqu’un seul équipement est désormais nécessaire.
La véritable Industrie 4.0
Avec la technologie piézoélectrique, des capteurs de course et de pression intégrés, associés à un système de commande via des ‘Motion Apps’, offrent de nouvelles perspectives pour les constructeurs de machines et d’usines. Alliant technologies mécaniques, électroniques et logicielles, le Festo Motion Terminal permet de transformer un produit pneumatique en véritable composant de l’Industrie 4.0 et de mettre en œuvre un système de production flexible.
La modification des fonctions pneumatiques et l’adaptation à de nouveaux formats sont contrôlées en ajustant les paramètres dans des applications. Les capteurs intelligents intégrés pour les tâches de commande, de diagnostic et d’apprentissage automatique éliminent en outre le besoin de composants supplémentaires.
Les applications à l’honneur
Lors du lancement du VTEM, dix fonctions étaient disponibles via les ‘Motion Apps’, de la modification simple des fonctions des distributeurs au mouvement à haut rendement, et du comportement proportionnel à différents profils de mouvement. Ce système se démarque par le fait qu’un seul et unique équipement est utilisé pour tout.
Grâce à l’activation rapide de nouvelles fonctions via les applications, les concepteurs peuvent créer un type de machine simple, puis sélectionner les applications nécessaires pour l’équiper des fonctions et caractéristiques couvrant les besoins du client.
L’attribution des fonctions via des logiciels présente en outre l’avantage d’éviter toute falsification des données, car il est impossible de l’extérieur de déterminer les fonctions exécutées par les vannes. La maintenance est également simplifiée grâce à l’élimination des longues listes des pièces de rechange et d’usure.
Efficacité énergétique intrinsèque
Les ‘Motion Apps’ développées spécialement pour le Motion Terminal et la fonction de diagnostic des fuites économisent de l’énergie pendant le fonctionnement. La technologie piézoélectrique à économie d’énergie au stade préliminaire de l’électrovanne joue aussi un rôle important.
La consommation d’air peut être adaptée de manière flexible à l’aide des applications de niveau de pression sélectionnable et ECO drive. Cette dernière règle la consommation d’air comprimé sur le minimum nécessaire lorsqu’aucune force de pression ou de maintien n’est requis en position finale. Selon l’application, cette fonctionnalité permet jusqu’à 70 % d’économies par rapport au fonctionnement normal.
Diminution des coûts et de la complexité
Le Festo Motion Terminal permet des mouvements rapides et puissants et offre un diagnostic des fuites à un coût bien inférieur à celui des systèmes actuels. Ainsi, le nombre de contrôleurs nécessaires est inférieur à celui des solutions électriques, un seul contrôleur pouvant réaliser jusqu’à huit mouvements avec le VTEM. La consommation d’énergie est également réduite, tandis que l’espace d’installation peut être diminué jusqu’à 65 %.
Si l’on compare les différentes technologies, les installations avec le Festo Motion Terminal offrent des alternatives véritablement économiques pour huit applications. Au lieu d’une vanne, d’un régulateur de pression et d’un capteur de pression, soit trois composants, un seul est requis : une vanne.
www.festo.com